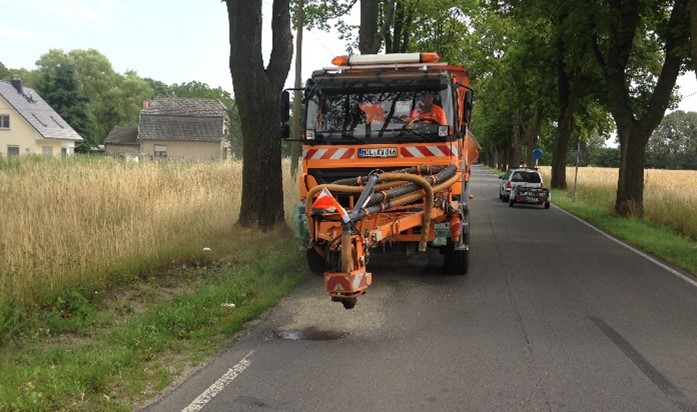
Strassmayr reports that its Blow Patcher STP 1010 is in full production after two years of on-site testing and evaluation with chosen customers in Europe.
The STP 1010 Blow Patcher, introduced at bauma 2019 in Munich, Germany, allows reparation of holes and general road surface damage without the use of milling machines and pavers. It requires only one person to operate system - the driver of the vehicle – using a joystick within the truck cabin. Delivery of aggregate and emulsion is done electronically.
“Technological, production and manual documentation is ready and the machines are in full production,” notes the company, based near Poznań in Poland. Several machines are already in operation in France, Germany, Belgium, Estonia and the Netherlands.
Because of the physical size of the machine and its specifications, Strassmayr says it expects the greatest interest will be by contractors and local authorities in Western Europe, “where the target customer is very demanding. It is for them that we have created a comprehensive and very effective system.”
Notably, the Blow Patcher comes in two versions. Each version carries 2,000 litres of emulsion. The STP 1010/4000 version carries 4m³ of aggregate and the STP 1010/6000 version carries 6m³ of aggregate.
Aggregates and emulsion stay separated in their own bins until the last moment before application. This means that there is no loss of material if, for any reason, the reparation process needs to be stopped at some stage. As well, there is no need to purchase small quantities of asphalt mixture each day.
Main engine
The system’s main engine is a HATZ 4H50TICD which fulfils exhaust emission regulation EPA Tier 4 Final. The vertical 4-cylinder liquid-cooled diesel engine puts out 55kW of power. It also has an engine radiator fan to ensure the most effective cooling. A hydraulic pump drives all the functions and there is a hydraulic oil tank with filter and temperature/oil level indicators. Meanwhile, a Kaeser OMEGA blower delivers more than enough air to “blow” the aggregate into place.
An access platform allowing easy access to the engine compartment including ladder. Finally, there is easy access to all engine components from the side of the unit.
Two hydraulic pumps handle emulsion processes. The larger pump is for circulation and loading/unloading of the emulsion while the smaller unit is for the spraying operation.
The introduction of the emulsion into the road surface hole is a two-step process. First, compressed air is blown into and around the hole. Next, the hole is flushed with a cleaning liquid.
Application of the emulsion is done using Strassmayr’s Easy Patch method. This automatic electronic system regulates the amount of emulsion in accordance with the amount of aggregates being delivered to repair the road surface. “Thanks to the electronic Easy Patch system, we have removed the risk of putting an incorrect amount of emulsion in the mixture,” notes the company.
The vehicle’s aggregate bin – whether with a 4m³ of 6m³ capacity – is divided into two sections to allow for two sizes of aggregate stone. Each bin section has its own hydraulic screw conveyor for delivering the aggregate to the road surface. There is also a manually operated cover to protect the bin and its contents in the case of rain.
The 2,000-litre emulsion bin is integrated into the body of the vehicle and is insulated with rockwool. A Riello diesel burner heats the emulsion and automatically controls its temperature.
Working arm
The system’s working arm, or boom, in the front of the vehicle is clearly visible to the driver and has an operational radius of between 3.5m and 4m. A ring of small nozzles at the end of the boom ensures proper mixture of emulsion and aggregate.
The speed of delivery of the aggregates can be reduced if there is spill-over outside the target area on the road surface during repair work. This means there is little loss of aggregate that otherwise would then end up being brushed off the road surface as surplus to reparation requirements.
All operations of the boom are done via a joystick system and a Siemens-manufactured touch screen.
To maintain a stable emulsion temperature, there is a pre-heating system for the pump body. This avoids temperature drops in the emulsion as the reparation process starts and the first amounts of emulsion pass through the pump.
Importantly, no crane is required to lift the system off the vehicle’s chassis. Raising the system off the chassis is done using six legs that are incorporated into the system itself. Adjusting the height of the legs, when raising the system for removal, is done manually.
Strassmayr has also incorporated a 200-litre water-spraying unit that is operated electrically. A water nozzle, also at the end of the boom, is useful for filling buckets or even washing hands. A series of spray bars in each aggregate bin section allows for easy and fast cleaning with water of the holding units.
Patch Portal
Strassmayr’s Patch Portal is an information and data analysis tool that works using GPS and GSM connections. Contractors and local authorities can confidently trace the unit’s location during repair work. Information on the portal includes a calculation of material used during operation and the location of potholes being repaired.
To ensure less down-time of the system, Patch Portal can check the technical condition of main system’s components. If a problem is detected, it will send a notification to a defined e-mail address or a text message to a listed mobile phone number.
Patch Portal also allows for the creation of a comparative database of several Blow Patchers operating in the field.