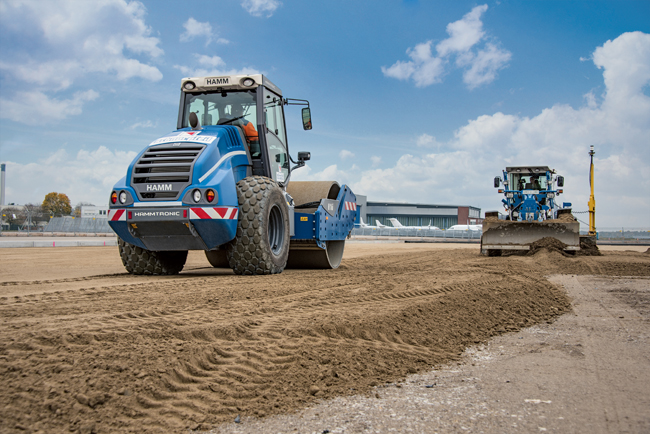
Using the
In autumn 2017, sections of the flight operations areas at Cologne/Bonn Airport were renovated. In this context, parts of the drainage system, including both the unbound superstructure and parts of the substructure, were also rehabilitated. The Wirtgen mobile cold recycling mixing plant prepared the material mix.
A new location usually also means a different formula, different mineral aggregates and different binders. But that was no problem for Alexander Weber of SAT Straßensanierung, because the KMA 220 can produce a wide range of mixes from new aggregates, milled material or other reclaimed road surfacing materials in an environmentally friendly process. Cement, bitumen emulsion or foamed bitumen can be added in the plant as a binder.
One of the key factors in the cost-effectiveness of the plant is its transportability. Erection and dismantling are also straightforward, because the work can be done without any special tools and no foundations are required.
Volkmar Gogol is the person at SAT who was responsible for setting up the KMA 220 and putting it into operation. He has been working with cold mixing plants from Wirtgen since as far back as 1990. “Today, I can mix between 150 and 220tonnes/hour with the KMA 220, depending on the material used and the formula.”
In six days, the mobile KMA 220 at Cologne/Bonn airport provided some 11,000tonnes of recycled material for the hydraulically bound base required for a surface area of about 60m x 600m in the area of the taxiway. The material actually consisted of RAP from a variety of projects in the region and parts of the hydraulically bound base from a construction site neighbouring the airport. To achieve the required strengths, 4.4% by volume of 32.5 R Portland cement and 1.2% by volume of water was added to the construction material. A total of six trucks transported the material from the KMA 220 straight to the installation site some 400m away.
Proven measuring and control technology in the KMA 220 ensures that the formula is followed. The aggregate is weighed on belt scales while on the take-off conveyor and fed continuously to the mixer.
Due the large tank capacities, the preparation of the hydraulically bound base at the Cologne/Bonn airport project also proceeded smoothly. This was confirmed by David Rose, site manager of general contractor Heinz Schnorpfeil Bau, “The plant keeps to the formula reliably and produces the desired quantities in the allotted time.” The KMA 220 continuously turned the recycled material into hydraulically bound base material that was then distributed over the surface of the site by a grader. Compaction was handled by a
Immediately after completion of the hydraulically bound base, a