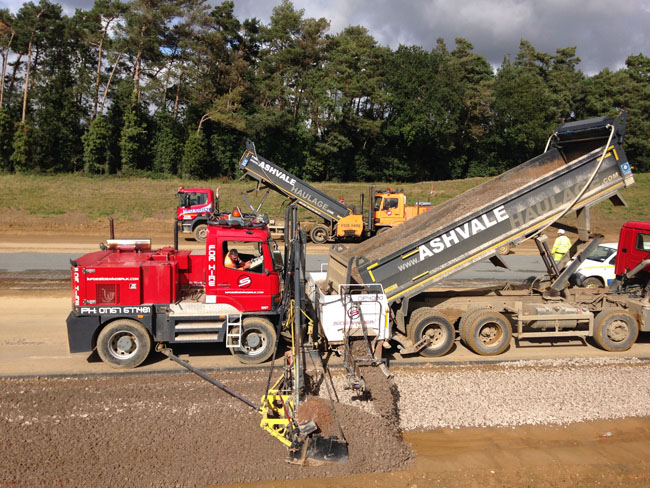
UK contractor
Excavators and dump trucks prepared the area for placement of sub-base material. The swale areas were constructed using both conventional methods as well as with the specialised
The materials used for the first trial were sand, lined with polyurethane membrane covered by a geotextile mat followed by two 100mm layers of Type 1 soil and 50mm of topsoil. Excavators prepared the formation for the swale and the Sidewinder placed material and formed the profile.
Material was delivered in trucks and tipped directly into the Sidewinder’s offset hopper, which transferred the material to the prepared area. Grade and slope for the swale levels were controlled using sonic grade and slope sensors, referencing from the road surface. Once the material was placed into the excavation to the required profile and level, the material was compacted using conventional rollers.
Due to the laying width limitation of the Sidewinder, different methods were tried to find the most appropriate method of achieving the required 4m width.
One method used the Sidewinder to pave the pre-existing 1m ledge with two 100mm layers of Type 1, which were then compacted to the required level. This allowed both the Sidewinder as well as the trucks delivering material to run on the step. The Sidewinder then made a second pass to pave the remaining 3m-wide area of swale. However, this method was later discounted as time-consuming and for safety reasons regarding the 800mm-wide roller.
Sand provides the profile of the swale and acted as a protective layer between the formation and the plastic waterproof liner. After sand was installed, topsoil infilled the void between the swale and the embankment.
A wheeled excavator fitted with a lifting frame rolled out the liner, after which it took nine personnel to finally position the heavy material. The liner was then covered with a geotextile to protect it from being punctured by the Type 1. The geotextile rolls were light enough to be rolled out by hand and a wheeled excavator placed Type 1 onto the geotextile to hold it in place. The Sidewinder could then place and grade the first layer of Type 1 to cover the liners, with a wheeled excavator assisting by placing Type 1 to the back of the swale. Each layer of material was compacted prior to the next being applied. This was done using tandem rollers with 0.8m- and 1m-wide drums.
Progress was hampered because the Sidewinder couldn’t maintain a full screed of material. A small auger used on the machine during footpath applications was then fitted to the Sidewinder.
To aid progress, a wheeled excavator worked ahead of the Sidewinder. It placed material from a truck, ensuring that the screed remained sufficiently full to complete the full profile. The final layer of topsoil was then installed.
The wheeled excavator placed material to complete the void between the swale and the embankment. The Sidewinder then made the final pass to finish the profile. Soil was not compacted but was later hydroseeded.
Trial 1
The trial area was 378m and it took six working days between 07:30 and 16:00. Setbacks of 2.5 days were incurred due to poor weather, a surfacing program, acquiring a permit to work as well as sourcing a lifting frame for the liner and a “Stop Work” for a management site visit.
It is safe to estimate that, using the Sidewinder, around 400m of swale can be completed in four working days. Despite the difficulty that the Sidewinder had in supplying material to the last metre of the screed, the Sidewinder discharged 20tonnes of material in under five minutes. Also, the ability to place and grade material to either left or right of the machine allowed safe working in live traffic conditions. Changeover time is less than 30 minutes.
Trial 2
The second trial included design changes proposed to the client in removing the sand and topsoil layers. Customised V-shaped swale buckets were used for the excavation of the formation and the placing and grading of Type 1. This trial used only excavators, dump trucks and standard tandem rollers for all work; it did not include a Sidewinder. The trial - using different methods - was to determine the time and resource to construct 100m of unlined swale using only traditional plant.
Method A of trial two involved the digger with the customised swale bucket excavating the swale formation to profile for a 4m length. A dumper placed Type 1 in the exposed area in front of the digger. The same digger then distributed the material to the swale profile and design depth before moving on to repeat the process.
The area was compacted using conventional rollers. Progress was slow and the 1m ledge adjacent to the carriageway could not be formed correctly without changing to a conventional bucket. Because only 30m were finished in the first two hours, this approach was abandoned.
For method B of trial two, one excavator with a modified bucket excavated the formation to the required shape and depth while a second wheeled excavator produced the 1m ledge directly adjacent to the carriageway. Type 1 was then introduced to the excavation using dumpers, then graded to profile by the excavator with the shaped bucket, followed by the wheeled excavator with a standard bucket trimming the 1m shelf adjacent to the carriageway. The area was then rolled using a 0.8m-wide roller.
The last 70m were completed in 3.5 hours.
Trial Findings
The trial two area was 100m unlined and it took 5.5 hours to finish, with no setbacks.
It was estimated that method B could produce 100m of completed unlined swale in five hours. To optimise this method, special attention is needed to the rotation of plant used to deliver Type 1directly on the swale.
Trial 2 required significantly less material with fewer operations that trail one.
Both trial two methods could produce an average of 100 linear metres per day of lined swales and 150m per day of unlined swales, at roughly the same cost. Trials indicated that major improvements in output were possible using the Sidewinder method, unlike with the conventional method. It was recommended to use the Sidewinder subcontractor.
Trial 3
After the second trials, Sidewinder UK had implemented design changes learned during the initial two trials. This included designing and manufacturing a heavier screed, installing a full-width auger, constructing a 3m-wide trapezoidal roller and the inclusion of a pole carrier to deploy the liner.
With these improvements productivity increased to an average 200-220m per day of lined swale and 250-300m per day for unlined swale. But problems with the auger caused delays. Due to these delays the Sidewinder subcontractor constructed an extension to the conveyor as discussed during the earlier trial.
Method
As larger areas became available it was possible to deploy two Sidewinders to further increase productivity. The first Sidewinder would bulk-fill the nearside half of the swale, leaving the second Sidewinder fitted with the extension conveyor to fill the outer half and produce the final profile. The trapezoidal roller reduced rolling time by 66%. Together these improvements raised productivity to over 700m per day. Careful planning was required as each Sidewinder could place and grade 20tonnes in under five minutes which is more than 1,400 tonnes per day.
The exercise resulted in the average linear metres per day increased from 100m on the first trial to 350m per day per Sidewinder. The swale was finished with hydroseeded grass.