Developments in data processing and management are revolutionising the way concrete strengths can be measured and used to improve efficiencies - Kristina Smith reports on two new technologies
A new system that uses thermal imaging to measure the strength of sprayed concrete tunnel linings is being trialled for the first time in London. The brainchild of Dr Benoit Jones, managing director of Inbye Engineering, the technique could lead to improvements in safety, quality and – in the longer run – productivi
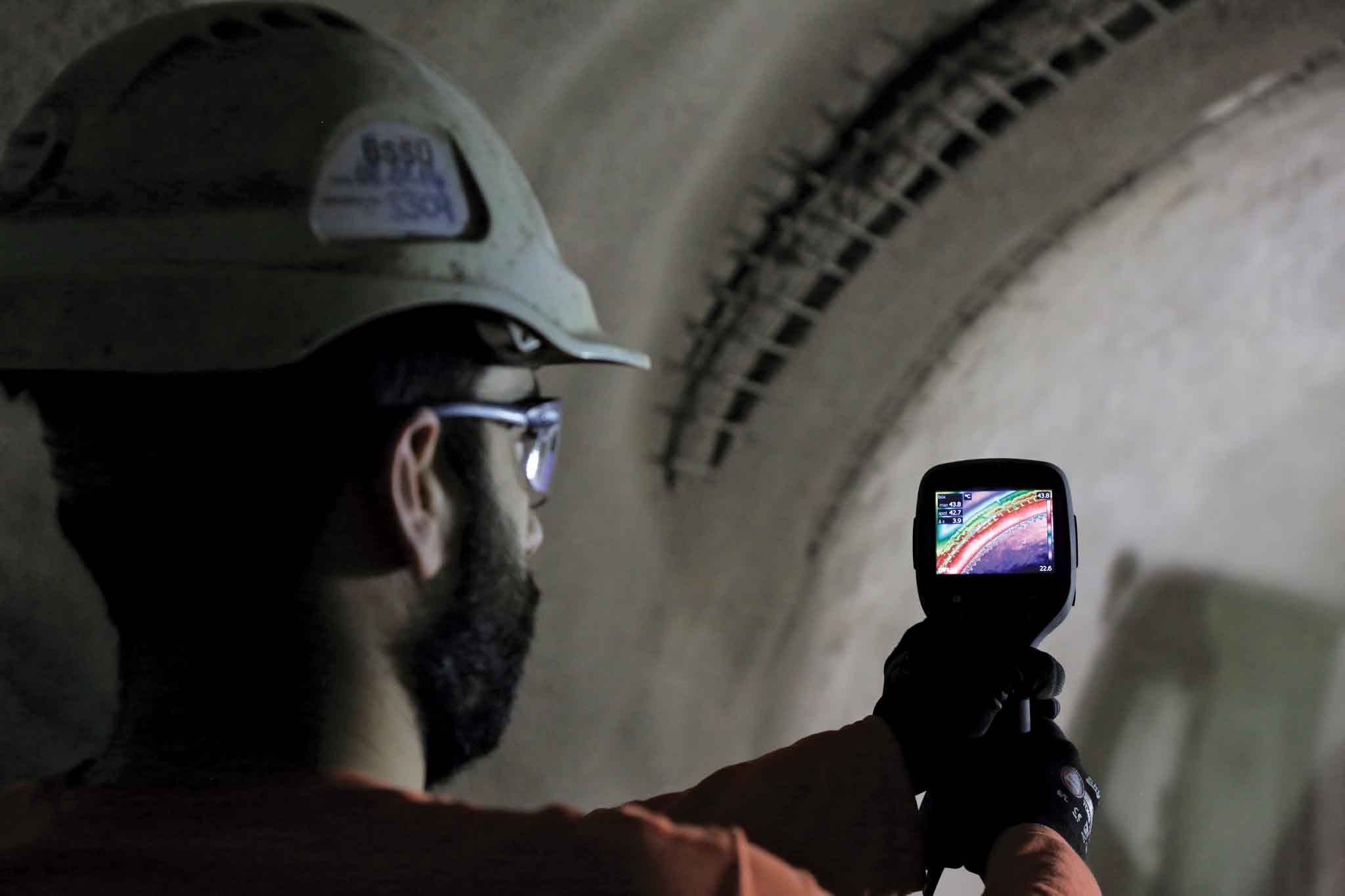
The innovative system from Inbye Engineering is proving its worth on major infrastructure projects
RSSDevelopments in data processing and management are revolutionising the way concrete strengths can be measured and used to improve efficiencies - Kristina Smith reports on two new technologies
A new system that uses thermal imaging to measure the strength of sprayed concrete tunnel linings is being trialled for the first time in London. The brainchild of Dr Benoit Jones, managing director of8537 Inbye Engineering, the technique could lead to improvements in safety, quality and – in the longer run – productivity.
“This technique gives us a better idea of what the whole lining is doing rather than extrapolation from a panel of a small area of lining,” says Jones. Current test methods for the strength of sprayed concrete lining include using penetrometers or Hilti guns, taking samples and using test panels sprayed at the same time
One of the most common causes of serious accidents including fatalities during sprayed concrete lining application occurs when ‘green’ or insufficiently cured concrete falls off the roofs of tunnels. Patches of less cured concrete can occur for a number of reasons, such as an absence of accelerator being added as the concrete is sprayed through the nozzle of the spraying machine.
Jones has been working on his invention, which he has named Strength Monitoring Using Thermal Imaging (SMUTI) since 2011, when he was based at Warwickshire University. Since then there have been a number of phases which have seen research carried out both in the laboratory and on sites.
SMUTI involves using a thermal imaging camera, placed at a safe distance, to measure the temperature of the concrete at various time intervals. Software then transforms the temperature measurements into compressive strength values.
The initial two development phases, which saw researchers taking readings on Crossrail’s Bond Street Station where Bam2717 Ferrovial Kier (BFK) was working and Whitechapel Station with 1146 Balfour Beatty BeMo Tunnelling 2567 Morgan Sindall Vinci (BBMV), demonstrated that SMUTI was feasible. The latest trial, which began in March this year on the Bond Street Station Upgrade for London Underground, involves the shift engineers from JV contractor Costain Laing O’Rourke using the technology.
“The theory is fairly simple in some ways,” said Jones. “But the practicalities are a challenge. We want something that is easy to use, foolproof, so that as many people as possible can use it and see the benefits.”
This trial will see results from SMUTI compared to those from traditional methods, although this in itself presents a challenge, says Jones: “The biggest problem is that the only test we can compare the results to is using the penetrometer needle which we don’t think is really reliable itself. So we are trying to improve our method against something we don’t have total confidence in.”
For strengths above 1MPa, Jones and his researchers are confident that SMUTI gives reliable results; it is in strengths below that, which occur in the first few days, where fine tuning is necessary. If all goes to plan, the team hope to have some firm answers by September.
Jones, who has set up a dedicated company, Inbye Engineering, to patent SMUTI and help fund its development, would like to see the technique used on tunnelling projects around the world. Though he has not investigated its use on concrete pavements, he concurs that there could be some potential use for thermal imaging there too.
203 Doka continues to develop its Concremote system for measuring concrete strength remotely. The latest addition to the technology, which measures the temperature of curing concrete and converts that to a predicted strength, is the Concremote plug.IN which sees positions for wireless sensors built into its Dokadek 30 decking formwork panels.
Being able to measure concrete strengths more accurately can allow contractors to strike forms earlier, cutting programme times and potentially saving money. This type of technology also allows contractors to provide long-term quality monitoring of a project, said Doka’s director of research and development Johann Peneder.
“With this system we can do much more than measure strengths. It’s about the sustainability of a project, what the concrete will be like in 20 or 30 years’ time. It’s important for the contractor to be able to ensure what quality he can expect. By pressing a button he can get all that information.”
As well as the plug.IN sensors installed through the ports in the decking formwork, Concremote uses wireless slab sensors which are inserted into the top of fresh concrete once screeded and cable sensors which are installed in the form-ply of the wall formwork. The sensors transmit readings to the Concremote data centre which computes strength development data which can be accessed through a secure web portal via notebook, tablet or smartphone. Concremote can also be set up to send information via text or email message.
In addition to providing real-time data related to curing and stripping times, the information can be used to calculate when pre-stressing can be carried out. Measuring variations in temperature is also important for monitoring stresses that may develop in a component, helping to avoid cracks and future structural damage.
Concretemote is now being used in 20 to 25 projects around the world. The extent to which it can be exploited varies between different regions, depending on what that country’s regulations allow, says Peneder.
In the future, Peneder predicts that he information collected through Concremote will be incorporated into BIM (building information models) to help inform owners’ future maintenance strategies. “We want to further extend this technology in the future. We are just at the start of what is possible now,” says Peneder.
New protocol tests corrosion protection
Corrosion control technology specialist Cortec has put three of its concrete repair products through a new testing protocol which aims to ensure their performance, and claims it is one of the first manufacturers to do so. The products which underwent testing by Tourney Consulting Group (TCG) were Cortec Migrating Corrosion Inhibitors (MCI): MCI-2018, MCI- 2019 and MCI-2020.
Published in July 2014, the new M-82 Standard Protocol to Evaluate the Performance of Corrosion Mitigation Technologies in3416 Concrete Repairs comes from the 2406 US Bureau of Reclamation. Following industry consultation and discussion, the Bureau employed TCG to develop the protocol through a pilot program. The aims of the protocol are to predict the effectiveness of mitigation techniques for corrosion of steel reinforcement in existing structures caused by chloride ingress.
The protocol sets down a minimum level of chloride content at which the tests must be done, with Cortec’s tests carried out at a higher level to demonstrate their effectiveness. According to the manufacturer, the MCI treatments showed a reduction in cracking in both length and area compared to the control slabs and were deemed effective in mitigating ongoing corrosion.
MCI-18 is a combination water repellent and Migrating Corrosion Inhibitor (MCI) whose added protection comes in the form of a 100% organosilane water repellent. MCI-2019 is similar to MCI-2018 but contains only 40% organosilane in a solvent base, offering a more cost-effective solution. MCI-2020 is a water-based corrosion inhibitor for concrete and masonry structures. Since MCI-2020 does not have water repelling properties, a standard 40% silane repellent was used over it during the M-82 protocol testing.
CONTROLS’ new console updates old test machines
2139 CONTROLS GROUP has launched a new control console, the AUTOMAX UTM, for testing both concrete and steel. In consultation with universities and laboratories around the world, CONTROLS has developed the console to run several different test procedures, including compression, flexure and indirect tensile tests on various construction materials; Elastic Modulus and Poisson Ration determination for concrete and cement specimens; and tensile tests on steel reinforcing bars.
“Even though most of the machines used in laboratories all over the world are manually controlled, automatic control achieves an accurate and constant testing speed without large fluctuations,” says Federica Bini, product manager at CONTROLS GROUP. “This not only guarantees compliance with the requirements of a standard, but also provides reliable and consistent results, not affected by the way different operators' carry out the test.”
The console can be used to update an existing tension, compression or combined tension and compression testing machine by replacing existing hydraulics and electronics. This allows a dated unit to be upgraded to meet the evolving requirements of international standards with a limited investment, says CONTROLS.
The AUTOMAX UTM is PC-controlled and comes with different software modules specifically designed to meet the testing procedures of the main international standards related to the above tests. The machine is able to connect and control up to four testing frames and to acquire data from up to 10 displacement, strain and elongation sensors.
The test cycle, with closed loop digital feedback, for any kind of test selected, is automatically performed by simply pressing the start button. Test graphs and actual test rates are displayed in real time during the test. Customised test certificates can be directly printed or archived at the end of the test, in order to prove that tests have been executed in accordance with the relevant standard.
RSS
A new system that uses thermal imaging to measure the strength of sprayed concrete tunnel linings is being trialled for the first time in London. The brainchild of Dr Benoit Jones, managing director of
“This technique gives us a better idea of what the whole lining is doing rather than extrapolation from a panel of a small area of lining,” says Jones. Current test methods for the strength of sprayed concrete lining include using penetrometers or Hilti guns, taking samples and using test panels sprayed at the same time
One of the most common causes of serious accidents including fatalities during sprayed concrete lining application occurs when ‘green’ or insufficiently cured concrete falls off the roofs of tunnels. Patches of less cured concrete can occur for a number of reasons, such as an absence of accelerator being added as the concrete is sprayed through the nozzle of the spraying machine.
Jones has been working on his invention, which he has named Strength Monitoring Using Thermal Imaging (SMUTI) since 2011, when he was based at Warwickshire University. Since then there have been a number of phases which have seen research carried out both in the laboratory and on sites.
SMUTI involves using a thermal imaging camera, placed at a safe distance, to measure the temperature of the concrete at various time intervals. Software then transforms the temperature measurements into compressive strength values.
The initial two development phases, which saw researchers taking readings on Crossrail’s Bond Street Station where Bam
“The theory is fairly simple in some ways,” said Jones. “But the practicalities are a challenge. We want something that is easy to use, foolproof, so that as many people as possible can use it and see the benefits.”
This trial will see results from SMUTI compared to those from traditional methods, although this in itself presents a challenge, says Jones: “The biggest problem is that the only test we can compare the results to is using the penetrometer needle which we don’t think is really reliable itself. So we are trying to improve our method against something we don’t have total confidence in.”
For strengths above 1MPa, Jones and his researchers are confident that SMUTI gives reliable results; it is in strengths below that, which occur in the first few days, where fine tuning is necessary. If all goes to plan, the team hope to have some firm answers by September.
Jones, who has set up a dedicated company, Inbye Engineering, to patent SMUTI and help fund its development, would like to see the technique used on tunnelling projects around the world. Though he has not investigated its use on concrete pavements, he concurs that there could be some potential use for thermal imaging there too.
Being able to measure concrete strengths more accurately can allow contractors to strike forms earlier, cutting programme times and potentially saving money. This type of technology also allows contractors to provide long-term quality monitoring of a project, said Doka’s director of research and development Johann Peneder.
“With this system we can do much more than measure strengths. It’s about the sustainability of a project, what the concrete will be like in 20 or 30 years’ time. It’s important for the contractor to be able to ensure what quality he can expect. By pressing a button he can get all that information.”
As well as the plug.IN sensors installed through the ports in the decking formwork, Concremote uses wireless slab sensors which are inserted into the top of fresh concrete once screeded and cable sensors which are installed in the form-ply of the wall formwork. The sensors transmit readings to the Concremote data centre which computes strength development data which can be accessed through a secure web portal via notebook, tablet or smartphone. Concremote can also be set up to send information via text or email message.
In addition to providing real-time data related to curing and stripping times, the information can be used to calculate when pre-stressing can be carried out. Measuring variations in temperature is also important for monitoring stresses that may develop in a component, helping to avoid cracks and future structural damage.
Concretemote is now being used in 20 to 25 projects around the world. The extent to which it can be exploited varies between different regions, depending on what that country’s regulations allow, says Peneder.
In the future, Peneder predicts that he information collected through Concremote will be incorporated into BIM (building information models) to help inform owners’ future maintenance strategies. “We want to further extend this technology in the future. We are just at the start of what is possible now,” says Peneder.
New protocol tests corrosion protection
Corrosion control technology specialist Cortec has put three of its concrete repair products through a new testing protocol which aims to ensure their performance, and claims it is one of the first manufacturers to do so. The products which underwent testing by Tourney Consulting Group (TCG) were Cortec Migrating Corrosion Inhibitors (MCI): MCI-2018, MCI- 2019 and MCI-2020.
Published in July 2014, the new M-82 Standard Protocol to Evaluate the Performance of Corrosion Mitigation Technologies in
The protocol sets down a minimum level of chloride content at which the tests must be done, with Cortec’s tests carried out at a higher level to demonstrate their effectiveness. According to the manufacturer, the MCI treatments showed a reduction in cracking in both length and area compared to the control slabs and were deemed effective in mitigating ongoing corrosion.
MCI-18 is a combination water repellent and Migrating Corrosion Inhibitor (MCI) whose added protection comes in the form of a 100% organosilane water repellent. MCI-2019 is similar to MCI-2018 but contains only 40% organosilane in a solvent base, offering a more cost-effective solution. MCI-2020 is a water-based corrosion inhibitor for concrete and masonry structures. Since MCI-2020 does not have water repelling properties, a standard 40% silane repellent was used over it during the M-82 protocol testing.
CONTROLS’ new console updates old test machines
“Even though most of the machines used in laboratories all over the world are manually controlled, automatic control achieves an accurate and constant testing speed without large fluctuations,” says Federica Bini, product manager at CONTROLS GROUP. “This not only guarantees compliance with the requirements of a standard, but also provides reliable and consistent results, not affected by the way different operators' carry out the test.”
The console can be used to update an existing tension, compression or combined tension and compression testing machine by replacing existing hydraulics and electronics. This allows a dated unit to be upgraded to meet the evolving requirements of international standards with a limited investment, says CONTROLS.
The AUTOMAX UTM is PC-controlled and comes with different software modules specifically designed to meet the testing procedures of the main international standards related to the above tests. The machine is able to connect and control up to four testing frames and to acquire data from up to 10 displacement, strain and elongation sensors.
The test cycle, with closed loop digital feedback, for any kind of test selected, is automatically performed by simply pressing the start button. Test graphs and actual test rates are displayed in real time during the test. Customised test certificates can be directly printed or archived at the end of the test, in order to prove that tests have been executed in accordance with the relevant standard.
RSS