IROCK says that its RDS-15 mobile crusher suits duties in recycled asphalt applications. This horizontal impact crushing plant is said to be highly mobile and versatile. The rapid deployment system (RDS) the firm has developed is said to increase transportability from site to site and cut set-up times when the equipment arrives on-site. The RDS-15 is said to be ideal for processing smaller materials such as reclaimed asphalt pavement (RAP).
Versatile and compact, this crushing and screening system provid
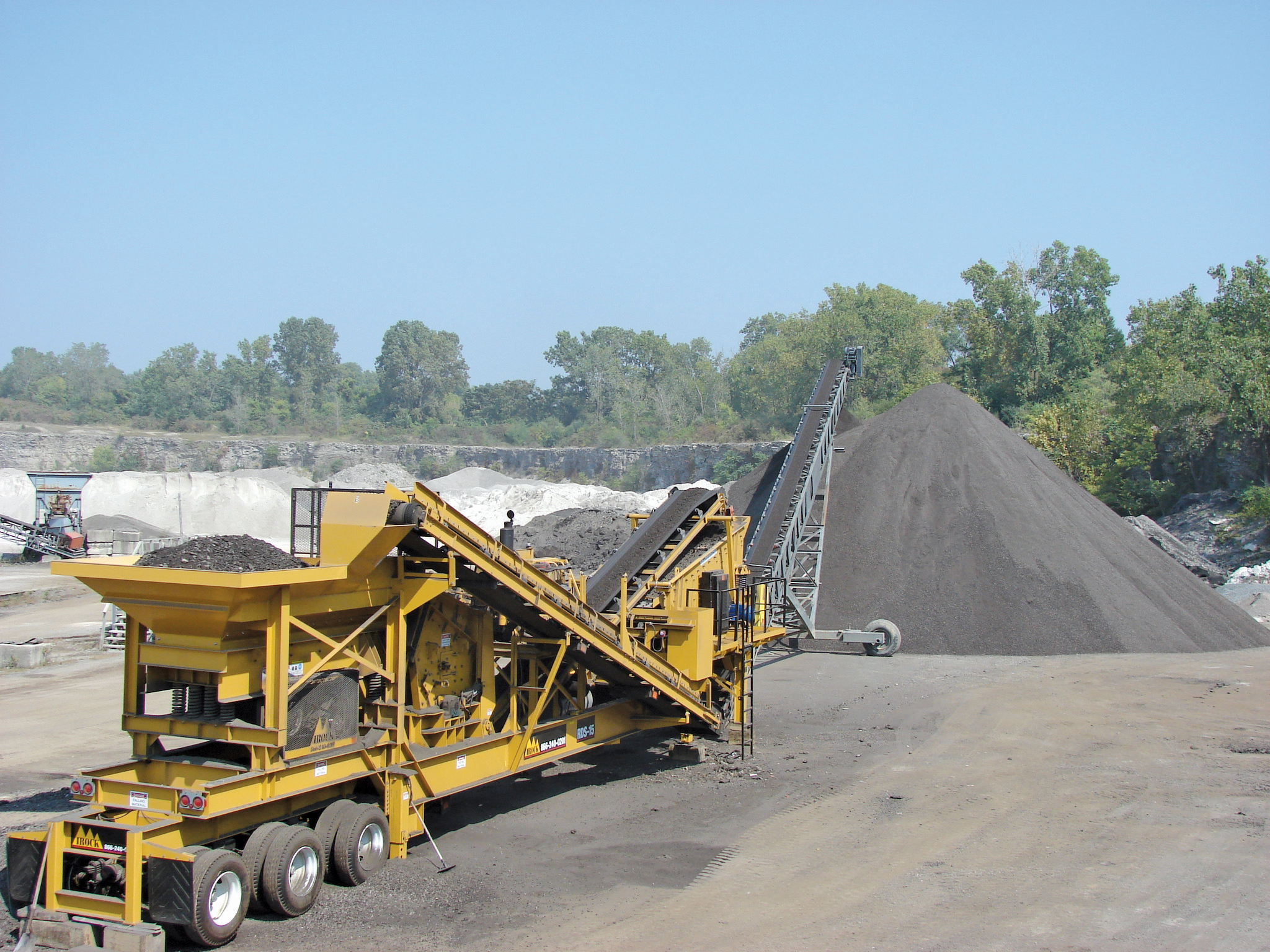
Portability and versatility are claimed by IROCK for its new RDS-15 crusher
IROCK says that its RDS-15 mobile crusher suits duties in recycled asphalt applications. This horizontal impact crushing plant is said to be highly mobile and versatile. The rapid deployment system (RDS) the firm has developed is said to increase transportability from site to site and cut set-up times when the equipment arrives on-site. The RDS-15 is said to be ideal for processing smaller materials such as reclaimed asphalt pavement (RAP).
Versatile and compact, this crushing and screening system provides increased efficiency and can be used to produce a uniform, high-quality product according to the firm. Power comes from a 261kWThe unit’s closed circuit design is said to allow operators the option to recirculate material requiring further sizing. By closing the flop gate, the two decks can feed onto the 610mm return conveyor, which drops the material back into the crusher. This design is claimed to increase production throughput by 20% over competing machines. The increase in working efficiency boosts production while lowering fuel consumption and general running costs. This feature is ideal for applications such as asphalt recycling, where contractors commonly need a consistent 12mm product. The machine features a 1.52x4.27m double-deck screen frame. By opening the flop gate, the machine can process, screen and separate up to three different sizes of materials, two sized and one crusher run.
Within the full-length fabricated steel plate hopper, the unit features a heavy-duty, 1.02x4.27m vibrating grizzly feeder. The two-step, tapered grizzly removes fines and only allows materials that need to be sized into the crusher, reducing potential wear on the crusher and further boosting efficiency. While operators have an option to add
Performance and production are improved by IROCK’s four-bar impactor design. The RDS-15 provides the ideal balance inside the crushing chamber to optimize production and ease uneven wear on the blow bars. Blow bars can be removed, flipped and reinstalled for a second lifecycle. Adjustable aprons are used to control the size of the crushed material.
IROCK’s exclusive ROCK BOX uses a shelf system with AR-400 steel wear bar. An innovative alternative to discharge chutes found on similar units, the ROCK BOX allows crushed material to build up and act as a wear liner, effectively reducing maintenance and cutting down on wear part use. IROCK incorporates special AR-400 steel plate liners for each material transfer point, which provides better durability than conventional rubber liners.
To reduce cleaning and maintenance requirements, the RDS-15 features a standard dust suppression system. For further protection from dust and vibration of normal operating conditions, operators can remove the machine’s control panel for operation from up to 10m.
This mobile crusher can also be hooked up to a truck and hauled as one unit. In addition, catwalks enable easier screen change-outs and provide convenient access to key maintenance and cleaning points.