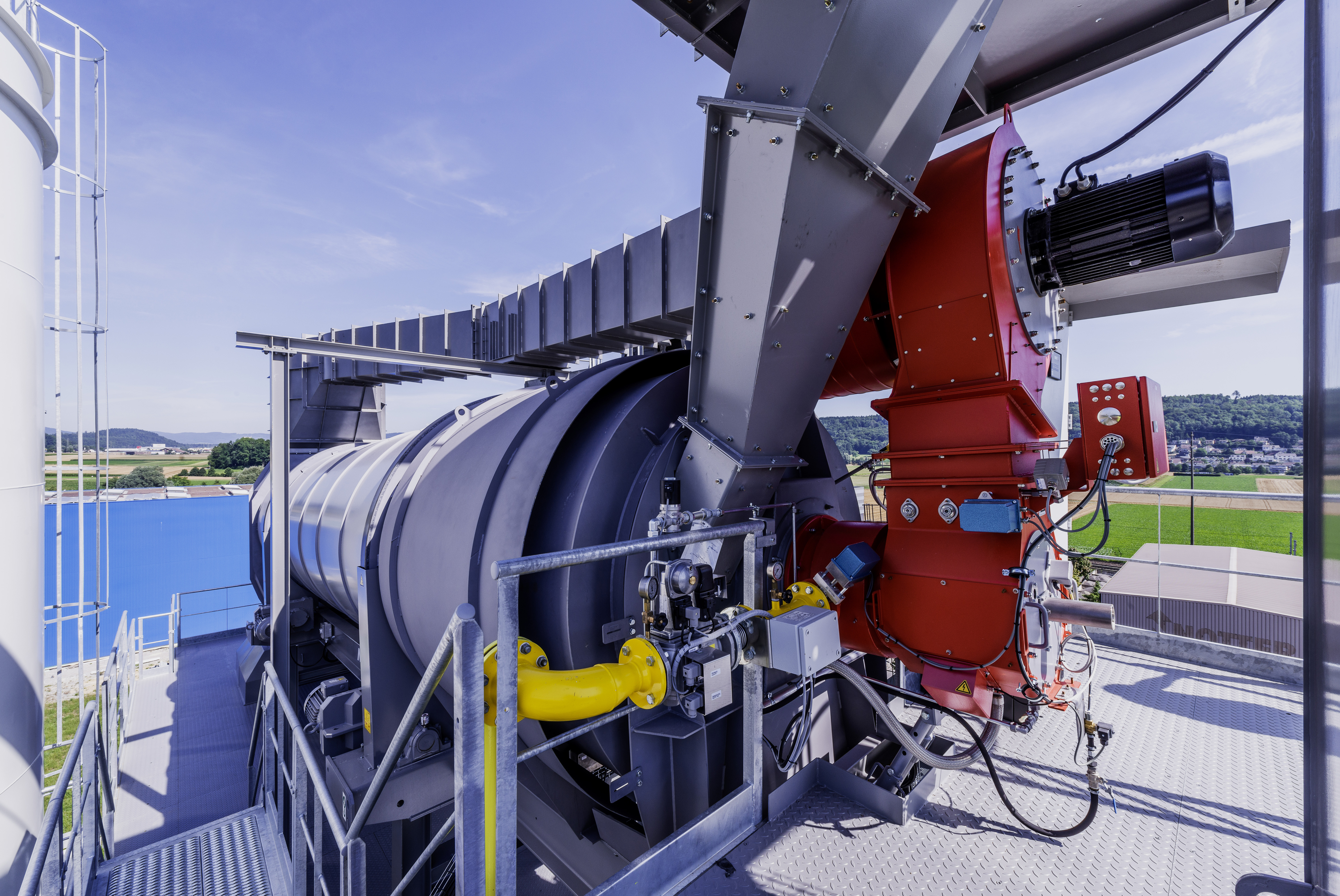
Environmentally friendly asphalt-mixing plants that minimise dust, noise and odour and maximise the use of RAP will be a highlight at the Ammann booth.
Ammann noise reduction solutions eliminate up to 25dBA, says the company. As well, bitumen fumes are reduced at points along the production process, including bitumen tanks, skip and load-out levels and the stack.
At the lower inexpensive end is the addition of cold RAP into the mixer; RAP and aggregates are dosed separately into the mixer. This process is available on new Ammann plants and as a retrofit on other manufacturers’ plants. RAP use of 25% to 40% is possible.
The addition of warm RAP via a separate RAH60 parallel dryer in combination with the cold feed system means 60% use of hot recycled materials is possible.
For recycling rates of 100%, according to the company, warm RAP with a counterflow RAP dryer which protects bitumen from damage during the heating process. The RAP is warmed so gently that there is no radiation heat making it a highly efficient system with extremely low emissions.
The focus then shifts to Ammann’s light compaction machines – “true latest lightweight champions”, according to the company. The full line-up will be on display, including vibratory plate compactors from a light 5kg to a much heavier 825kg model.
For the APH compaction series – with fully hydrostatic reversible vibratory plates, from 350-825kg – the company developed a triple-shaft exciter system for the largest plates in the Ammann portfolio. The third exciter shaft makes the machines easier to control while increasing the power and compaction forces. The system keeps plate movement consistent, which enables smooth travel - even through heavy, cohesive soils - and helps overcome steep grades. APH machines can even climb while backfilling saturated areas.