With an operating weight of 27tonnes, the BM 2000/65 is the lightest planer currently available in the 2m class. The firm says that this low weight has been achieved by a special lightweight design as well as a shorter conveyor belt that now make the planers even more flexible to use. Operating characteristics include efficiency, ease of operation and safety, according to the firm.
Planer productivity depends on the integration of all components. The operator has to monitor all parameters from the control station, from the cutting edge to the conveyor belt. In the new BM/65, good visibility has been optimised. The front of the machine features a slim design while the position of the operators platform is said to make it easy to work precisely and safely. The flat rear profile also improves visibility and site safety when manoeuvring. A camera system provides visibility in areas out of direct sight from the operator platform. The control platform itself can be moved by up to 200mm, allowing the operator to view the right cutting edge and the side plate.
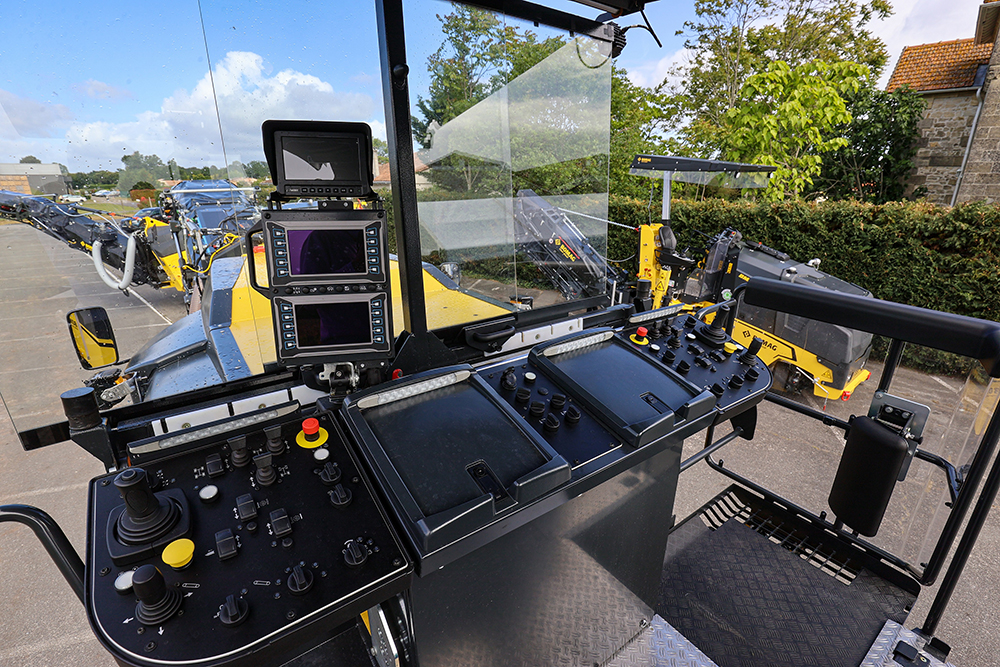
The slim design allows a turning radius of only 1.7m, boosting manoeuvrability: the planer is said to have the smallest milling radius in the 2m class. Featuring the latest generation conveyor belt with a 130° swivel angle, the planer is efficient at truck loading, even when milling mini-roundabouts.
The low operating weight of 27tonnes has been achieved by the lightweight design of the machine and milling box. The low weight improves versatility and simplifies transport approval processes. If greater weight is required, optional ballasting of up to 1.8tonnes can be added.
When collapsed, the BM/65 has a 650mm shorter conveyor belt than other planers in the 2m class, also making transport easier.
The new control system is said to make machine settings quick and easy to access, while sensors and assistance systems are all easy to select and use. All relevant information is presented on the two rugged full-colour displays.
The six-cylinder 477kW engine complies with Stage V and Tier 4 Final emissions standards, as well as being highly efficient.
A key performance feature is the efficient cutting design with a wear-optimised BMS15L exchange holder system that saves 20% fuel and extends the service life of cutting tools.
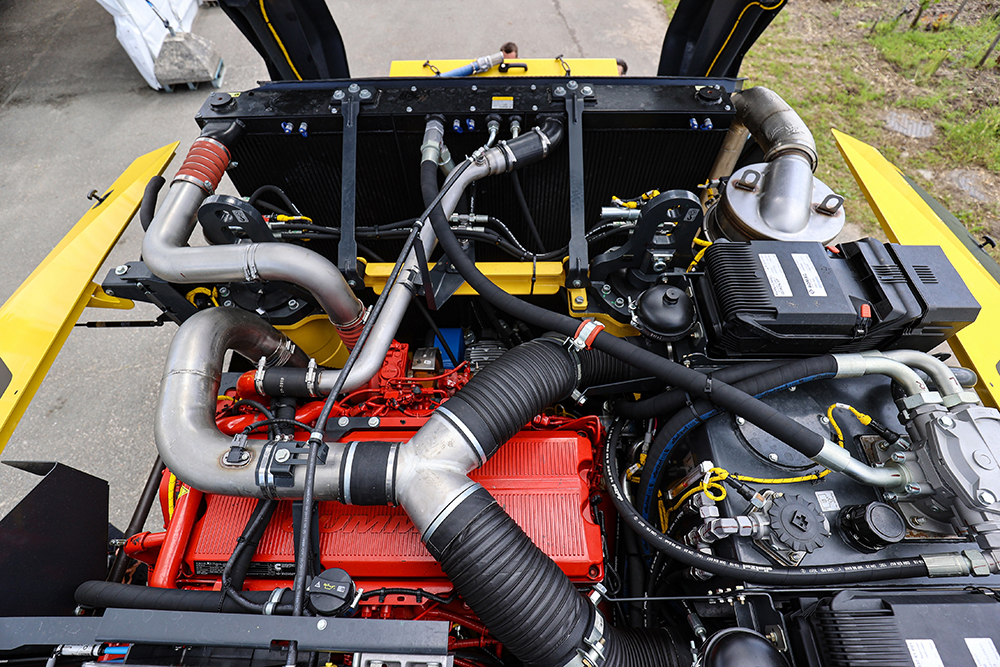
Equipped with the firm’s novel Ion Dust Shield, the BM/65 renders fine dust particles with a grain size of less than 10μm harmless. The Ion Dust Shield technology transforms fine dust particles by means of electrical charging into harmless coarse dust that can be easily removed. This has been proven to reduce particulate matter by 80%, ensuring cleaner air and protecting crews, residents, and passers-by. As a result, the Ion Dust Shield also contributes to significantly lower fine dust pollution during milling for the 2m class. The improved sealing and low-wear design also made it possible to create a particularly low-dust working environment for the operator.
The water tank has a capacity of 3,250litres, while the two-part spray bar is designed to optimise consumption and reduce water wastage.
The water system, hydraulic valve block, milling drive and oil filter can all be reached via four easily accessible maintenance flaps. Engine and hydraulic filters can be changed safely and conveniently from the operator’s platform. The machine's modular design enables each unit to be checked, serviced or replaced individually. This shortens diagnostic, service and repair times. Diesel and AdBlue can be filled directly from the operators platform.