UK firm Hanson hopes to attain key sustainability targets with its new ERA asphalt product. This energy reducing asphalt delivers a 50% reduction in carbon emissions while enhancing durability and improving health and safety for contractors. It can also use up to 50% recycled content, while the asphalt itself is 100% recyclable. The Hanson ERA production process allows a wide range of base, binder and surface course materials to be produced at temperatures of 80 and 95°C, compared with up to 190°C for equiv
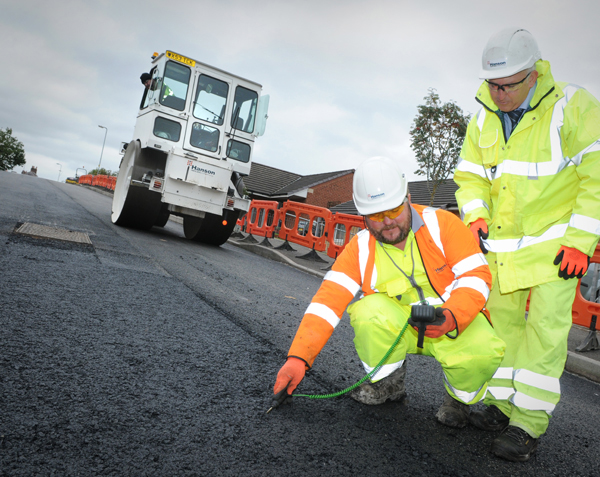
The novel Hanson ERA asphalt product features a high percentage of recycled materials
UK firm 2644 Hanson hopes to attain key sustainability targets with its new ERA asphalt product.
This energy reducing asphalt delivers a 50% reduction in carbon emissions while enhancing durability and improving health and safety for contractors. It can also use up to 50% recycled content, while the asphalt itself is 100% recyclable.
The Hanson ERA production process allows a wide range of base, binder and surface course materials to be produced at temperatures of 80 and 95°C, compared with up to 190°C for equivalent hot-mix asphalt. As well as the increased sustainability credentials, the lower temperature allows faster completion of resurfacing works, minimising time on site for contractors and disruption for motorists.
Hanson ERA can also help local authorities reduce waste and carbon emissions and meet sustainability targets. In the UK3348 Newport City Council was one of the first to use the material to resurface a bus route carrying heavy traffic loads. Andrew Morris, chief highway engineer at Newport City Council said, "Using Hanson ERA allowed the site to be planed out, resurfaced and reopened to traffic within a very short window of time. Testing has shown that the resistance to deformation is equivalent to standard hot-mix asphalt. We believe that adopting this new surface technology will help us meet our sustainability targets while providing durable longer lasting roads."
This energy reducing asphalt delivers a 50% reduction in carbon emissions while enhancing durability and improving health and safety for contractors. It can also use up to 50% recycled content, while the asphalt itself is 100% recyclable.
The Hanson ERA production process allows a wide range of base, binder and surface course materials to be produced at temperatures of 80 and 95°C, compared with up to 190°C for equivalent hot-mix asphalt. As well as the increased sustainability credentials, the lower temperature allows faster completion of resurfacing works, minimising time on site for contractors and disruption for motorists.
Hanson ERA can also help local authorities reduce waste and carbon emissions and meet sustainability targets. In the UK