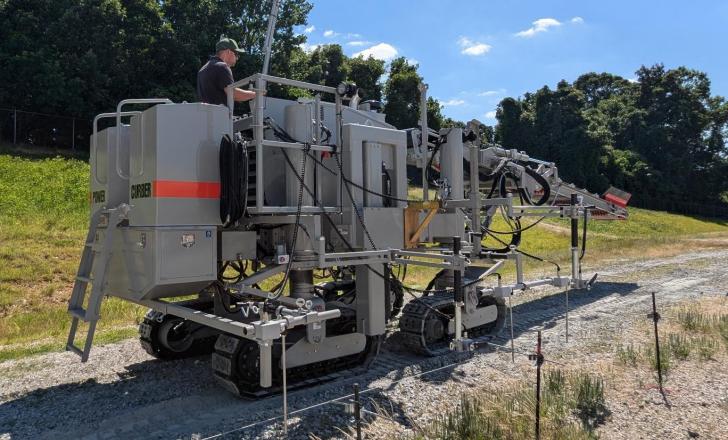
Power Curbers is developing its 5700-D concrete slipformer to meet customer demand, offering an industry first with an optional enclosed cab as well as a version aimed at European customers.
The new cab offers a fully-enclosed operator’s platform with air conditioning and heating to boost comfort during extreme temperatures. The cab also has a novel glass floor insert, positioned to offer provide visibility of both the mold and the finished concrete. This allows operators to make adjustments as needed, improving precision during a pour. The cabin has two exterior doors, for access to both the front and rear of the machine.
Operators will benefit from a quieter working area with reduced engine noise and the cab also shields the control panel from direct sunlight, maintaining a cooler temperature for switches and reducing glare on the display.
Meanwhile, company president Stephen Bullock said that the firm is also offering a new version of its successful 5700-D slipformer, particularly for customers in Europe.
The firm has modified its existing, three track, 5700-D model to run on four tracks. Bullock said, “This is just to reach that market that wants a four track machine.”
He said that some customers prefer the perceived stability of the four track configuration, while others are more keen on the tighter turning and more compact features of the three track layout. With this development, Power Curbers is now able to meet both preferences. For ease of transport it has a folding belt conveyor. Other specifications such as the wide range of molds, the ability to work with stringless controls, its maximum slipforming height or paving width are the same as for the three track machine.
To further boost the versatility of the new 5700-D4, the machine can be switched quickly between paving on the left and right sides. Bullock said that this is another feature often preferred by customers in Europe. However, he added, “It’s available now.”
In addition, Power Curbers has been awarded the 2024 Continuous Improvement Award by the North Carolina Manufacturing Extension Partnership for its manufacturing processes and organisational excellence.
To achieve this, the firm took a deep look into its processes to identify areas of improvement. The company also provided extensive training in lean principles for its employees. These efforts provided a workplace where the team looks for process improvements.
This process has taken many years, starting with manufacturing and then extending the practices to other business areas, including lean accounting, striving to apply lean principles comprehensively throughout the organisation according to Bullock.
“It took concerted efforts throughout the first year to embed this mindset across the organisation and gain genuine buy-in. The objective was clear: embracing continuous improvement wouldn’t jeopardise job security but enhance our success,” said Bullock.
By implementing lean tools and practices, Power Curbers improved productivity, safety, and efficiency. Organising and standardising workspaces reduced accidents and increased productivity. The firm also held targeted events to solve specific problems, which led to quicker deliveries and increased sales.
With lean principles in place, operations became smoother and more organised. The firm improved inventory management and workspace organisation, improving efficiency and cost savings.
“Our inventory management underwent a significant overhaul. We realised the cost implications of excess inventory sitting idle on shelves and devised a coherent system to optimise inventory levels. This shift has improved efficiency and reflects our commitment to continuous improvement and operational excellence,” said Bullock. To ensure these improvements lasted, Power Curbers standardised processes and implemented visual management systems. The firm also continued to find ways to improve, such as adopting just-in-time delivery for parts to streamline production and improve cash flow.
“The just-in-time approach allows us to streamline our production process, from receiving raw materials to shipping the finished product, ensuring optimal cash flow. By adopting single-piece flow instead of batch processing, we avoid the accumulation of excess inventory and minimise the time between production and payment. This shift has improved our cash flow and overall operational efficiency, contributing to our success,” said Bullock.