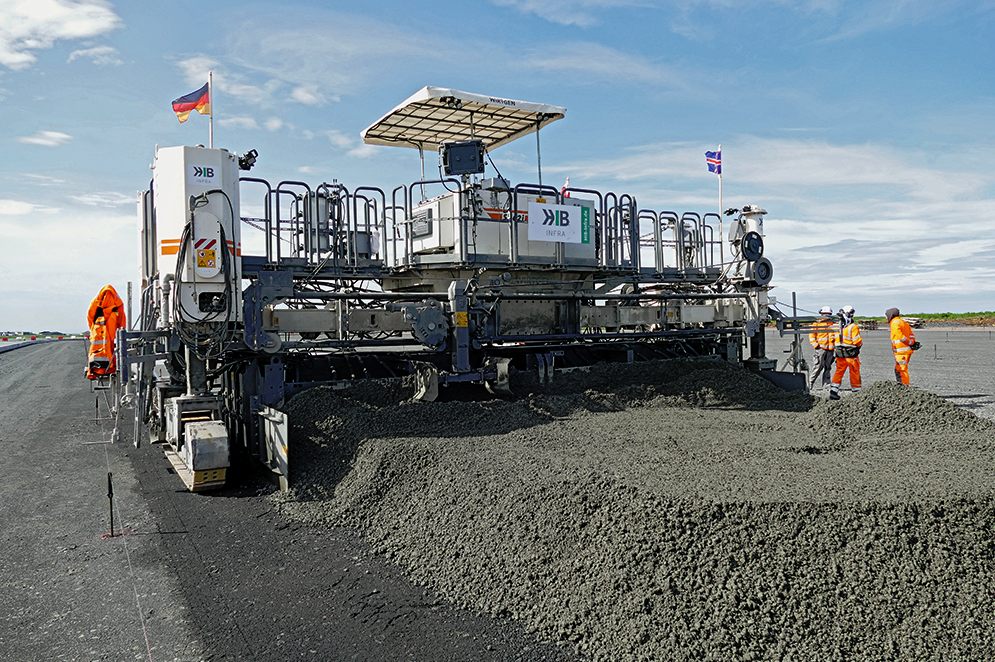
Concrete paving was carried out using a Wirtgen SP 62i model at Keflavik Air Base, with the machine laying 75,000m² of operational facilities.
The project involved the extension of the apron and a hazardous cargo pad at the military air base on the international airport at the port of Keflavik, 50km from Iceland’s capital, Reykjavik. The overall project was commissioned by the US Government.
At the end of the construction project the SP 62i had paved a total of 35,000m³ of single-layer concrete paving with a width of 7.62m and a thickness of 41-45cm. On average, 900m³ of concrete was paved/day.
Due to the climatic conditions on the Reykjanesskagi peninsula in the south-west of Iceland, the time window for the project was set for the beginning of July to the end of September of 2021. To squeeze the work into this timeframe, the decision was made to do without prior placement of fixed formwork for the individual strips.
Despite the tight deadline, the paving team was able to deliver high-quality results, with the machine’s high-precision steering and levelling system and the automatic super smoother playing important roles.
Operational areas on airfields generally have only a very slight cross-slope and, in Keflavik, the specified value was 1%. The area was paved in 31 separate strips that were connected to one another by tie bars inserted along the sides to ensure the correct height of the individual sections. The outer edges of the strips posed a challenge for paving with the slipform method. These had to be perpendicular from end to end and paved with no fall. This is to ensure that rainwater drains away during future operations, and that no water collects in the expansion joints.
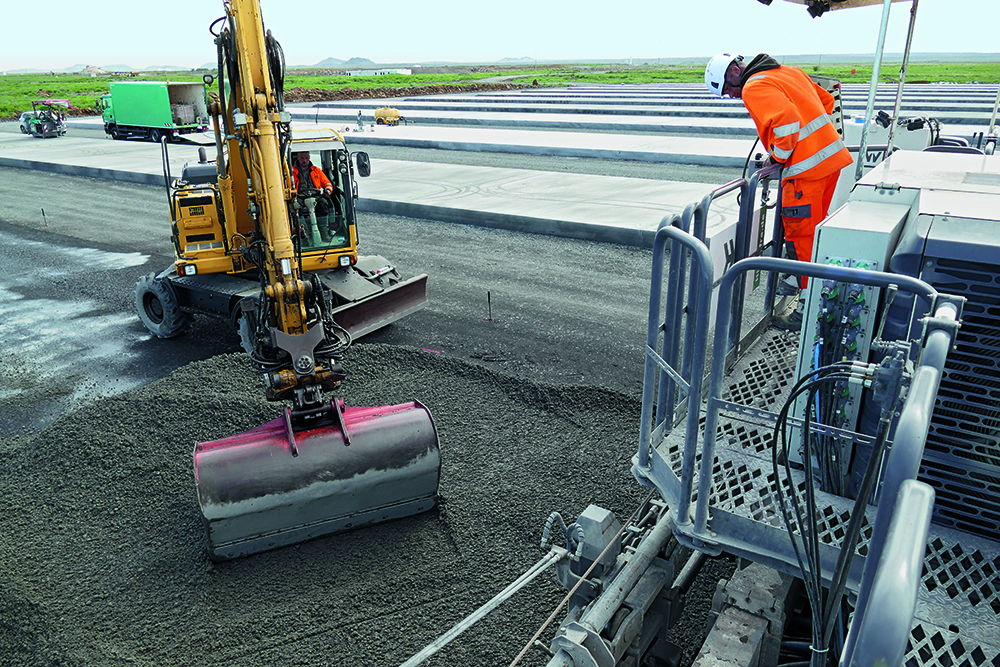
In order to fulfill the future load-bearing and wear-resistance properties of the construction in question, additives and a precise consideration of the concrete ingredients was needed. The required properties in the case of the extension work at Keflavik Air Base included a concrete with the compressive strength class C35/45. In order to achieve the desired compressive strength of 45N/mm², the ideal formula for the concrete mix was determined with the assistance of Wirtgen application engineers and optimised for paving with the slipform paver.
In situ paving of the first pilot strips was able to begin without trial areas. These showed optimum quality in all specified parameters such as density, compressive strength, profile-compliant placement and surface roughness, such as grip characteristics.
When it comes to the operational areas of airfields and airports, demands for surface evenness are generally very high. At Keflavik Air Base, the specified maximum permissible unevenness was 4mm on 4m. The evenness measured according to the TP Eben 2007 technical testing regulations for evenness measurements on road surfaces in longitudinal and transverse directions showed that deviations were lower and that the evenness achieved was better than the target value.
Quality can only be achieved with a coordinated team and the right equipment, as Hendrik Wendt, site manager & concrete technologist, HIB Infra explained. He said that the team from Wirtgen provided important advice and support in both the planning phase and as onsite consultants. He said, “Not least thanks to this, we were able to complete the project on time with as good as no problems at all on the construction site.”
The new parking apron at Keflavik Air Base measures 280m long by 235m wide, while the hazardous cargo pad measures 120m long by 76m wide.
The specified cross-slope is ≤ 1%, while the paving width is 7.62m and the paving thickness measures from 41-45cm. The equipment was able to achieve a daily paving performance of 900m³ and deliver an overall paved surface area of around 75,000m².