Innovative developments are pushing forward concrete road construction techniques. The concrete road sector looks to benefit from some key innovations and developments now coming to market or being employed in different territories. Irregular weather and environmental conditions can alter the rate at which concrete cures, with a risk of plastic shrinkage cracks that can compromise the integrity of a pavement. Contractors cannot control the environmental conditions of a paving project and when weather patter
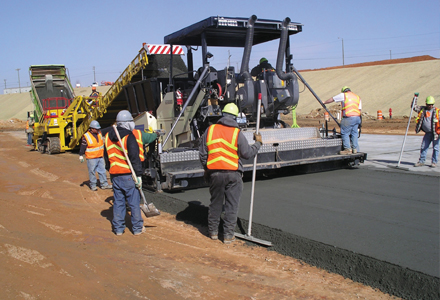
RSS
However, pavement engineers at Transtec are developing a wireless concrete curing monitor called SmartCure. The device tells pavement contractors when to adjust curing settings in response to weather changes, as well as changes in the concrete itself.
The system is an integrated portable weather station and software tool that measures current climatic conditions and computes the evaporation rate of moisture from the concrete surface. A weather unit is attached to the curing cart along with an infrared sensor for monitoring concrete surface temperatures and a GPS for location tracking.
Data is transferred wirelessly to an on-site laptop while the pavement is placed and this is fed to the SmartCure software.
The concrete paving equipment itself also continues to evolve and develop, with new models now available.218 Gomaco continues to add to its product range with the addition of the new 5400 Series paving mold. This unit features a new box design and has a durable 13mm paving skin, as well as a vertically-adjusting mounting that allows precise levelling respective to the machine. The mold is offered with the option of telescoping end sections that allow the user to add up to 305mm on each side. The standard paving depth is from 0-610mm and the system comes with edge slump adjustment and hydraulic vertical hinged sideplates. The mold has folding sideplate wings that do not need to be removed for transport, while a pivoting mold mounting beam is said to eliminate stress points.
The mold has a front and rear top T-bar that can be used to attach accessories such as the new vibrator mounting tube and this novel T-bar design also boosts structural rigidity. The inserts are bolted together with front and rear alignment pins, which is said to make assembly easier. The innovative modular design uses a wedge lock system that is said to make changing widths easier and the system comes with 254mm of hydraulic height adjustment, as well as offering hydraulic crown adjustment. The spreader plow is mounted to paver frame T-rail and the firm offers options such as an auger and a tamper bar. To further boost versatility this mold system can be equipped with GOMACO's novel 5400 Series bar inserter.
RCC evolution Established techniques are benefiting from further refinements and look set to be used more widely as a result. A continuous mixing plant from316 Rapid International was recently used in the mixing of roller compacted concrete (RCC) for a road surface on Highway 78 in Aiken, South Carolina, USA. As the current road surface had deteriorated to the point where a thin resurface treatment was not viable, the repair method consisted of milling the old surface and replacing it with 254mm of RCC. Interestingly, the Department of Transport also chose to diamond grind the RCC surface.
This method was chosen based on minimising traffic disruption, long-term durability, and cost of construction. For the past three decades, RCC pavements have been used in the US where strength, speed of construction, and economy are vital and is used in parking areas, intersections, highway shoulders and low speed roads for example. However, this development opens the way for the use of unsurfaced RCC for high speed roads as well.
The project consisted of a four lane, 1.6km long route of failed asphalt pavement that required rehabilitation or replacement. The road has a speed limit of 72km/h and carries 6,000 vehicles/day on average. A key need was to minimise traffic disruption. Traffic control measures were implemented to maintain at least one lane in each direction open for traffic at all times.
Satterfield Construction was the general contractor for the project, while sub-contractor Morgan set up its plant close to site and tucks transported the RCC to a Gomaco RTP-500 transfer machine equipped with a 10.7m swivel conveyor. The RCC was placed using an ABG Titan 7820 paver in a single 254mm lift, using a 12tonne twin drum roller and a rubber tyred roller to compact the surface.
Following compaction, a concrete curing compound was sprayed on the RCC surface to prevent excessive moisture evaporation. After final compaction, a saw was used to cut transverse control joints spaced 6.1m apart, while the road was re-opened for traffic within 24 hours from RCC placement. To improve the surface smoothness of the RCC, diamond grinding and a milling machine were used.
Similar retexturing surface improvements are being used to renovate worn concrete roads in the UK. Developed first in California, this method has been proven in the UK by Concrete Cutters, a specialist cutting and sawing contractor. The system can cut costs as it faster, cheaper than overlaying concrete with asphalt and requires less investment in equipment. The method also results in a road surface that is quieter, while material removed from the road surface can be recycled. The first major road grinding project was completed by Concrete Cutters on four 13km lanes of the A12 with a total area of 125,000m2. The2309 Highways Agency has approved this technique, which will result in its being used on much of the 1,350km of the UK's concrete roads that need attention.
The first highway grinding trials were carried out by Concrete Cutters on a busy stretch of the A12 dual carriageway close to London as the road had become worn after 10 years of heavy use. Uneven expansion and contraction joints between the concrete slabs were giving poor ride quality and the road surface had been smoothed and degraded, boosting traffic noise and cutting skid resistance.
Concrete Cutters purchased a Tyrolit PC6000 machine to undertake trials on four, 500m lane sections. The firm was able to machine 7,500m2 of road over six nights and reopen the A12 every day, as restricting road closures to nights caused a minimum of disruption to traffic. After the initial success, four more trial sections were chosen and another 24,000m2 of highway were ground. Concrete Cutters then purchased a second machine to cope with its workload.
Evidence from the US predicts that the advantages of a reground and retextured concrete road surface can last up to 10 years, with the ability to re-machine the road 1-2 further times, with little loss of structural or load-carrying capacity.
The diamond grinding process removes irregularities from concrete roads by taking away 3-10mm from the surface. This flattens the road, evens out undulations and retextures the surface to improve skid resistance, despite the roughening process decreasing the contact area between tyre and road. With less contact area between tyre and surface, noise is reduced and traffic driving over a textured surface emits less sound energy than if the surface were smooth.
Tyrolit's PC6000 road grinder features 250 diamond saw blades with blade segments comprising synthetic diamond grains in a hard, sintered metal matrix. Grinding is achieved by the dual action of head rotation and hydraulic pressure downwards against the surface, with water flushing.
Tests on the textured concrete reveal an average increase in skid resistance of 54% compared with a smooth road surface. Other benefits include shorter road closures, the ability to retexture a lane with traffic running in adjacent lanes and the removal of the need to taper overlays at junctions.RSS
Innovative developments are pushing forward concrete road construction techniques
The concrete road sector looks to benefit from some key innovations and developments now coming to market or being employed in different territories. Irregular weather and environmental conditions can alter the rate at which concrete cures, with a risk of plastic shrinkage cracks that can compromise the integrity of a pavement. Contractors cannot control the environmental conditions of a paving project and when weather patterns result in high winds and low relative humidity, curing practices have to be adjusted.However, pavement engineers at Transtec are developing a wireless concrete curing monitor called SmartCure. The device tells pavement contractors when to adjust curing settings in response to weather changes, as well as changes in the concrete itself.
The system is an integrated portable weather station and software tool that measures current climatic conditions and computes the evaporation rate of moisture from the concrete surface. A weather unit is attached to the curing cart along with an infrared sensor for monitoring concrete surface temperatures and a GPS for location tracking.
Data is transferred wirelessly to an on-site laptop while the pavement is placed and this is fed to the SmartCure software.
The concrete paving equipment itself also continues to evolve and develop, with new models now available.
The mold has a front and rear top T-bar that can be used to attach accessories such as the new vibrator mounting tube and this novel T-bar design also boosts structural rigidity. The inserts are bolted together with front and rear alignment pins, which is said to make assembly easier. The innovative modular design uses a wedge lock system that is said to make changing widths easier and the system comes with 254mm of hydraulic height adjustment, as well as offering hydraulic crown adjustment. The spreader plow is mounted to paver frame T-rail and the firm offers options such as an auger and a tamper bar. To further boost versatility this mold system can be equipped with GOMACO's novel 5400 Series bar inserter.
RCC evolution Established techniques are benefiting from further refinements and look set to be used more widely as a result. A continuous mixing plant from
This method was chosen based on minimising traffic disruption, long-term durability, and cost of construction. For the past three decades, RCC pavements have been used in the US where strength, speed of construction, and economy are vital and is used in parking areas, intersections, highway shoulders and low speed roads for example. However, this development opens the way for the use of unsurfaced RCC for high speed roads as well.
The project consisted of a four lane, 1.6km long route of failed asphalt pavement that required rehabilitation or replacement. The road has a speed limit of 72km/h and carries 6,000 vehicles/day on average. A key need was to minimise traffic disruption. Traffic control measures were implemented to maintain at least one lane in each direction open for traffic at all times.
Satterfield Construction was the general contractor for the project, while sub-contractor Morgan set up its plant close to site and tucks transported the RCC to a Gomaco RTP-500 transfer machine equipped with a 10.7m swivel conveyor. The RCC was placed using an ABG Titan 7820 paver in a single 254mm lift, using a 12tonne twin drum roller and a rubber tyred roller to compact the surface.
Following compaction, a concrete curing compound was sprayed on the RCC surface to prevent excessive moisture evaporation. After final compaction, a saw was used to cut transverse control joints spaced 6.1m apart, while the road was re-opened for traffic within 24 hours from RCC placement. To improve the surface smoothness of the RCC, diamond grinding and a milling machine were used.
Similar retexturing surface improvements are being used to renovate worn concrete roads in the UK. Developed first in California, this method has been proven in the UK by Concrete Cutters, a specialist cutting and sawing contractor. The system can cut costs as it faster, cheaper than overlaying concrete with asphalt and requires less investment in equipment. The method also results in a road surface that is quieter, while material removed from the road surface can be recycled. The first major road grinding project was completed by Concrete Cutters on four 13km lanes of the A12 with a total area of 125,000m2. The
The first highway grinding trials were carried out by Concrete Cutters on a busy stretch of the A12 dual carriageway close to London as the road had become worn after 10 years of heavy use. Uneven expansion and contraction joints between the concrete slabs were giving poor ride quality and the road surface had been smoothed and degraded, boosting traffic noise and cutting skid resistance.
Concrete Cutters purchased a Tyrolit PC6000 machine to undertake trials on four, 500m lane sections. The firm was able to machine 7,500m2 of road over six nights and reopen the A12 every day, as restricting road closures to nights caused a minimum of disruption to traffic. After the initial success, four more trial sections were chosen and another 24,000m2 of highway were ground. Concrete Cutters then purchased a second machine to cope with its workload.
Evidence from the US predicts that the advantages of a reground and retextured concrete road surface can last up to 10 years, with the ability to re-machine the road 1-2 further times, with little loss of structural or load-carrying capacity.
The diamond grinding process removes irregularities from concrete roads by taking away 3-10mm from the surface. This flattens the road, evens out undulations and retextures the surface to improve skid resistance, despite the roughening process decreasing the contact area between tyre and road. With less contact area between tyre and surface, noise is reduced and traffic driving over a textured surface emits less sound energy than if the surface were smooth.
Tyrolit's PC6000 road grinder features 250 diamond saw blades with blade segments comprising synthetic diamond grains in a hard, sintered metal matrix. Grinding is achieved by the dual action of head rotation and hydraulic pressure downwards against the surface, with water flushing.
Tests on the textured concrete reveal an average increase in skid resistance of 54% compared with a smooth road surface. Other benefits include shorter road closures, the ability to retexture a lane with traffic running in adjacent lanes and the removal of the need to taper overlays at junctions.RSS