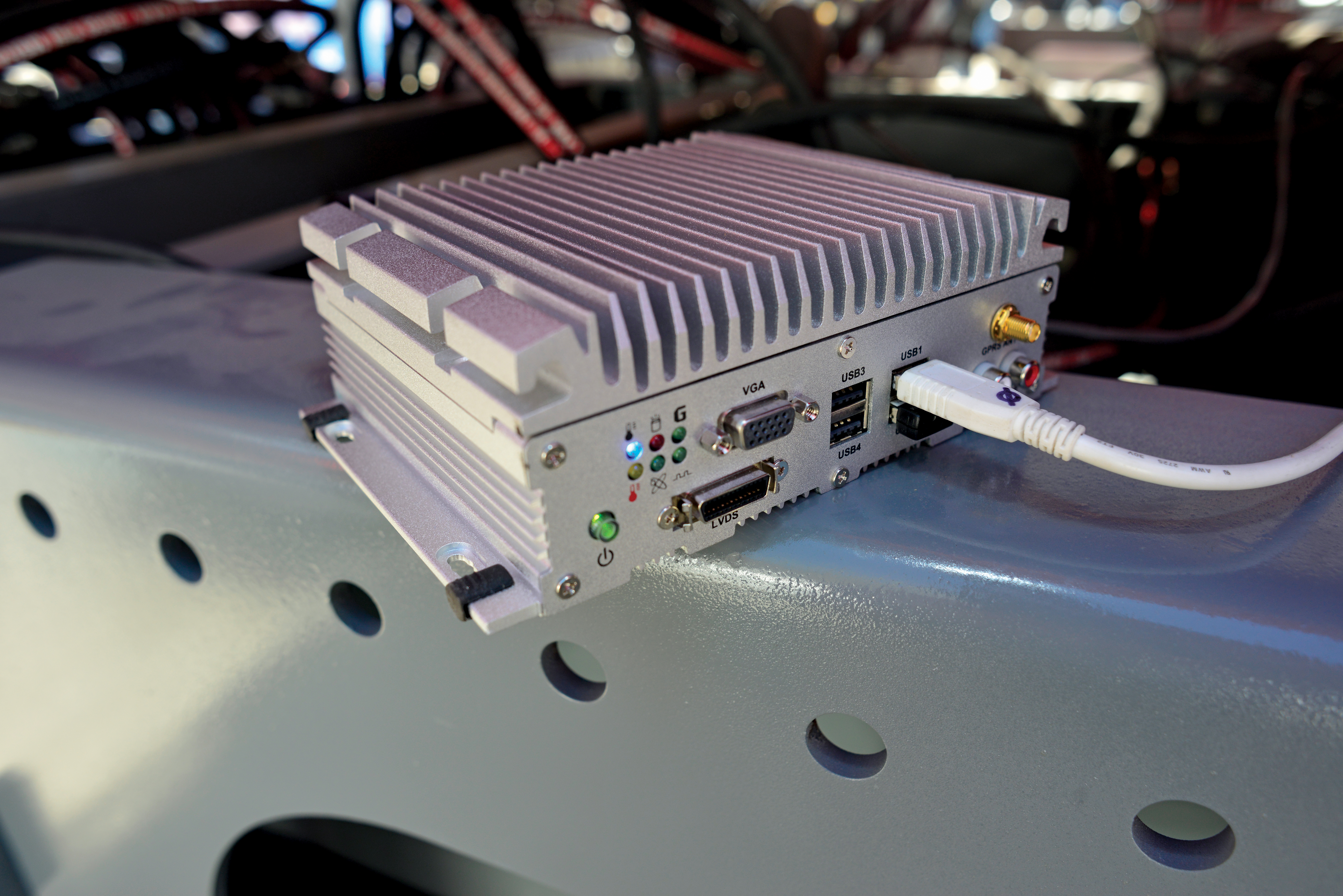
Machine innovations and machine control advances are the latest news in the concrete paving sector - Mike Woof reports
While machine control systems were pioneered in the concrete paving market, continuous refinement of the technologies is offering major improvements for customers. Customers have a choice now of more than one supplier while the packages are said to be more user-friendly than before. And in addition, the systems themselves can be more closely integrated into the machines due to advances made by the equipment manufacturers.Guntert & Zimmerman is focussing its activity on its equipment guidance and operation network (EGON) telematics system, which the firm claims offers more capabilities than simple engine monitoring and fault code reading. The EGON package is able to aggregate signals and information throughout the entire hydraulic and electrical system, allowing the firm or the contractor to see exactly where the problem is located almost in real-time (just accounting for the lag in internet connection). The firm’s marketing manager, David Lipari, explained that the EGON system can monitor key functions such as the steer sensors and position switches. This package provides a comprehensive analysis of machine functions using sophisticated telematics capabilities. Lipari said, “No matter where you’re paving it’ll work as long as you have a wi-fi or GSM connection.”
The system provides alerts if there are issues with various functions as it monitors the paver’s CANbus system. “You can use it to pinpoint performance errors with the machine. This will give our customers peace of mind and we’re actually able to see what’s happening in real-time. You can use it to watch a live profilagraph on the machine, although at the moment EGON is more of a service tool.”
Highly advanced, this control system is said to incorporate user-friendly features and state of the art network controllers. The EGON system will make maintenance and servicing easier as it offers extensive diagnostic capabilities. According to the company, this package also helps to maximise available paving time. The position of the unit on the machine has still to be finalised however.
Telematics capabilities allow the scheduling of trucks to ensure a continuous and consistent material flow to the paver, with alerts over any potential delays due to traffic hold-ups for example. The system can also be used to monitor the heat and grade of the concrete as it arrives at the machine, with any necessary changes required being fed back to the concrete plant immediately. An open architecture in the concrete pavers allows use of all the machine control functions. Lipari said, “The hardware for the EGON system is minimal; now it’s a matter of capturing the data.”
Further capabilities are in development and the firm will be announcing these towards the end of 2013. The EGON system has been fitted to the firm’s S600 model as well as the new S850 launched earlier this year, but is also available on all the other pavers in the line-up. The S850 has a patented, double telescopic tractor frame, with an access walkway, and allows a working range of 3.66-7.92m, with up to 2.13m of telescoping ability for each side. Customers can also fit the optional bolt-in tractor frame extensions allowing paving widths of up to 12m, while the S850SL can be fitted with the firm’s well-proven TeleEnd system.
North Carolina-based
This versatility is a focus for the machines built by Power Curbers and also for those units from sister firm Power Pavers. Dyke Messinger, president and CEO of Power Curbers said, “The customer today wants a machine that can do multiple applications, not just kerb or not just barrier. They want a machine that can pave. Our multi-purpose machine can pave up to 4m wide and it can do barrier up to 2m high.”
According to Messinger this versatility and adaptability ensures that a machine achieves greater utilisation and providing a better return on investment for the owner, with a faster payback time.
But machine control technologies are also important to Power Curbers and Power Pavers and the machines can now work with the latest 3D paving controls. Power Curbers introduced the
German manufacturer
The SP 81/SP 81i can produce drains, concrete barriers, kerbs or narrow paths up to 2.2m high and 3m wide. The offset mould can be mounted on either side, allowing the concrete paver to be easily adapted to a job site and even where space is tight. The trimmer unit can be fitted as required to provide additional accuracy. Spiral-shaped, the trimmer drum is fitted with cutters and removes uneven sections, helping deliver a more uniform profile.
The SP 82 and SP 82i are designed with two rigid tracks while the SP 84 and SP 84i feature four steerable, swivelling crawler tracks. These machines can be used to slipform concrete pavement with the mould integrated between the crawler tracks, paving roadways and surfaces from 2-8m wide as standard and with a paving thickness of up to 400mm. Thicker pavements can also be achieved if required and the pavers can be used to construct surfaces with a double cross fall of up to 3%.
As with the existing compact SP 15 and SP 25 models, this new SP 80 series is also available with the firm’s WI-Control package, highlighting that machine control technologies are a focus for Wirtgen as with its rivals.
The sophisticated machine control system can automatically recognise machine configuration and set optimum parameters accordingly and can also be connected with the customer’s own fleet management system through a standard interface. Another new package from Wirtgen is the company’s sophisticated WITOS system, which offers modular telematics monitoring for fleet management purposes.
Functions include monitoring a fleet of machines and managing service and diagnostic processes and the process optimisation section has modules for paving (as well as milling and compaction).
Under stress
A new handbook has been developed under a co-operative agreement between the Federal Highway Administration (FHWA) and the Precast/Prestressed Concrete Institute (PCI). This new report is on precast concrete pavements and has been prepared by the PCI's Pavement Committee. It is intended to give the latest information on precast pavements for highway construction. "Precast concrete pavement is a long-life solution for pavement rehabilitation and reconstruction - if produced and constructed according to recommended guidelines," said David Merritt, PCI Pavement Committee chair and project manager at pavement engineering firm The
Precast pavement's long life is due partially to the method used to produce the concrete. The precast panels are fabricated and cured in a controlled environment before being transferred to a job site. For an even more durable pavement, precast panels can be prestressed, a process that minimises stresses in the pavement that can lead to cracking. The report is divided into four areas: applications, design and maintenance, manufacture, and construction. Any section may be individually obtained as a stand-alone document.
In addition to the comprehensive handbook, PCI has created an online precast pavement repository at www.PrecastConcretePavement.org to provide access to further information and project resources. The site was developed as part of PCI's cooperative agreement with FHWA.