Mike Woof discusses some novel developments relating to bitumen In the developed countries of Western Europe there is an increasing shift away from new highway construction to maintaining and rebuilding existing roads. In Germany alone, a network of asphalt roads extending more than 600,000km will have to be maintained or repaired.
Highway maintenance techniques do vary between European countries but some commonalities exist. There are techniques that have been sidelined in the last few years but which now
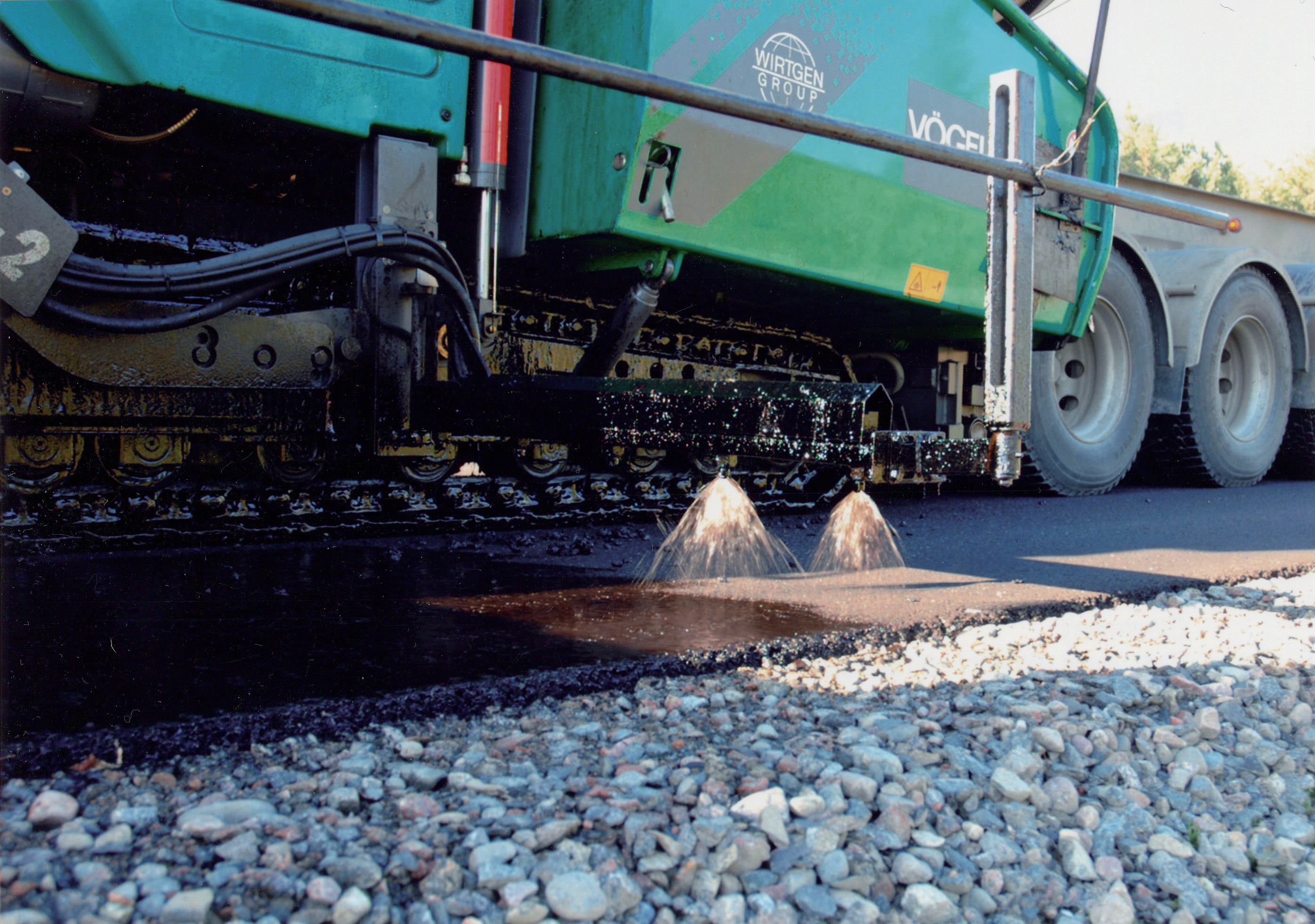
Using the Fintec crusher to recycle demolition waste is providing a useful source of roadbase material for the Xi'an Municipal Road and Facility Management Bureau
Mike Woof discusses some novel developments relating to bitumen
In the developed countries of Western Europe there is an increasing shift away from new highway construction to maintaining and rebuilding existing roads. In Germany alone, a network of asphalt roads extending more than 600,000km will have to be maintained or repaired.Highway maintenance techniques do vary between European countries but some commonalities exist. There are techniques that have been sidelined in the last few years but which now offer cost-competitive repair solutions with the development of new technologies. One of the most notable is for surface dressing, which in the past has been regarded as a cheap but comparatively low quality process. Surface dressing techniques have had a reputation for delivering road surfaces with higher than desirable running noise and loose chippings that can cause cracked windscreens (windshields) in an undesirably large number of vehicles.
However, according to UK-based specialist John Baxter, consultant director and secretary of the Road Surface Dressing Association (
This is an important point as polymer modification improves the cohesion of the binders and reduces temperature susceptibility. As a result, the surface dressing performance is significantly improved and the greater cohesion means that chippings will be retained. Meanwhile the improvements in temperature susceptibility mean that the binder will not become brittle in winter weather conditions, further improving chippings retention. In a similar vein, in hot weather the road surface will not soften.
Tests were carried out by the University of Ulster in partnership with the
Another key factor for the use of surface dressings has been the development of sophisticated equipment using computer controls to provide a consistent and accurate application rate for the binder. A sufficient and consistent binder thickness is vital to ensure that the chippings are retained. In the past the application rate would be controlled by varying the speed of the tanker, based on the driver's readings of a calibrated speedometer and this led to somewhat haphazard material thicknesses. But the new generation equipment uses a computer to control material delivery by linking the spray bar pump with the vehicle's powertrain to provide a far more accurate flow rate. Proper training practices have also been developed along with quality assurance systems, further helping improve the reliability of surface dressing applications according to Baxter.
Using surface dressing can help seal a pavement and provide sufficient skid resistance, offering an efficient and low cost repair option and as it is a cold process, energy costs are also low. When the surface dressing needs to be removed, conventional cold milling can be used while the recovered material can also be recycled using either foam bitumen processes or through a hot mix plant. Using cold recycling with either foam bitumen or emulsion-based processes with surface dressing also allows early opening of the road to traffic, reducing traffic disruption caused by repairs. Loose chippings can be swept up from the newly dressed surface and as these are generally of a high quality stone, they can be recycled into an asphalt plant for wearing course mixes or rewashed and used in the next batch of surface dressings.
Wider options
There are other repair techniques too. A specialist contractor Allied Drilling, which focuses on airfield maintenance and runway resurfacing, is using a purpose built, self contained machine, brought in from America, for applying hot bituminous materials and sealing joints. The
The new lighting is part of the Transition Project needed by Newquay Cornwall Airport to secure a Civil Aviation Authority Licence during the conversion of the military airfield at RAF St Mawgan to a civilian operated airport. The airfield's 2.75km long runway is capable of handling the largest aircraft, including the Boeing 747 and the double deck Airbus A380. Expansion of the arrivals and departure hall lounge and facilities to accommodate the increase in flights is also complete.
Allied Drilling is sawing about 15,000m of 15mm wide slots varying in depth from 100-255mm and sealing after the cables have been installed. The firm had been looking to replace hand applied sealing when it saw the Cimline, which has since proven faster, safer and easier to use than other methods. According to Allied Drilling, the job would have taken us twice as long using hand applied sealing and the new machine has saved the firm time and money. The company said that on some nights it has put over 1tonne of material through the machine and has already lined up other runway resurfacing projects. The firm also hopes to use the machine on motorways and trunk roads for sealing transverse and long horizontal joints.
The Cimline Magma 110 is one of a four-model range available in the UK through sole distributor Castellan Group in Milton Keynes. Safety is maximised as it means there is no longer a need to use propane gas-fired boilers and running back and forth with large watering cans full of hot bitumen to make a sealed joint. The technology is proven as the Cimline machines have been used in the US for around 20 years. The Magma 110 is a self contained, 415litre capacity, indirect heated diesel fired boiler, with a hydraulically driven pump and agitator. A diesel hydraulic drive system powers the material agitator and external pump, which circulates the temperature controlled, hot material through a 6m long heated flexible hose to a hand held lance with a variable flow nozzle controlled by the operator. The sealant comes in 15kg blocks, which are placed in the machine's heated mixing tank through angled splash-proof doors and can be ready for work within 40 minutes of initial start up. Emissions are low and the operator has greater control and accuracy of placing the very hot sealant directly where it is needed.
In the UAE's Alain Municipality, longitudinal and lateral cracks have been inspected in various city streets, revealing some 50,000 linear m of cracks. To repair these cracks hot applied sealant material is used, delivered in 15kg solid boxes, and loaded into a kettle with plastic cover/bags. The material is then heated up indirectly using hot oil in the oil jacket tank of the kettle prior to being injected into the routed crack through an oil jacketed hose. The material is injected at temperatures of 180-210ºC and the hose makes the job easier as there is no risk of suction or blockage.
According to Marathon Equipment, the crack sealing procedure involves a primary jobsite inspection followed by opening of the crack. The area can then be cleaned using a hot air lance and wind blower, prior to injection of the sealant material using the KERA 145 HD Kettle, with the final task being spreading of cement powder. Used properly, the technique is said to be highly productive and can be used to repair 1,000 linear m of crack/day, while the repaired road surface can be opened to traffic just 30 minutes after the work is carried out.
The SprayJet Module can be used for widths of 5m and is equipped with a 2000litre emulsion tank as standard, however an extra emulsion tank is now available as an option for contracts requiring very large rates of spread. The extra tank holds 5,000litres and is mounted in the paver hopper, providing a total capacity of 7,000litres in all.
For these applications, the paver can be supplied with mix from the MT1000-1 transfer unit. The material flows through a receiving bin in the extra tank and onto the paver's conveyors. A stand-alone, diesel-fired burner unit with a heating capacity of 30kW is installed in the extra tank to ensure that the emulsion remains at the necessary temperature. In addition the extra tank has its own pump circulating the emulsion and maintaining it in a highly homogeneous state. Should the emulsion level in the standard tank drop below 1,000litres, the material is automatically delivered from the extra tank into the standard tank.
Another upgrade for this module is an optional spray bar system for paving widths up to 6m. The lateral spray bars are longer and feature two additional nozzles, with a total of 24 nozzles for spraying. Combined with a Vögele AB600-2 screed or AB500-2 screed with bolt-on extensions, the machine is can handle pave widths up to 6m. ·