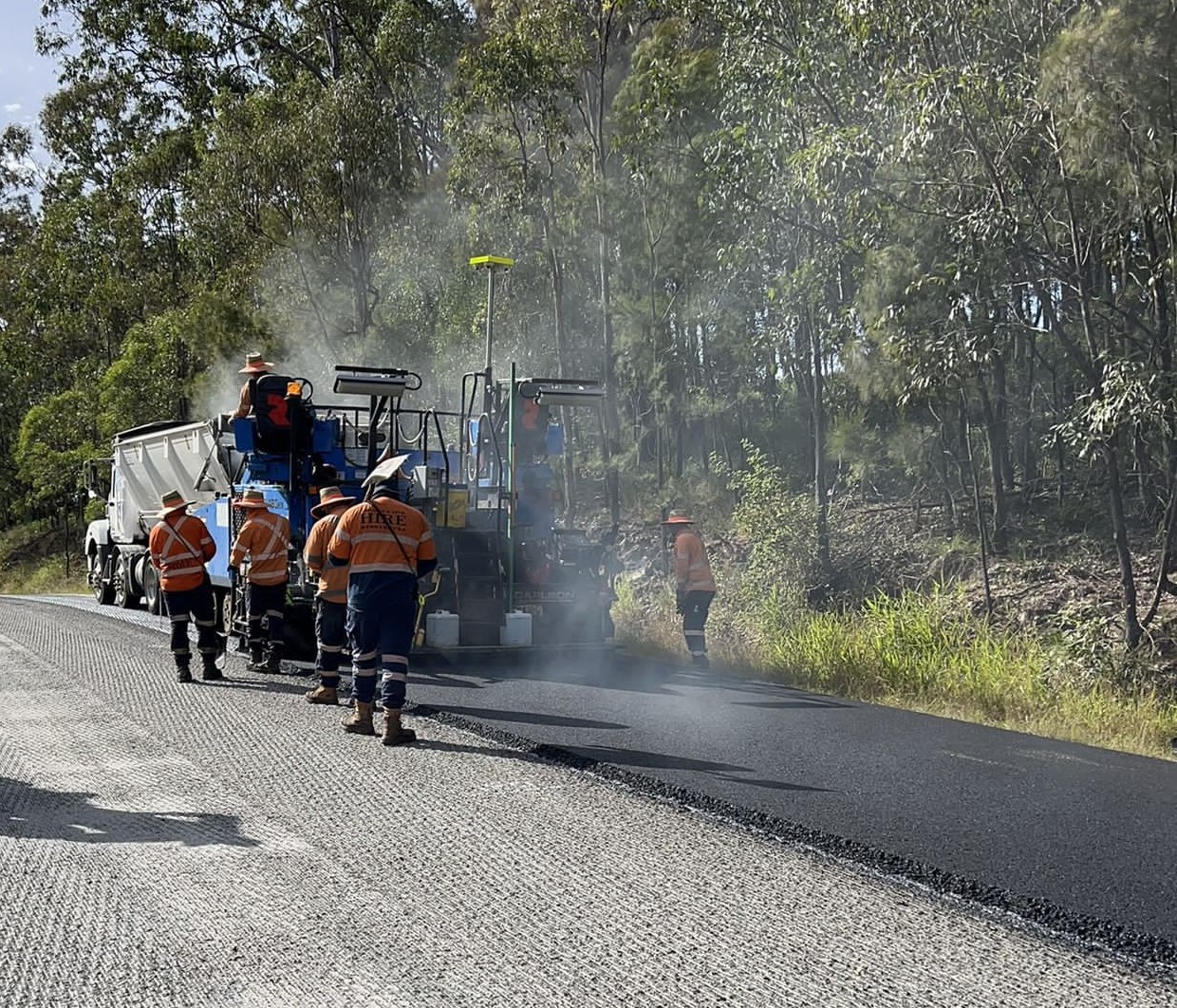
In Australia, construction product manufacturer and contractor Downer Group has announced that it will construct a A$10 million (US$6.5 million) asphalt manufacturing facility in Northern Tasmania, which will include technology for incorporating waste feeds in mixes. The new plant will replace an existing one that is near the end of its life, tripling the hourly production rate and will be set up to manufacture Downer’s Reconophalt, an asphalt mix modified with waste such as glass, toner cartridges and soft plastics.
Several Australian states are looking to increase their use of waste materials. Michael Ferguson, Tasmania’s minister for infrastructure and transport welcomed Downer’s investment. “The Tasmanian Liberal Government is expanding the use of recycled materials for our new roads around our State as a commitment to waste reduction in Tasmania,” he said.
The New South Wales Government wants to transition to a circular economy over the next 20 years, which involves finding more ways to use waste productively, reducing the need for virgin materials. It published plans for the first phase of its Waste and Sustainable Materials Strategy which will take it to 2027 in June 2021.
Reconophalt can contain a variety waste materials, with the recipe changing depending on the needs of the project and road authority. The materials used include soft plastic bags and packaging; waste glass; waste toner from printer cartridges; crumb rubber; coarse aggregates and sands from street sweepings; and RAP. So, for instance, Reconophalt 436 uses four recycled ingredients accounting for 36% by weight, Reconophalt 886 has eight recycled materials accounting for 86% by weight.
According to Downer, Reconophalt can be used in underlying base layers and non-modified wearing course asphalt to replace specification of a C170/C230 binder. With a cost that is competitive with standard asphalt, the product provides better fatigue performance – Downer says up to 65% improvement - better resistance to deformation and hence has lower whole-life costs. Downer says that mixes made with Reconophalt can be totally recycled at the end of their lives, to keep the loop going.
Downer first laid a road using Reconophalt in Craigieburn, Victoria in 2018, containing soft plastics, glass, toner and RAP. For every kilometre of two-lane road, Reconophalt used 200,000 recycled plastic bags, 63,000 recycled glass bottles, toner from 4,500 used printed cartridges, as well as 20% RAP.
Also in 2018, Downer laid a trial section in a street in Snug in Kingborough, Tasmania. Reconophalt has now been used in the Australia Capital Territory, News South Wales, South Australia and Western Australia with Reconophalt reporting that 300,000tonnes have been laid.
Using waste materials in road construction can raise concerns about health and the environment. These include dust exposure when working with crushed glass, toxicity, microplastics escaping and leaching of chemicals such as Bisphenol A (BPA) which is used in the manufacture of chemicals. Australia’s New South Wales (NSW) Environment Protection Authority tested Reconophalt extensively over 18 months to check on these concerns before approving it in May 2020.
Another major concern about the use of waste materials in roads is the quality of the feed and the risk of contamination. Materials for Reconophalt are sourced through partnerships with Close the Loop and Repurpose. Close the Loop manufactures TonerPlas which goes into the mix with Redcycle collecting soft plastics through Coles and Woolworths and Plastic Police collecting soft plastic through schools and councils.
Meanwhile, in Queensland trials of the Sripath rejuvenator are being carried out. Contractor Fulton Hogan has laid two trial sections of road containing Sripath Technologies’ ReLIXER rejuvenator in Brisbane and City of Gold Coast. The Australian Flexible Pavement Association (AFPA) organised the trial jointly with Fulton Hogan to find ways to use higher proportions of recycled asphalt planings (RAP), reducing carbon emissions.
“ReLIXER lowers the carbon footprint and greenhouse gas emissions. In high-RAP Mixes, it helps reduce the need for virgin bitumen and lowers the overall cost of the mix,” said Ravi Rajagopalan, general manager at Sripath Asia-Pac. “ReLIXER has been tested, vetted and adopted by experts from around the world, now also in Australia.” Specialists at Royal Melbourne Institute of Technology (RMIT) have carried out evaluation and testing of ReLIXER, according to Sripath.
Australia lags behind many developed countries in its use of RAP. Specifications vary between states, but generally only 10 or 15% RAP is used, which does not generally require the use of a rejuvenator. Higher proportions of RAP also require modifications to asphalt plants.
Fulton Hogan paved a trial section incorporating ReLIXER on Old Cleveland Road in Brisbane for Brisbane City Council. A mix containing 40% RAP and the ReLIXER rejuvenator will be compared against a standard mix, containing 15% RAP and no rejuvenator.
Chris Lange, technical manager at Fulton Hogan, said: “We have been very interested in green technologies, such as incorporating higher RAP content into mixes. We believe that this trial has provided us with a viable path forward”.
The second trial on Hymix Road in Gaven, City of Gold Coast (pictured), comprised a control section and three sections each using a mix with 40% RAP, A15E polymer modified binder and a different rejuvenator. Fulton Hogan organised the trial in conjunction with the Australian Flexible Pavement Association. Alongside ReLIXIR, rejuvenators VIATOP plus RC from TCL Hoffman and Ingevity’s Evoflex are under test.
ReLIXER, which was first launched commercially in North America in 2015, is a blend of plant-derived oils combined with a proprietary additives package. Sripath Technologies will not say what the oils are, only that they are not ones which can be used as a food. Evoflex is based on tall oil pitch. VIATOP plus RC is a combination of cellulose fibers and rejuvenators and is described as a "green product made of natural raw materials".