In Tucson, Arizona, contractor McNeil brothers is using a two-track GOMACO concrete slipformer on a 3.2km stretch of highway. This project is for the Arizona Department of Transportation (ADOT) and involves widening Interstate 10 to four lanes of traffic in each direction between Ruthrauff Road and Prince Road in Tucson. This new stretch was needed to better handle increasing traffic demands in the city and includes rebuilt entrance and exit ramps to improve access to the city.
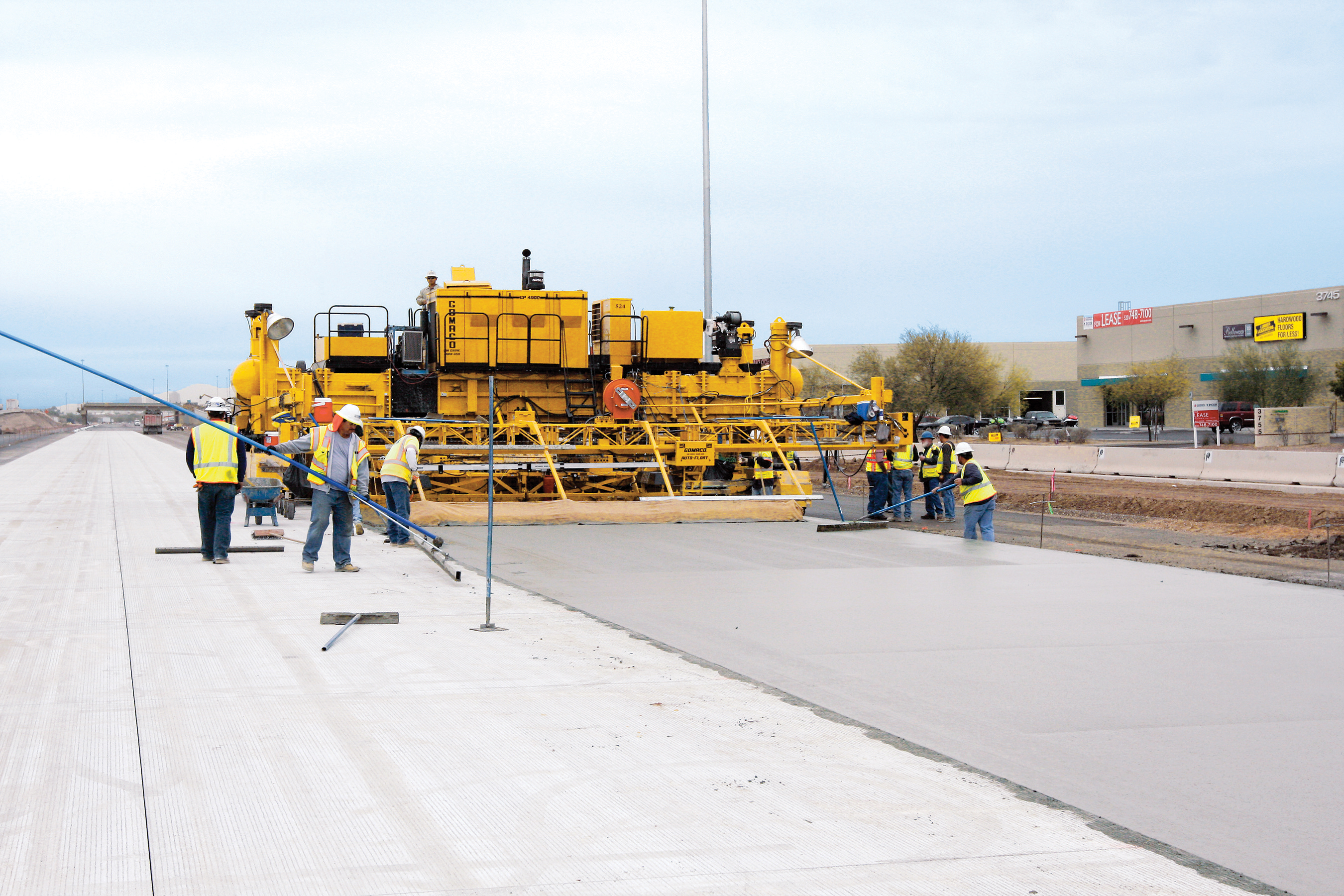
GOMACO’s GSI system is said to optimise smoothness for the contractor as it provides fast feedback on finish quality
In Tucson, Arizona, contractor McNeil brothers is using a two-track Gomaco concrete slipformer on a 3.2km stretch of highway. This project is for the Arizona Department of Transportation (ADOT) and involves widening Interstate 10 to four lanes of traffic in each direction between Ruthrauff Road and Prince Road in Tucson. This new stretch was needed to better handle increasing traffic demands in the city and includes rebuilt entrance and exit ramps to improve access to the city.
McNeil Brothers purchased a new218 Gomaco two-track GP-4000 paver with a 5400 series mold and IDBI for the 2013 paving season, also equipping the machine with two paver-mounted Gomaco Smoothness Indicator (GSI) units.
Matt McNeil, vice president of McNeil Brothers, explained that the job involves paving up to 25.6m at the widest point. The work includes paving the four lanes, shoulders, on/off ramps and some frontage roads. The firm has ITS mobile batch plant on site mixing the standard concrete mix with a 57 aggregate and the slump averages from 25-32mm. A fleet of 15 trucks is used to carry material from the plant, dumping the concrete directly onto the grade in front of the paver.
The GP-4000 is paving the passes 7.3M wide and 381mm thick and for this job the machine has been equipped with three different bar insertion systems, including a front-mounted centre bar inserter, two rear-mounted side bar inserters, and the IDBI that inserts the dowel bars for the transverse joint. The IDBI is inserting 22 dowel bars across the width of the slab, spaced on 305mm centres. Each bar is 457mm long and 38mm in diameter, with joints every 4.6m.
McNeil Brothers has plenty of experience with an IDBI and has been using one on a GOMACO paver since 1996, having helped GOMACO field-test the system. The firm has used various upgraded IDBI systems over the years and is now using the newest version.
This has already been field-proven on four-track pavers, but McNeil’s is the first used with a two-track GP-4000 paver and Interstate 10 is the first of many highway projects the firm intends to pave with the unit.
Another feature new to McNeil is the paver-mounted GSI unit used for monitoring the smoothness of the new road surface. ADOT uses the two-tenths blanking band to measure smoothness.
McNeil Brothers is averaging less than 25mm on the project and the ride has been good, as confirmed by the IRI according to McNeil. He added that the system gives instant feedback and allows the firm to see what is going through the paver, what effect it has on the ride and make immediate changes if required. The GSI also helps determine the optimum paving speed by providing feedback on factors such as the concrete itself, and the firm is achieving an average production of some 191m3/hour on I-10.
McNeil explained that different concrete mixes need different paving speeds and that paving faster requires wetter concrete. He said that the GSI unit makes the process easier for the contractor as it provides the necessary feedback on the paving smoothness. For final finishing, a GOMACO T/C-600 texture/cure machine follows the paver applying a burlap drag finish with longitudinal tining and white spray cure.
The contractor fully intends to use this equipment elsewhere and once this project is complete, the company will widen out its GP-4000 and IDBI to 11m to start work on another of Arizona’s highway projects.
McNeil Brothers purchased a new
Matt McNeil, vice president of McNeil Brothers, explained that the job involves paving up to 25.6m at the widest point. The work includes paving the four lanes, shoulders, on/off ramps and some frontage roads. The firm has ITS mobile batch plant on site mixing the standard concrete mix with a 57 aggregate and the slump averages from 25-32mm. A fleet of 15 trucks is used to carry material from the plant, dumping the concrete directly onto the grade in front of the paver.
The GP-4000 is paving the passes 7.3M wide and 381mm thick and for this job the machine has been equipped with three different bar insertion systems, including a front-mounted centre bar inserter, two rear-mounted side bar inserters, and the IDBI that inserts the dowel bars for the transverse joint. The IDBI is inserting 22 dowel bars across the width of the slab, spaced on 305mm centres. Each bar is 457mm long and 38mm in diameter, with joints every 4.6m.
McNeil Brothers has plenty of experience with an IDBI and has been using one on a GOMACO paver since 1996, having helped GOMACO field-test the system. The firm has used various upgraded IDBI systems over the years and is now using the newest version.
This has already been field-proven on four-track pavers, but McNeil’s is the first used with a two-track GP-4000 paver and Interstate 10 is the first of many highway projects the firm intends to pave with the unit.
Another feature new to McNeil is the paver-mounted GSI unit used for monitoring the smoothness of the new road surface. ADOT uses the two-tenths blanking band to measure smoothness.
McNeil Brothers is averaging less than 25mm on the project and the ride has been good, as confirmed by the IRI according to McNeil. He added that the system gives instant feedback and allows the firm to see what is going through the paver, what effect it has on the ride and make immediate changes if required. The GSI also helps determine the optimum paving speed by providing feedback on factors such as the concrete itself, and the firm is achieving an average production of some 191m3/hour on I-10.
McNeil explained that different concrete mixes need different paving speeds and that paving faster requires wetter concrete. He said that the GSI unit makes the process easier for the contractor as it provides the necessary feedback on the paving smoothness. For final finishing, a GOMACO T/C-600 texture/cure machine follows the paver applying a burlap drag finish with longitudinal tining and white spray cure.
The contractor fully intends to use this equipment elsewhere and once this project is complete, the company will widen out its GP-4000 and IDBI to 11m to start work on another of Arizona’s highway projects.