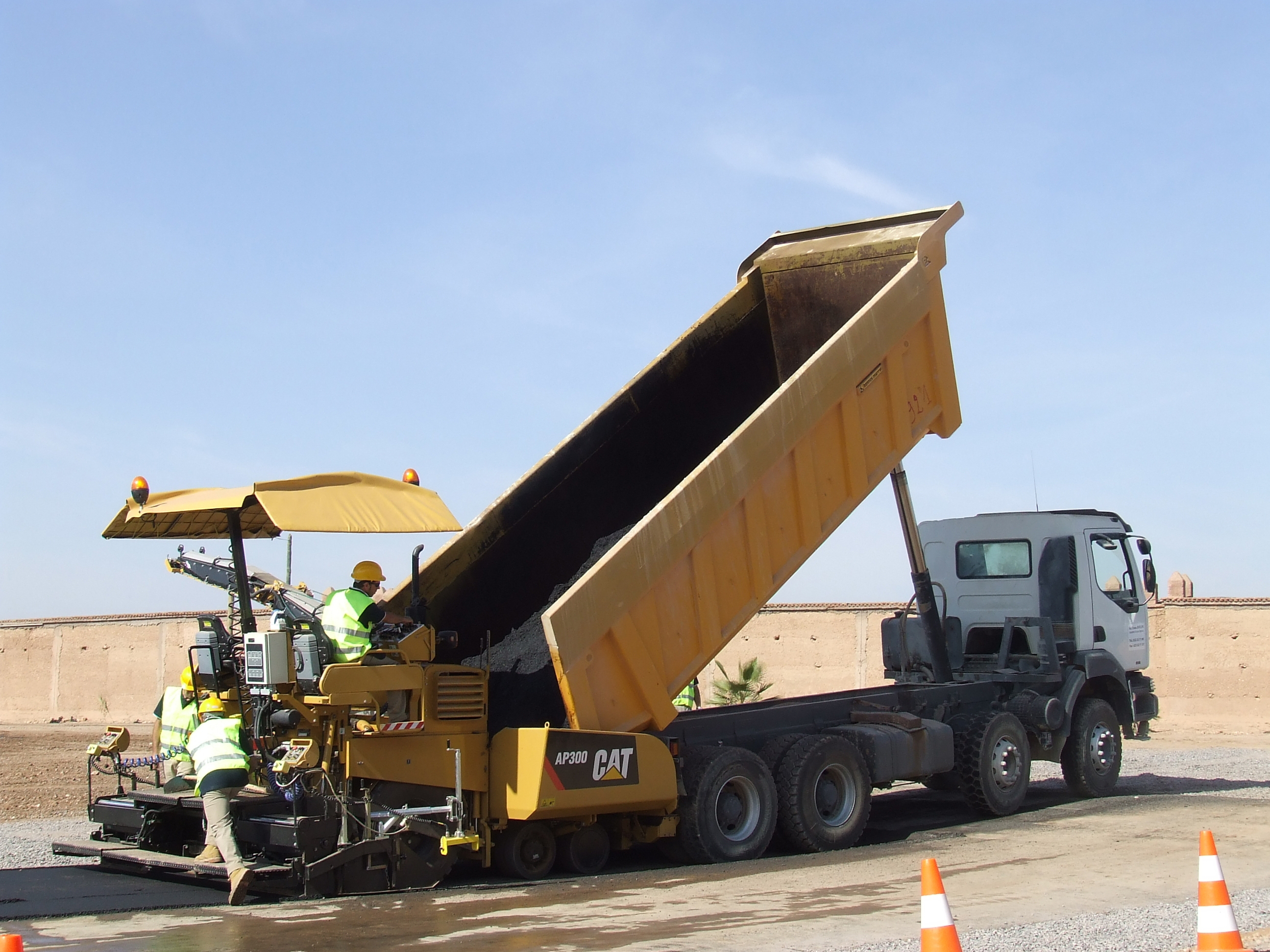
US and European asphalt paving needs are different, but some firms are bridging that gap, reports Mike Woof
With a clear differentiation between the US and European asphalt paving markets, manufacturers from the latter are now developing machines aimed at the former. The US and European markets for paving machines have developed along very different lines. North American pavers are designed for high throughputs and high paving rates, having been designed to meet a need to build roads over long distances with high productivity. Meanwhile European machines have tended to offer lower throughputs and paving rates because distances in Europe are shorter and instead these machines are equipped with screeds that can carry out a portion of the compaction work.Being a US-based firm,
Finish quality is another important target in asphalt paving as smoother surfaces are known to last longer.
But it is the
Dual languages
Slurry seal specialist
BOMAG's BF6615 has been designed for use by contractors in paving projects such as parking areas and streets. The machine has a low-profile engine hood that allows the operator good visibility of the hopper during loading, while twin driving positions mean the operator can find the best seating location to suit the application. Power for the 9.3tonne BF6615 comes from a
The key feature of the machine is its new NIMAT 2 full-width floating screed has a standard 2.44-4.57m paving width and is electrically heated, with dual vibrators working at 2,500vpm. The screed features two abrasion-resistant, reversible and independent hydraulic augers that extend with the screed extensions, providing consistent material control at all paving widths. The screed plates are bolted on for easy replacement and these are designed to withstand tough job-site conditions. Both the augers and dual hydraulic slat conveyors feature full automatic control with manual override.
The 8.1tonne hopper capacity on the BF6615 allows high-production paving to continue between trucks. However the powerful drive system means that even with its power saving system, the new paver can push asphalt feeder trucks while maintaining working speeds up to 55m/minute.
The BF6615 runs on standard bolt-on polyurethane track pads, with eight sealed rollers/side carrying the weight of the machine and bolt-on rock guards on the inside and outside of each track drive to prevent asphalt from building up on the chains.
Other features include a hydraulically lifting bed, a fume extraction system, wash down spray system, swivel mounted bumper rollers and power depth adjustment controls for variable mat thickness. Options include a swivel-mounted tow-type hydraulic truck hitch, working lights, ditch plates, simple
On a broadly similar role, Vögele's VISION Series pavers are product of a joint development project between the firm's engineering teams in Germany and the US. Although these are new models, the VISION Series shares proven features with the recently revamped Vögele Super Series paver line sold in Europe, such as high productivity, good all round visibility and low operating noise. The new North American range includes the tracked VISION 5200-2 paver and wheeled VISION 5203-2 version, both of which are aimed at large highway projects and designed for the 3.05m paving class. The VISION 5100-2 and 5103-2 are slightly more compact machines that are designed for urban applications in the 2.44m paving class and are tracked and wheeled machines respectively.
These four new pavers feature Vögele's sophisticated ErgoPlus control system. All four new models share a design operator's platform that has been designed to offer high visibility of the screed edges, feed, augers and hopper. Different screeds are available to suit different customer requests although the units come with Carlson screeds as standard.
To meet the market requirements of North American customers for high paving speeds, the machines offer high productivity, high material throughput rates and high power-to-weight ratios. The larger VISION 5200-2 and VISION 5203-2 pavers have throughput rates in excess of 1,173tonnes of mix/hour and are powered by Cummins diesels rated at 180kW. The VISION 5100-2 and VISION 5103-2 pavers can pave up to 631tonnes/hour and are also powered by Cummins diesels, rated at 127kW. All the engines meet the necessary Tier 3 exhaust emissions standards.
Meanwhile Carlson, best known for its popular screed range which is the leading brand in the US market, is now offering its own compact paver. The CP-90 is a small, crawler-based machine designed for use in housing developments and parking areas. The launch of this unit is significant as it shows Carlson is broadening its horizons and the CP-90 features one of the firm's trademark electric screeds as well as a two-speed hydrostatic drive.
It is worth noting that the machine Carlson showed at ConExpo was the prototype and was completed only shortly before the exhibition. A number of design improvements have already been planned for the subsequent units, which will be slightly more compact in terms of height and will also be slightly lighter than the first unit. Although the production units will be lower, they will still measure 1.73m long by 3.85m wide for transport as with the prototype. The target weight for the production models is 8.5tonnes and Carlson's sales/marketing manager Tom Travers explained that this is an important feature as it will allow the CP-90 to be carried to site on a small truck to reduce transport costs. By using a larger truck a paving contractor will be able to carry other equipment such as compaction machines, again cutting transport costs.
Although it is compact in size, the CP-90 can still be used for paving substantial widths from 1.21-4.57m. The screed developed for the CP-90 will not be made available to other paver manufacturers however. Simple in design, the CP-90 is said to be easy to service and maintain, which should help reduce running costs.
Travers said that this machine also features a somewhat stronger construction than other compact pavers in this size class, which is claimed to make it more durable than rival models. And to further ensure the CP-90 offers a long working life, durability and reliability Carlson has used a number of heavy duty components from much larger pavers built by sister company Roadtec. He said, "It's the first machine in this size with highway paver-class components." Again designed for North American requirements, VT
A novel use of asphalt paving equipment is being carried out in China. A Vögele machine is being used to lay an asphalt lining for water reservoirs and has to operate on a steep slope at an angle of 31º. The new hydro power station in Henan Province will use 3,000,000m3 to turn generators and produce 1,200MW of electricity. Two water reservoirs are being built and these are surrounded by retaining walls 31° steep. One of these reservoirs requires lining with an asphalt seal and a contractor, China Institute of Water Resources and Hydropower Research (IWHR) is using a Vögele SUPER 1800-2 paver, equipped with the firm's AB500-2 screed, for the task.
IWHR and Wirtgen China worked closely to configure the machine for the job, which requires placing 166,000m² of asphalt seal to be paved. Paving is carried out in two layers with a thickness of 10cm each. For the binder course, asphalt is used with a bitumen content of 4% and for the surface course asphalt with 7% of bitumen. This relatively high bitumen content is required for effective waterproofing. The SUPER 1800-2 paves 80m wide strips from bottom to top, with a 20mm liquid seal then sprayed on the finished lining. The machine paves vertical strips that vary in width from 2.5-4m and operates on the slope at around 1.5m/minute. A special electric drive shuttle vehicle that features an insulated dump body is used to supply the paver with hot mix on the steep slope, several times for each strip. An HD13 Hamm roller linked to a cable winch for safety, handles the compacting job to deliver the required final density for the lining.provides enough power to push a large truck during loading. The engine is transversely mounted, which allows for better maintenance access and cooling efficiency as well as allowing better visibility. The 9000 has dual hydraulic slide-out operator stations, with digital gauges for monitoring paver functions and diagnostics as well as touch-pad steering and a fume ventilation system. Two Series 90 variable-displacement pumps drive the paver functions.
The machine has an 11tonne hopper with heavy-duty, hydraulic radius hopper wings. Twin 457mm heavy-duty slat bar and roller chain conveyors feed the 406mm-diameter hardened cast steel augers that push asphalt to the screed. The auger assembly can be hydraulically raised and lowered, while standard sonic feed sensors control the augers. The 9000 is equipped with a heavy-duty, vibrating screed that is electrically-heated and extends hydraulically to offer paving widths from 2.43-4.72m. An onboard 20kW generator electrically heats the main screed and the front-mounted extensions.
The machine has an ergonomic computer located in front of the operator, which makes the machine easier to use as the material displays were previously located behind the operator. The Macropaver has no chain or sprocket drives, has large 3,216litre water and emulsion tanks and a maximum aggregate capacity of 9m³ While the recent ConExpo event in Las Vegas resulted in many manufacturers introducing models for the North American market, there has been some development of asphalt pavers for European customers too. Italian firm Antec has developed its wheeled PW2700 and tracked PT2700 to take the place of the former PT2600 model, as well as scoring strong sales with its pavers now being supplied to several countries and all of its scheduled production to the end of July being sold. The company says it has scored repeat orders in Norway and the UK through its local dealers while the firm also has dealers in Eastern Europe, Portugal and Australia. In addition
In addition Antec is now upgrading its tiny PW1500 paver, a 710kg machine design for small repairs that can pave widths from 250-800mm wide and up to 1.65m wide with screed extensions. Automatic screed heating and new controls allow the machine to pave to a higher quality, as well as making it easier to operate.
Caterpillar's new AP600D and AP300 have also been developed primarily for European rather than US customers. The AP600D is a 1.2tonne wheeled machine aimed at medium to high production paving and is fitted with the firm's AS4251C screed allowing paving widths from 2.55-5m, while bolt-on extensions allow a maximum 8m paving width. Customers can select either LPG or electric heating and can also choose from variable frequency tamper or vibrators. Power comes from a Cat C6.6 diesel rated at 129kW allowing paving speeds of 25m/min and travel speeds of 18km/h.
The wheeled AP300 is designed for the 6-8tonne weight class and features the AS3173 hydraulically extendable screed, again with a choice of LPG or electric heating. This screed allows paving widths of 1.7-3.20m, with a maximum 4m offered using bolt-on extensions and the hopper sides are designed to move independently to provide efficient material flow. Other features include: improved ergonomics; an engine mounted low in the chassis to maximise visibility; a variable frequency vibrating system; electronic ignition; and automatic and independent adjustment of the smoothing plate temperature
RSS