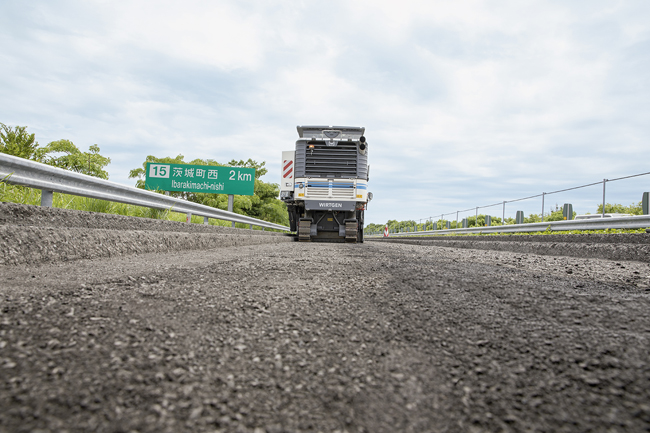
The W 210 mill was used to plane off first the wearing course and then the binder course of the Jõban Expressway.
The W 210 model with its 500kW diesel proved productive for the contractor, Unite Co, removing the two worn surface layers with its 2m-wide drum in just two hours, while traffic flowed in the lane alongside. The firm had a good reason to select the Wirtgen machine for the job, and not just because of the unit’s productivity. “Our machine is equipped with the Vacuum Cutting System (VCS),” explained site manager Koji Yamada.
Five years ago, the VCS vacuum cutting system developed by Wirtgen was included in the New Technology Information System (NETIS) of the Japanese Ministry of Land, Infrastructure, Traffic and Tourism.
To repair cracks in the road pavement, the large milling machine was equipped with a standard milling drum. After removal of the 100mm-thick surface course, the W 210 cold milling machine milled the binder course to a depth of 150mm in a second pass. Both passes were carried out at an advance rate of 7m/min.
Removing the two layers separately allowed the contractor to ensure that the milled material could be recycled more effectively. The recovered cuttings could be returned to different storage areas, allowing them to be used for different mix grades containing RAP by the asphalt producer. This helped deliver a cost-effective solution for the contractor, ensuring better quality control for the asphalt plant.
The performance of the machine also benefited from its load-dependent water sprinkling system. Water required for cooling the cutting tools is regulated in accordance with the engine load and cutting speed on the latest milling machines. The water system switches on automatically when the milling drum lowers into working position and automatically switches off when cutting stops. This helps reduce water consumption by up to 20%.
At the same time, the water cooling system helps extend the service life of the cutting tools. Meanwhile, reducing water consumption means that the machine requires fewer refills. Downtime is minimised primarily as cutting tool life is extended, but also as the time between refills of the water tank is longer.
Another important feature crucial for re-use of the RAP is that the residual moisture of the milled material is only 3–4%/tonne. With less advanced milling technology the residual moisture will generally be around 5%, requiring more energy to dry out the RAP when it comes to using the material at the asphalt plant.
When producing asphalt, a simple rule applies to the drying process at the mixing plant. Reducing the moisture content of the feed by 1% will save around 1litre of heating oil when producing 1tonne of asphalt. In addition, this reduction in moisture content will also deliver a reduction in CO2 production from the plant.
The contractor estimates that for the Jõban Expressway project, the lower moisture content of the milled material helped deliver a saving of some 400litres of heating oil when reusing the RAP at the asphalt plant.
Yamada added that the quality of the milled surface was also high due to a combination of the machine’s water spray system and its sophisticated levelling control. This helped to provide a smoother surface for paving and compaction, further reducing materials costs as the contractor did not have to smooth out the milled finish using more material in the base course.
According to Wirtgen, reducing water consumption in its milling machines helps to deliver a significant saving in overall fuel costs for the asphalt plant. And delivering a quality milled surface further reduces material costs for the paving contractor.
At the Jõban Expressway site, the contractor milled an area of 800m2 to a total depth of 250mm, producing 200m3 of RAP. Assuming that this 200m3 of RAP has a density of 2.47tonnes/m3, then the asphalt producer was able to save some 500litres of heating oil at the plant as a result.