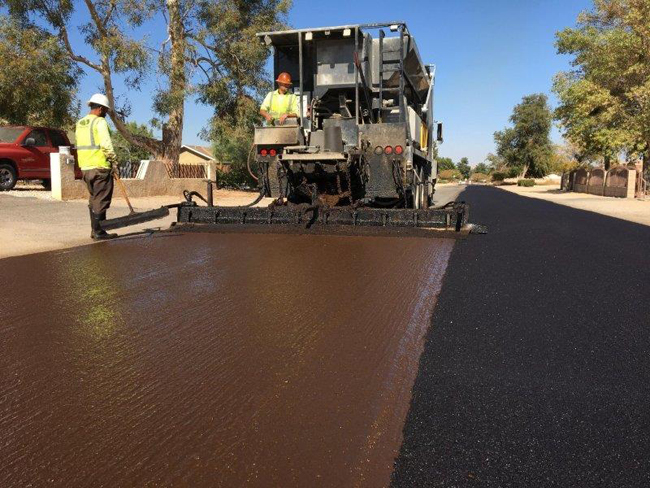
When RoadResouce.org went live – quietly - in July it was the end of two years of hard work by three US associations for pavement preservation.
But there was no grand party or ceremonial pushing of the “go live” button, says Doug Hogue, vice president and general manager of
“For all of us in the industry July is a busy period that left little time to celebrate on the opening day,” says Hogue, who is also vice president of
He along with members from the Asphalt Emulsion Manufacturers Association (AEMA) and the Asphalt Recycling and Reclaiming Association (ARRA), were heavily involved in the website’s development.
The project’s nascence was in 2016. AEMA was completing a marketing study to find ways to double the use of asphalt emulsions. But importantly, the marketing study found that there really was no place to go for agencies to find out about emulsion-based treatments or – importantly – to compare them.
PPRA as a platform
But AEMA realised that creating such a website was too big for one association. They came to the table through the PPRA and asked ISSA and ARRA if they would join in a project. Budgets were put together, each association had committees of like-minded people and an outside website creator was approached.
Even so, says Hogue, there was concern among some people that opening up data and comparing methods would reduce the use of one method in favour of another one or several others. In other words, the advice had to impartial and empirically-based and not be a commercial activity that pushed one method of preservation over another.
There was a soft launch only for members of the three associations in February and then it went live in late July for anyone to use. “All the associations hope it will be used internationally and the units are English and metric. But right now, the website’s currency is only US and Canadian dollars. The majority of our membership is US and Canadian so that is from where we have sound cost data.”
Cost figures for repairs generated by adding the project’s parameters including road condition can be only guidelines. But the results can be shared with an agency for all to see where project costs can be adjusted and where the agency’s money is best spent to get the best or desired road improvements. “This is what the treatment toolbox on the site is all about,” he says. It’s an open book discussion about processes that can boost trust in the private sector.
It is hoped that RoadResource.org will also promote innovation by contractor and agency, says Hogue, who has been with VSS Macropaver for nearly 26 years. “My main interest has always been machines but along the way I’ve had to learn a lot about the chemistry of asphalt. In our processes chemistry is very important to the function of the machines.”
Innovation
Typically a road that has large cracks and potholes would not be a candidate for slurry or micro-surfacing which is a wearing course. “But our sister company, VSS International, the largest US west coast contractor, has done some innovative thinking over the past decade. This included filling depressions, cracks and potholes with slurry and then using overlay with an asphalt rubber chip. This acts as a stress-absorbing interlayer because of the flexible asphalt rubber.
“Then they would come on top of that with microsurfacing. Those two would typically be called a cape seal [a chip seal covered with a slurry or micro-surface]. When microsurfacing is on top of a chip, you fill all the voids between the chips and it really looks like a newly paved road. So, you’ve levelled it by filling the voids, you’ve addressed the cracking issue through the flexible layer of chip seal. There has been years of extended life to a road that would have been at the end of its life.”