New technologies allow efficient use of recycled asphalt - Mike Woof writes The Eurobitume/Euroasphalt 2012 event in Istanbul earlier this year proved an important event with regard to asphalt recycling innovations. Key developments in this technology were announced, particularly in the field of asphalt production. One of the notable papers came from E-MAK, part of the Turkish Simge Group, which focused on its RATEK system. This technology is designed to use recycled asphalt and can produce greater throughp
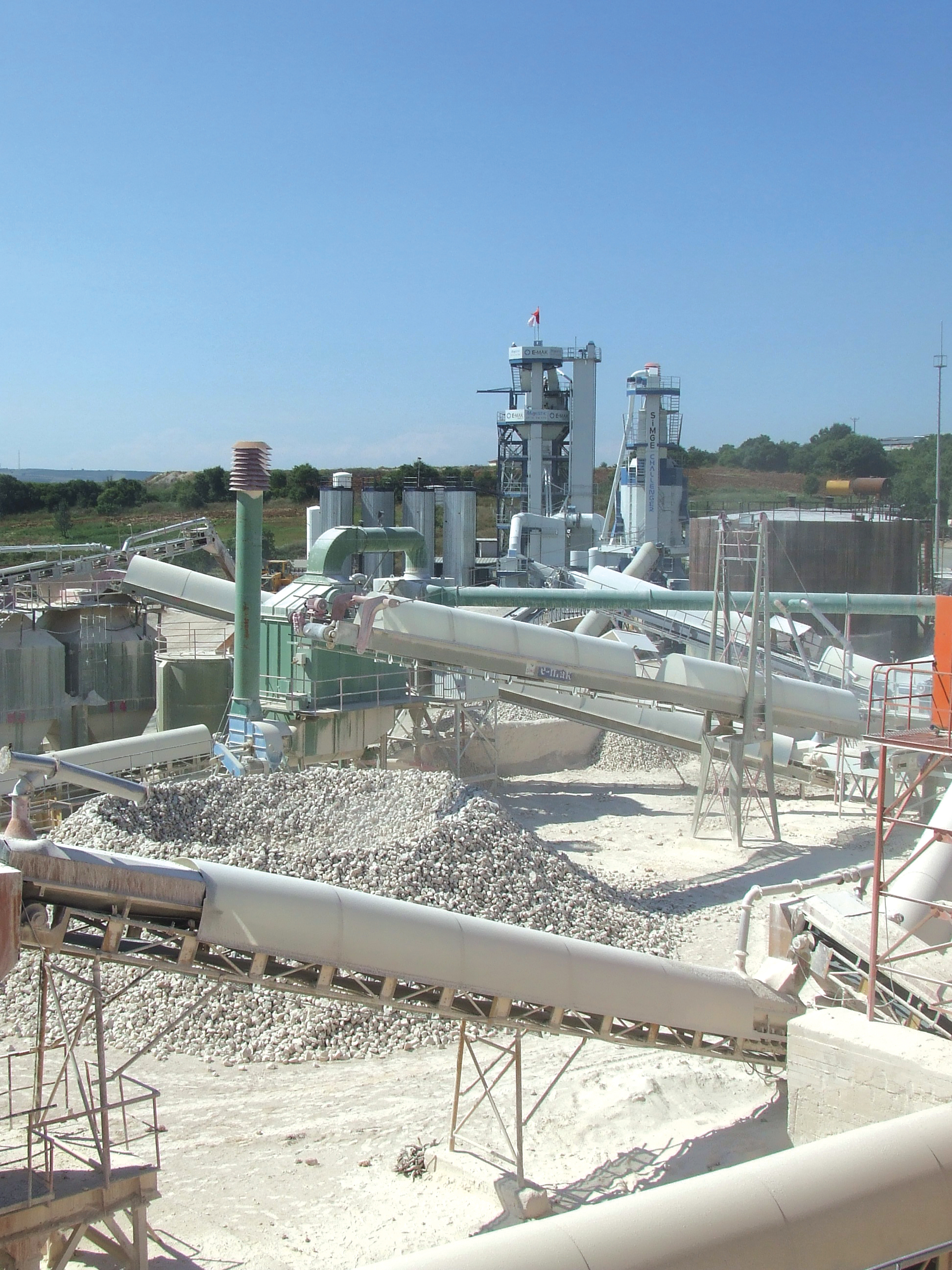
The innovative RATEK plant developed by the Simge Group offers efficient processing of RAP
New technologies allow efficient use of recycled asphalt - Mike Woof writes
The Eurobitume/Euroasphalt 2012 event in Istanbul earlier this year proved an important event with regard to asphalt recycling innovations. Key developments in this technology were announced, particularly in the field of asphalt production. One of the notable papers came fromEmre Gencer, marketing director at the Simge Group presented the paper and explained that the RATEK plant avoids the use of direct heating, which can damage the valuable bitumen as well as cutting out the problem of fumes. The indirect heating reaches temperatures of 650°C at the burners and enters the heart of the RATEK plant, with its innovative triangular profile, at a temperature of around 400°C after mixing with cold air. By the time the RAP meets the hot air within the plant the temperature drops to some 120°C, which prevents damage to the bitumen. Gencer said, “We create a heat sandwich.”
The design of the RATEK system allows the RAP to be heated for around three times longer than for conventional plants, delivering an efficient heat transfer process that also helps reduce fuel consumption/tonne of material produced. The internal design of the RATEK also minimises the problem of materials sticking that can affect conventional plants and lead to a need for periodic shutdowns for cleaning and maintenance.
The system also features a separate pre-mixing stage for the RAP, which can then be used for a base course material. But for binder course or wearing course grade asphalt, the feed from the RAP pre-mixer is then fed into a secondary mixer and combined with virgin materials. This two-stage system itself brings savings as costly anti-ageing additives can be combined in the initial mixing process, without having to be added into the secondary stage along with the virgin materials. By this method, the quantities of anti-ageing additives needed for a binder or wearing course mix can be reduced, cutting production costs. Overall, Gencer said that the RATEK plant offers several important benefits as it uses indirect heating that does not damage the binder and can produce larger quantities of quality asphalt using RAP than conventional systems. At the same time the Ratek plant also reduces fuel costs, emissions and the quantities of anti-ageing additives required.
A paper at the event also highlighted the benefits of using recycled asphalt based on experience derived in the German city of Hamburg. Faced with heavy traffic loads, the need for shorter construction times and budget constraints, the Hamburg road authorities have carried out a series of trials in the city with seven tests stretches being laid since 2010. The first initial tests with RAP were carried out in Hamburg as far back as 1983, but the technology was limited and only now does the methodology offer an efficient and reliable solution. The higher the bitumen content, the higher the value of the material. Meanwhile Hamburg has also managed to save some 19,000/year in fuel costs by simply roofing over the material storage area for the RAP, which prevents moisture ingress.
Some changes to operating methods are required and it is important to have separate milling operations. This allows materials to be separated by grade and achieves the best value from the material. This can have a significant benefit on quality and in one trial, 90% of the materials used in a wearing course came from a high quality RAP that had been specially stockpiled, offering significant cost savings. After two years of heavy use, this section of road is still performing well and the authorities are planning further projects in the city as a result.