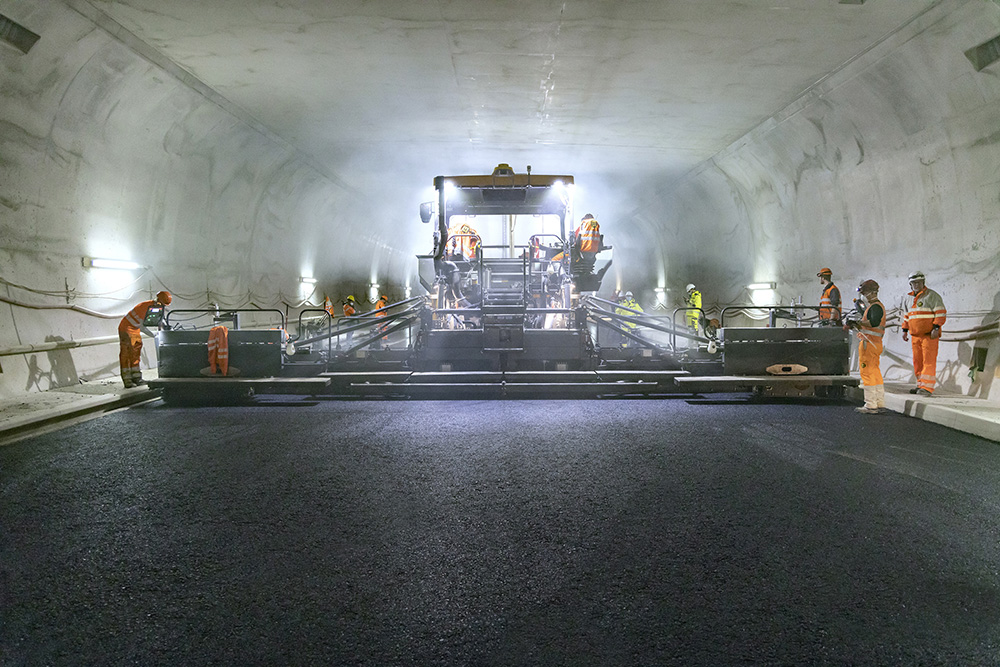
The tunnel has been one of the most complex infrastructure projects in Switzerland, with 2022 seeing the opening of the third bore. The Gubrist tunnel measures 3.2km long and forms part of Zurich's northern bypass.
With a diameter of 16m, it is the largest tunnel bore in Switzerland and is intended to relieve the chronic congestion of this section of road by providing three extra carriageways towards St Gallen/Bern.
Despite complex tunnel logistics, parallel working and heavy traffic, 20,000tonnes of asphalt had to be paved within a tight schedule and also meet stringent quality standards. So the contractor opted to use a digital road construction solution. “For a project of this scale, it was obvious that we should use a solution which enables us not only to visualise planning digitally, but also to control jobsite processes actively,” said Cedric Berrut, civil engineering operations manager.
The Vögele WITOS Paving Plus product was selected for the project, as software-based process optimisation solution network. The system can connect the construction manager to the mixing plant manager, the paving supervisor and the paver operator. The system consists of five modules for job site planning, mix provision, transport of mix, asphalt paving and process analysis. These functions can all be managed by the system in real time. The package also allows just-in-time delivery to the site and continuous paving with no paver stoppages. The paving team can also react to disruptions to the process.
At 11.5m, this was the widest paving project without joints ever completed in Switzerland. The firm also made key use of two Vögele machines for the project, an MT 3000-2i Offset PowerFeeder and a SUPER 2100-3i Road Paver fitted with the SB 300 Fixed-Width Screed. Over a 3.2km stretch of road, the contractor used the machines to pave base and binder courses that measured 80mm-thick combined, with a 40mm wearing course on top. According to Berrut, the firm relied on the sophisticated machine package to deliver a quality surface productively.
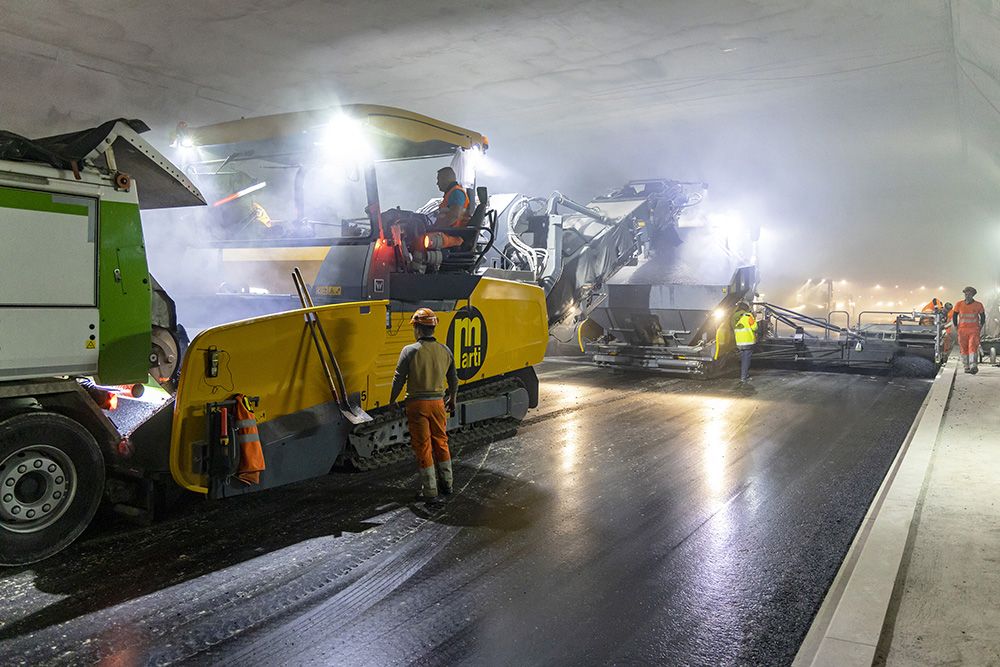
Paving the Gubrist tunnel required planners, construction managers and the paving team to take account of a number of challenges. The contractor’s mixing plant is 100km away. In order to avoid jams on a busy stretch of road and to minimise delays due to parallel working in the tunnel, the firm opted to pave at night. The Witos process optimisation solution simplified the logistics and the planners were able to record and monitor key parameters such as the quantities of material required, as well as machine status.
The system transmitted the quantities of material needed to the mixing plant, then compared this with data from the plant and calculated the schedule for the supply trucks and their arrival times onsite. “Planning and production of mix were much more accurate,” said Berrut. “This enabled us to match paving and compaction processes to suit material deliveries.”
The system gave paving supervisor, construction manager and paver operator a real-time overview of paving progress, laydown rate and mix delivery throughout the project.
The tablet PC or paver operator’s console enabled the team to detect deviations from the plan in terms of paving time, paving distance or mix quantities and react if necessary. “This enabled us to ensure continuous paving and thus the appropriate quality,” says Berrut. Evaluation in the analysis module furthermore resulted in a significant reduction in waiting times as a result of cycling, as well as in fewer mix trucks than on comparable job sites. “Ultimately, this means reduced material and transport costs, fewer emissions, better utilisation and at the same time, better quality.”
The system could also be used in difficult conditions such as those in the tunnel. In order to ensure reliable data transmission, the contractor used a GSM network that was routed into the tunnel by additional antennas. Berrut also said that the technology integrates well with digital infrastructure and provides data that can be used for BIM models.