Concrete slipforming technology offers long term roadway and barrier construction with new technology now available - Mike Woof reports With road construction investment being seen around the world, concrete slipformer manufacturers are seeing strong export sales at present. New models are coming to market also with manufacturers continuing to broaden ranges by offering additional features and capabilities. US concrete paving specialist GOMACO is benefiting from extensive worldwide sales, with its long term
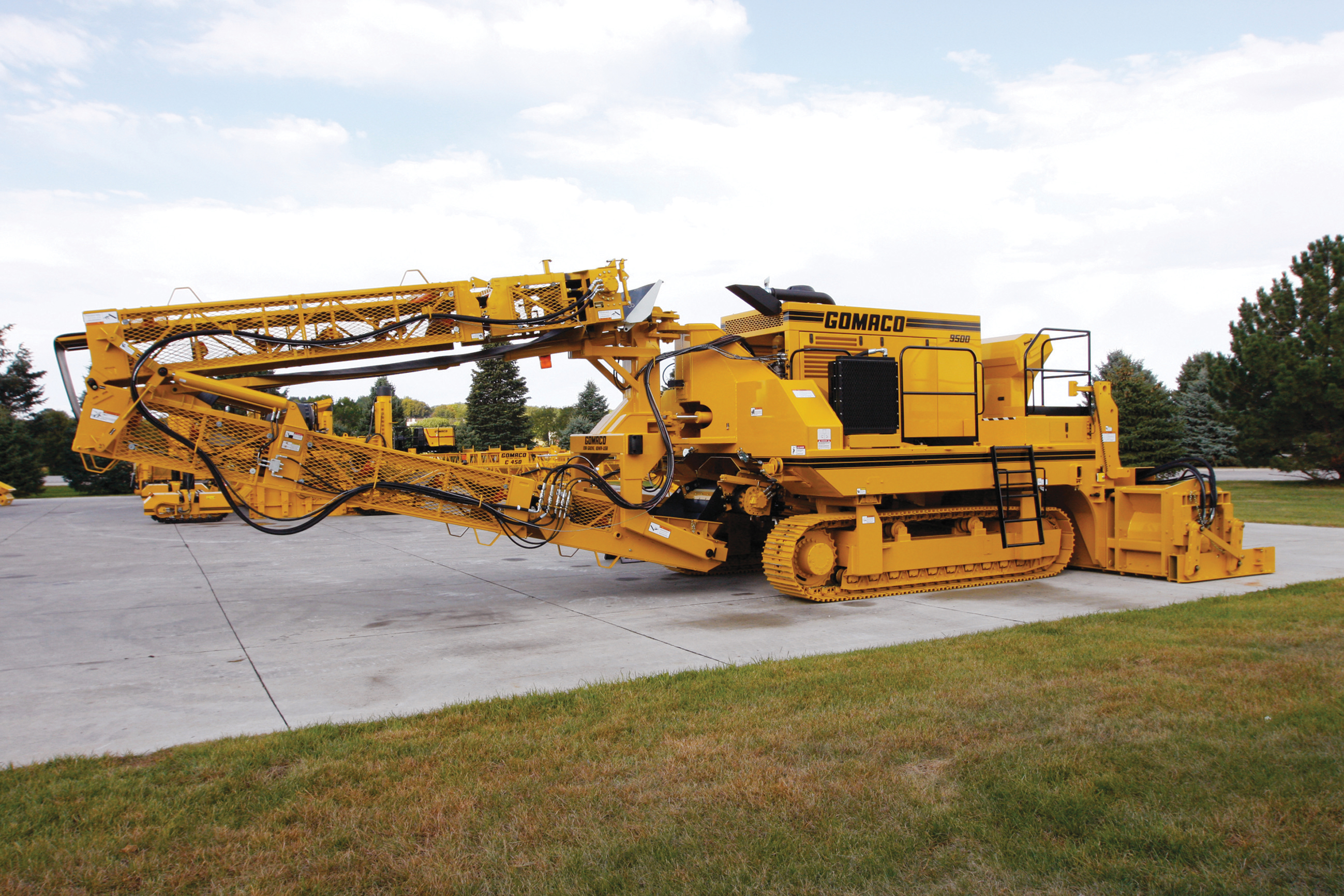
The folding conveyor system on GOMACO’s 9500 materials handler was developed to a specific customer request
Concrete slipforming technology offers long term roadway and barrier construction with new technology now available - Mike Woof reports
With road construction investment being seen around the world, concrete slipformer manufacturers are seeing strong export sales at present. New models are coming to market also with manufacturers continuing to broaden ranges by offering additional features and capabilities.
US concrete paving specialist218 Gomaco is benefiting from extensive worldwide sales, with its long term operations in Russia proving particularly fruitful. The company has been active in Russia since the 1980s and currently has units operating at Sochi, on the Moscow-St Petersburg highway and also at various airports. With the Russian authorities having announced a preference for concrete highways, the company looks set to gain more business while its long term presence in the country gives it a considerable advantage.
The company is also offering additions to its model range, such as an update to its well-proven and highly versatile 9500 material handling machine. This unit can be used as a trimmer, concrete and asphalt placer, and a shoulder trimmer. It is now available with an optional hydraulically-folding rear conveyor belt for improved transportability. The new option allows the conveyor to remain attached to the 9500 for transport and when folded up the machine is just 12.7m long by 3.5m high.
This option was developed following a specific request from a contractor. And as part of the redesign process, GOMACO engineers rebuilt the 9500’s conveyor to be stronger and more rigid with a truss-style framework. The switch controlling the hydraulically-folding rear conveyor can be placed at different locations on the back of the machine, which improves visibility and safety. The belt width is the same as the standard unit at 914mm while the rear conveyor maintains its 160° swing with hydraulic height adjustment up to 3.7m. It has a 10.6m long reach during machine operation, with a conveyor belt speed of 153.6m/minute, which allows fast placing of concrete or removal of trimmed material.
The two-track 9500 is equipped with a front-mounted trimmerhead that also offers several benefits to users. This allows trimming to the end of each pass or close to front obstacles. The powerful single-drive, hydrostatic motor offers high production as well as fewer connections and parts. Time savings are also claimed for the 9500’s quick-detach design of the trimmerhead, which has machine-mounted pick-up arms and can be quickly and easily loaded on the truck for transport.
The 9500 has a trimmer load control that controls the travel speed and ensures optimum power at the trimmerhead. By controlling travel speed a contractor can ensure accurate trimming and in addition, the 9500 was designed to offer job-site mobility and manoeuvrability. The machine can make a 360° turn within its own length and is also said to be user-friendly and safe to operate, providing good all-round visibility of the site. Other features include a remote control handset, emergency stop buttons located on strategic areas of the machine, a back-up alarm, an alarm for conveyor swing, and a rotating beacon on the rear conveyor.
At the same time, GOMACO’s rear-loading, front inserting 5400 series bar inserter is now available on the 3100 and 5000 series molds with a self-supported transition adjustor. Previously, the 5400 bar inserter was only available with the 5400 series mold. The inserter mounts to a T-bar, which is bolted onto the front of the 3100 or 5000 series mold, while the bar loading chain system is supported by a stand in the rear of the mold. It can be retrofitted to any existing 3100 or 5000 series mold in the field with a self-supported transition adjustor.
The GOMACO?5400 series bar inserter loads from the safety of the work bridge on the back of the paver. The system inserts the bar in front of the mold and has a chain feed system that allows the bars to travel in a flat, horizontal path, offering a high degree of reliability and efficiency. With the inserter mounted to the mold, on-the-go crown changes can be made while still maintaining constant bar depth. Individual guides on the right and left side of the inserter keep each bar parallel to the top of the slab while smart cylinders control depth of placement. The GOMACO exclusive G+ control system is used to control the bar insertion process and timing and the monitor features a magnetic mount that allows it be placed anywhere on the side of the paver for visibility of the working area.
The system can place bars from10-25mm in diameter and between 508-1016mm in length. A box for the bar bundles is mounted to the back of the paver allowing easy loading of the bundles and also easy access to load the bars into the bar magazine. One crew member can work from the paver’s work bridge loading the bar magazine on one or several 5400 series bar inserters.
Another firm benefiting from worldwide sales is307 Power Curbers, according to Stephen Bullock, vice president sales. He said that the firm is now benefiting from its export business, although market demand has improved again in the US. He said, “We have a pretty good forecast.”
The company has done well from overseas working and Algeria’s East-West Highway project was a deal for the firm. Bullock said, “We had dozens of machines on that highway. For every km of road there was 4km of barrier.”
He explained that the highway features two centerline barriers plus barriers on the outside as well, to prevent herds of goats or cattle as well as any wild animals from straying across the highway. This is just one of several projects in North Africa where the firm has supplied machines, with another 5700C slipformer being used to build centerline barrier for the upgrade to the Cairo-Alexandria highway in Egypt for instance.
With the firm’s home market having been weak, exports have been crucial and Bullock said, “In mid-2010 we shifted everything to our international business.”
Certain countries have been particularly good for concrete slipformer suppliers in particular and Bullock said, “Ecuador was one of those markets. The government said it wanted to go concrete.” He added that sister firm Power Pavers sold nine machines to Ecuador on that basis.
Meanwhile Asia has been a good export market for Power Curbers and sister firm Power Pavers. Vietnam has been particularly healthy although Bullock added that other Asian countries are also seeing increased paver sales and have further potential, “The Philippines made a shift to concrete a year ago.”
While Power Curbers is active in China, this market is still comparatively small. He said, “We’ve not seen a shift to concrete at this point. We’ve sold some 5700s but for kerb and gutter work.”
And the company does not consider the risk of Chinese copies to be a serious threat. Concrete paving is a niche market with comparatively low volumes that is unlikely to prove interesting commercially to Chinese manufacturers interested in selling volume products.
But the shift away from the US has required all the players in the sector to change focus. When the US market is good it accounts for around 50% of slipforming business according to Bullock. But business is good in the barrier sector though and he added, “There’s so much barrier work nationwide. We’ve sold so many machines for barrier jobs as opposed to kerbing.”
The company is also now offering stringless technology with its machines and Bullock said, “We have delivered a machine with stringless technology and it’s off to a great start.”
This first machine is being used by a contractor in Florida and is equipped with a control system from265 Leica Geosystems. However Power Curbers is leaving the choice of control package to the customer and is supplying machines with the rival 342 Topcon paving control package too. Bullock added, “We have tested the Topcon system and we gave the green light to that.”
The machines from sister company3975 Power Pavers have historically relied on conventional hydraulic systems but Bullock explained, “Over the last year our engineers developed electronics and they are ready to go with the Leica system now.” He added that new machines from Power Pavers will also be able to use Topcon paving controls shortly.
Bullock added the sales potential for stringless controls is greater with the Power Pavers machines than those from Power Curbers. “Paving is straighter than kerb and gutter, which has more curves so has more complex algorithms.”
He continued, “We did have good results with the Leica (Geosystems) control. It was right on the money and we were a little surprised at how good it was. The steering was fine, even though that’s the biggest challenge.”
But Bullock said that the tests with the Topcon package have proven equally successful and added that the firm is offering both as options and leave the choice to the client.
The firm’s most recent range addition has been the C-Max, a further development of its 5700 slipformer. This extends the capabilities of the base machine and Bullock said, “The C-Max exceeded what we thought it’d do.”
Enquiry levels are good for this unit for export, while two C-Max units have been sold in the US.
Meanwhile the 1700 model from Power Pavers was introduced last year and demand has been healthy from developing countries for this unit, which can pave 3.65m wide. Compact slipformers have advantages particularly for use in developing countries and Bullock said, “A small machine works well from a traffic point of view and is also better from a concrete supply perspective.”
The Power Pavers models offer greater sophistication than before and Bullock said, “We still have hydraulic controls as the base option but we also have digital controls and 3D systems to do more complex jobs.”
From3956 Terex Roadbuilding comes the updated SF3500C paver, which features 660mm diameter main frame tubing and is said to deliver structural rigidity at extended paving widths. Its Series 6 paving kit has a wedge and pin locking system and novel vibration manifold mounting, allowing contractors to change paving widths in a matter of hours.
Single-point main-frame telescoping from one side of the tractor is said to halve the potential flex points and prevents deflection. Hydraulically controlled main frame extenders allow the extension to telescope and retract quickly to minimise width change time. Offering up to a 2.4m extension, the two-track SF3502C paver offers standard paving widths ranging from 3.7-7.9m and a maximum 10.4m width.
With its novel design, the Terex Series 6 paving kit is claimed to be 55% stronger than earlier Terex designs, while it has a finishing zone of 1524mm to improve surface smoothness. Vibrator manifolds mount directly to the paving kit with quick disconnects, reducing vibrator hose length. With only eight hose connections between the kit and tractor at a 7.3m paving width, this reduces the time needed for width changes.
The low-rise engine compartment improves the field of vision to the slab behind the paver, while see-through walkways give a better view of the head of material in front of the paving pan. For optimum flotation, traction and stability, the SF3502C has 3.7m long by 406mm wide triple-grouser street shoes. A dual-range propel system offers a variable hydrostatic paving speed range up to 10.7m/min and a travel range up to 25.3m/min.
With road construction investment being seen around the world, concrete slipformer manufacturers are seeing strong export sales at present. New models are coming to market also with manufacturers continuing to broaden ranges by offering additional features and capabilities.
US concrete paving specialist
The company is also offering additions to its model range, such as an update to its well-proven and highly versatile 9500 material handling machine. This unit can be used as a trimmer, concrete and asphalt placer, and a shoulder trimmer. It is now available with an optional hydraulically-folding rear conveyor belt for improved transportability. The new option allows the conveyor to remain attached to the 9500 for transport and when folded up the machine is just 12.7m long by 3.5m high.
This option was developed following a specific request from a contractor. And as part of the redesign process, GOMACO engineers rebuilt the 9500’s conveyor to be stronger and more rigid with a truss-style framework. The switch controlling the hydraulically-folding rear conveyor can be placed at different locations on the back of the machine, which improves visibility and safety. The belt width is the same as the standard unit at 914mm while the rear conveyor maintains its 160° swing with hydraulic height adjustment up to 3.7m. It has a 10.6m long reach during machine operation, with a conveyor belt speed of 153.6m/minute, which allows fast placing of concrete or removal of trimmed material.
The two-track 9500 is equipped with a front-mounted trimmerhead that also offers several benefits to users. This allows trimming to the end of each pass or close to front obstacles. The powerful single-drive, hydrostatic motor offers high production as well as fewer connections and parts. Time savings are also claimed for the 9500’s quick-detach design of the trimmerhead, which has machine-mounted pick-up arms and can be quickly and easily loaded on the truck for transport.
The 9500 has a trimmer load control that controls the travel speed and ensures optimum power at the trimmerhead. By controlling travel speed a contractor can ensure accurate trimming and in addition, the 9500 was designed to offer job-site mobility and manoeuvrability. The machine can make a 360° turn within its own length and is also said to be user-friendly and safe to operate, providing good all-round visibility of the site. Other features include a remote control handset, emergency stop buttons located on strategic areas of the machine, a back-up alarm, an alarm for conveyor swing, and a rotating beacon on the rear conveyor.
At the same time, GOMACO’s rear-loading, front inserting 5400 series bar inserter is now available on the 3100 and 5000 series molds with a self-supported transition adjustor. Previously, the 5400 bar inserter was only available with the 5400 series mold. The inserter mounts to a T-bar, which is bolted onto the front of the 3100 or 5000 series mold, while the bar loading chain system is supported by a stand in the rear of the mold. It can be retrofitted to any existing 3100 or 5000 series mold in the field with a self-supported transition adjustor.
The GOMACO?5400 series bar inserter loads from the safety of the work bridge on the back of the paver. The system inserts the bar in front of the mold and has a chain feed system that allows the bars to travel in a flat, horizontal path, offering a high degree of reliability and efficiency. With the inserter mounted to the mold, on-the-go crown changes can be made while still maintaining constant bar depth. Individual guides on the right and left side of the inserter keep each bar parallel to the top of the slab while smart cylinders control depth of placement. The GOMACO exclusive G+ control system is used to control the bar insertion process and timing and the monitor features a magnetic mount that allows it be placed anywhere on the side of the paver for visibility of the working area.
The system can place bars from10-25mm in diameter and between 508-1016mm in length. A box for the bar bundles is mounted to the back of the paver allowing easy loading of the bundles and also easy access to load the bars into the bar magazine. One crew member can work from the paver’s work bridge loading the bar magazine on one or several 5400 series bar inserters.
Another firm benefiting from worldwide sales is
The company has done well from overseas working and Algeria’s East-West Highway project was a deal for the firm. Bullock said, “We had dozens of machines on that highway. For every km of road there was 4km of barrier.”
He explained that the highway features two centerline barriers plus barriers on the outside as well, to prevent herds of goats or cattle as well as any wild animals from straying across the highway. This is just one of several projects in North Africa where the firm has supplied machines, with another 5700C slipformer being used to build centerline barrier for the upgrade to the Cairo-Alexandria highway in Egypt for instance.
With the firm’s home market having been weak, exports have been crucial and Bullock said, “In mid-2010 we shifted everything to our international business.”
Certain countries have been particularly good for concrete slipformer suppliers in particular and Bullock said, “Ecuador was one of those markets. The government said it wanted to go concrete.” He added that sister firm Power Pavers sold nine machines to Ecuador on that basis.
Meanwhile Asia has been a good export market for Power Curbers and sister firm Power Pavers. Vietnam has been particularly healthy although Bullock added that other Asian countries are also seeing increased paver sales and have further potential, “The Philippines made a shift to concrete a year ago.”
While Power Curbers is active in China, this market is still comparatively small. He said, “We’ve not seen a shift to concrete at this point. We’ve sold some 5700s but for kerb and gutter work.”
And the company does not consider the risk of Chinese copies to be a serious threat. Concrete paving is a niche market with comparatively low volumes that is unlikely to prove interesting commercially to Chinese manufacturers interested in selling volume products.
But the shift away from the US has required all the players in the sector to change focus. When the US market is good it accounts for around 50% of slipforming business according to Bullock. But business is good in the barrier sector though and he added, “There’s so much barrier work nationwide. We’ve sold so many machines for barrier jobs as opposed to kerbing.”
The company is also now offering stringless technology with its machines and Bullock said, “We have delivered a machine with stringless technology and it’s off to a great start.”
This first machine is being used by a contractor in Florida and is equipped with a control system from
The machines from sister company
Bullock added the sales potential for stringless controls is greater with the Power Pavers machines than those from Power Curbers. “Paving is straighter than kerb and gutter, which has more curves so has more complex algorithms.”
He continued, “We did have good results with the Leica (Geosystems) control. It was right on the money and we were a little surprised at how good it was. The steering was fine, even though that’s the biggest challenge.”
But Bullock said that the tests with the Topcon package have proven equally successful and added that the firm is offering both as options and leave the choice to the client.
The firm’s most recent range addition has been the C-Max, a further development of its 5700 slipformer. This extends the capabilities of the base machine and Bullock said, “The C-Max exceeded what we thought it’d do.”
Enquiry levels are good for this unit for export, while two C-Max units have been sold in the US.
Meanwhile the 1700 model from Power Pavers was introduced last year and demand has been healthy from developing countries for this unit, which can pave 3.65m wide. Compact slipformers have advantages particularly for use in developing countries and Bullock said, “A small machine works well from a traffic point of view and is also better from a concrete supply perspective.”
The Power Pavers models offer greater sophistication than before and Bullock said, “We still have hydraulic controls as the base option but we also have digital controls and 3D systems to do more complex jobs.”
From
Single-point main-frame telescoping from one side of the tractor is said to halve the potential flex points and prevents deflection. Hydraulically controlled main frame extenders allow the extension to telescope and retract quickly to minimise width change time. Offering up to a 2.4m extension, the two-track SF3502C paver offers standard paving widths ranging from 3.7-7.9m and a maximum 10.4m width.
With its novel design, the Terex Series 6 paving kit is claimed to be 55% stronger than earlier Terex designs, while it has a finishing zone of 1524mm to improve surface smoothness. Vibrator manifolds mount directly to the paving kit with quick disconnects, reducing vibrator hose length. With only eight hose connections between the kit and tractor at a 7.3m paving width, this reduces the time needed for width changes.
The low-rise engine compartment improves the field of vision to the slab behind the paver, while see-through walkways give a better view of the head of material in front of the paving pan. For optimum flotation, traction and stability, the SF3502C has 3.7m long by 406mm wide triple-grouser street shoes. A dual-range propel system offers a variable hydrostatic paving speed range up to 10.7m/min and a travel range up to 25.3m/min.