Roadtec is offering a new cold recycling machine, the RT-500, aimed at duties in projects using the recycling train concept. Electrically powered by a Cat C9 generator set, the RT-500 can handle up to 600 tonnes/hour of material and is designed to crush and screen the recycled asphalt pavement (RAP) produced by an RX-900 cold planer. It has a JCI double deck screen that sorts milled material provided by the RX-900's conveyor. Any oversized material is fed back into the RT-500's Telsmith 3048 impact crusher
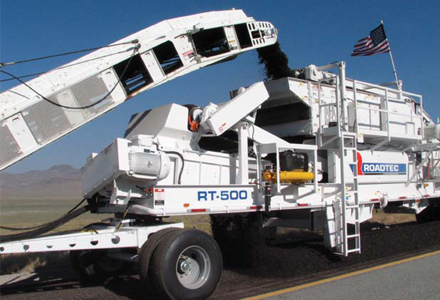
Electrically powered by a
Material that passes the screen drops onto a 1.22m wide weigh belt with an accurate electronic scale that communicates with the blending computer and adjusts the flow of additives going into the RT-500's JCI/KPI Model 52 pugmill twin shaft mixer with a capacity of 600tonnes/hour. After mixing the material is discharged in a windrow onto the roadway.
The Roadtec RX-900 cold planer provides the propulsion for the recycling train and tows the RT-500 cold recycler and a nurse tank for the emulsions, as well as a water truck and a slurry tanker. The RX-900 also pushes another emulsion tanker and slurry tank when they are present to refill tankers hooked to the train. Those two replenishing tankers are attached to the train long enough to pump off their products and then go to a staging area where they are refilled to return to the train.
A windrow loader also follows the train to pick up material and feed it to a conventional paver.