Demand for geosynthetics in the United States alone is projected to increase 4.4% per year through to 2010 to more than 727 million m².
Geosynthetics, used worldwide in the highway sector for strengthening, include geotextiles, geomembranes, geonets, geogrids, geosynthetic clay liners, preformed geocomposites, geocells and geofoams. The US advances will be fuelled by a recovery in nonbuilding construction.
Additionally, geosynthetics will continue to increase their use in a wider range of applications
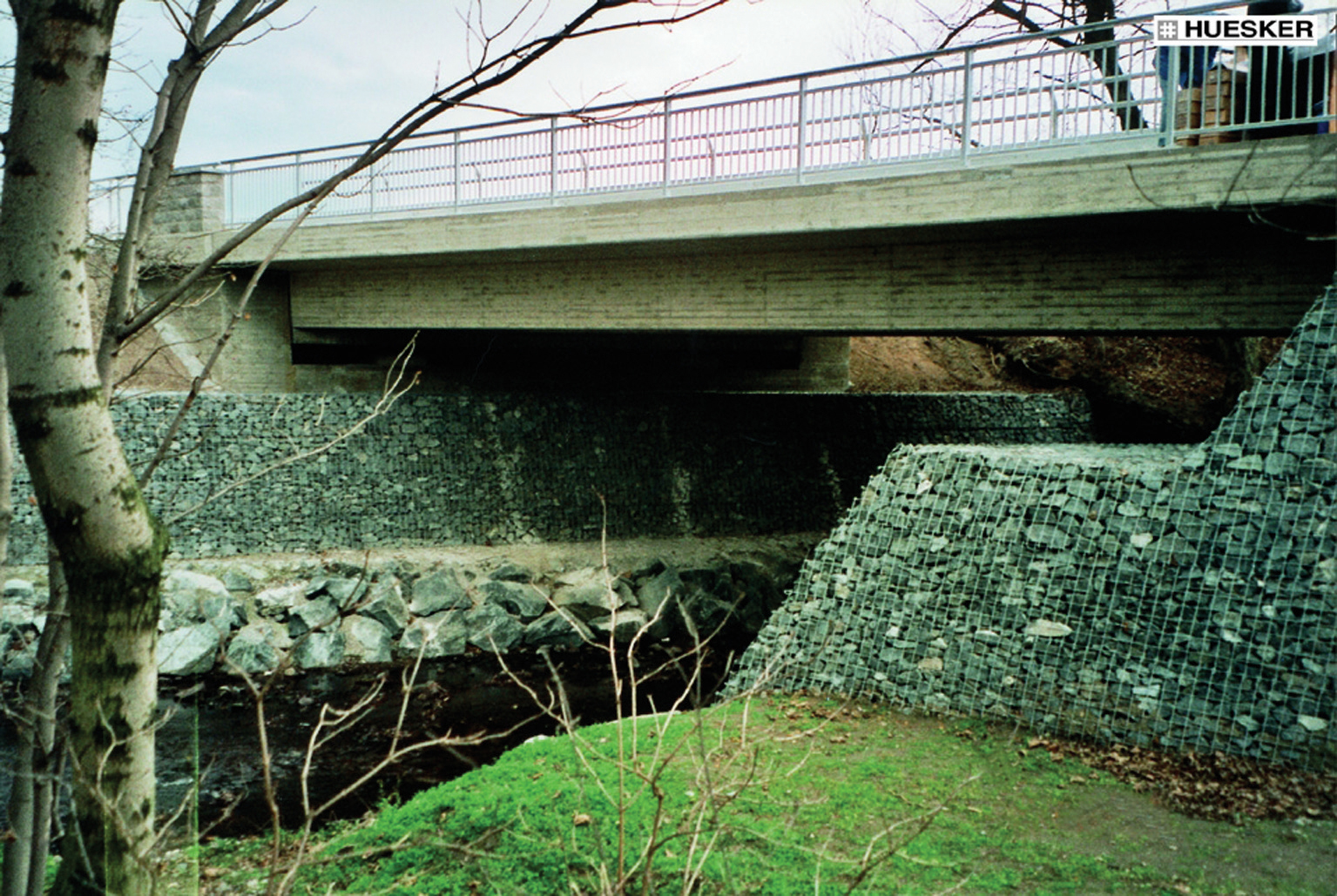
K 1355 district road bridge over the River Ilse at Ilsenburg - the first permanent geogrid-reinforced bridge abutment in Germany
Geosynthetics have a wide variety of uses and these include providing extra strength in highway construction
Demand for geosynthetics in the United States alone is projected to increase 4.4% per year through to 2010 to more than 727 million m².Geosynthetics, used worldwide in the highway sector for strengthening, include geotextiles, geomembranes, geonets, geogrids, geosynthetic clay liners, preformed geocomposites, geocells and geofoams. The US advances will be fuelled by a recovery in nonbuilding construction.
Additionally, geosynthetics will continue to increase their use in a wider range of applications, such as building construction and mining. Ongoing industry efforts to increase awareness among engineers and other specifiers of the benefits of geosynthetics in various markets will also support demand.
These and other trends are presented in Geosynthetics, a new study from The
In 2005, geotextiles accounted for the largest share of demand (in area terms), with approximately three-quarters of the total. However, in value terms, geomembranes accounted for the largest share of the market, with about half of the total. Smaller volume geosynthetic products such as geogrids, geonets and geocomposites are expected to achieve strong growth through to 2010, benefiting from the ongoing development of new applications and new composite combinations.
Among the various markets for geosynthetics, the construction market was the largest in 2005 in terms of square metres, with onethird of the total. In addition, the total penetration of geosynthetics into building and some nonbuilding applications remains low, providing growth opportunities. In fact, the construction market will see the strongest gains through 2010 among the major geosynthetics markets.
"The road and other transportation construction market will also see above average gains, and the prospects for highway and street construction in the US will be buoyed by the implementation of projects financed by the Safe, Accountable, Flexible, Efficient Transportation Equity Act: A Legacy for Users (SAFETEA-LU), which was passed in August 2005, and which secures funding for projects through to the 2010 fiscal year," says the report.
Liquid containment and mining and other markets will see growth below the industry average through to 2010.
(The report Geosynthetics, 248 pages, is available for US$4,300 from The Freedonia Group, 767 Beta Drive, Cleveland, OH 4 4 1 43-2326. Further details con tact www.freedoniagroup. com).
Geosynthetics can, among other uses, be used for soil reinforcement, filtration and, separation; improving load-bearing capacities, erosion control,retaining walls and bridge abutments, asphalt reinforcement and deep foundations.
German bridge
Germany's first bridge abutment built with geosynthetic reinforced soil (GRS) used Fortrac geogrid fromAt Ilsenburg, Germany, GRS was used during bridge construction, where the tender issued by the Wernigerode local authority for the construction of a replacement bridge over the River Ilse as part of the upgrading of a district road, envisaged the bridge being supported on bored piles. The abutment was designed as an anchored gabion structure incorporating the piled elements.
However, a proposal from consulting engineers IBH-Herold & Partner Ingenieure, Weimar, acting for contractor
In place of load transfer through the piles, the proposal involved load transfer onto the GRS structure, onto which the abutment bearing shelf is directly cast. This structure comprises layers of fill, placed and compacted onto Fortrac geogrid.
The front face is constructed from galvanised steel gabion baskets filled with crushed stone, and the geogrid is double-looped around the steel facing and turned back. The reinforcement material, Fortrac geogrid type R140/30-30MP made from polyvinylalcohol (PVA), is said to be cost-effective, have excellent structural engineering properties and fulfils two important requirements.
"PVA geogrid has excellent long-term durability with a working life of 120 years, even when placed in a high pH fill (in this instance pH 10-11), and the geogrid has an extension under working load of much less than 6% and so is particularly suited to this situation, where only a very lowdeformation can be tolerated," says Huesker.
"The GRS construction method offers several advantages enabling the work to progress rapidly and above all with cost benefits." Compared with the client's original scheme, the GRS solution offered around a 30% saving, and was half the price of a conventional reinforced concrete substructure. Construction time was reduced by 25% on the client's scheme and 70% compared with the reinforced concrete version says the company.