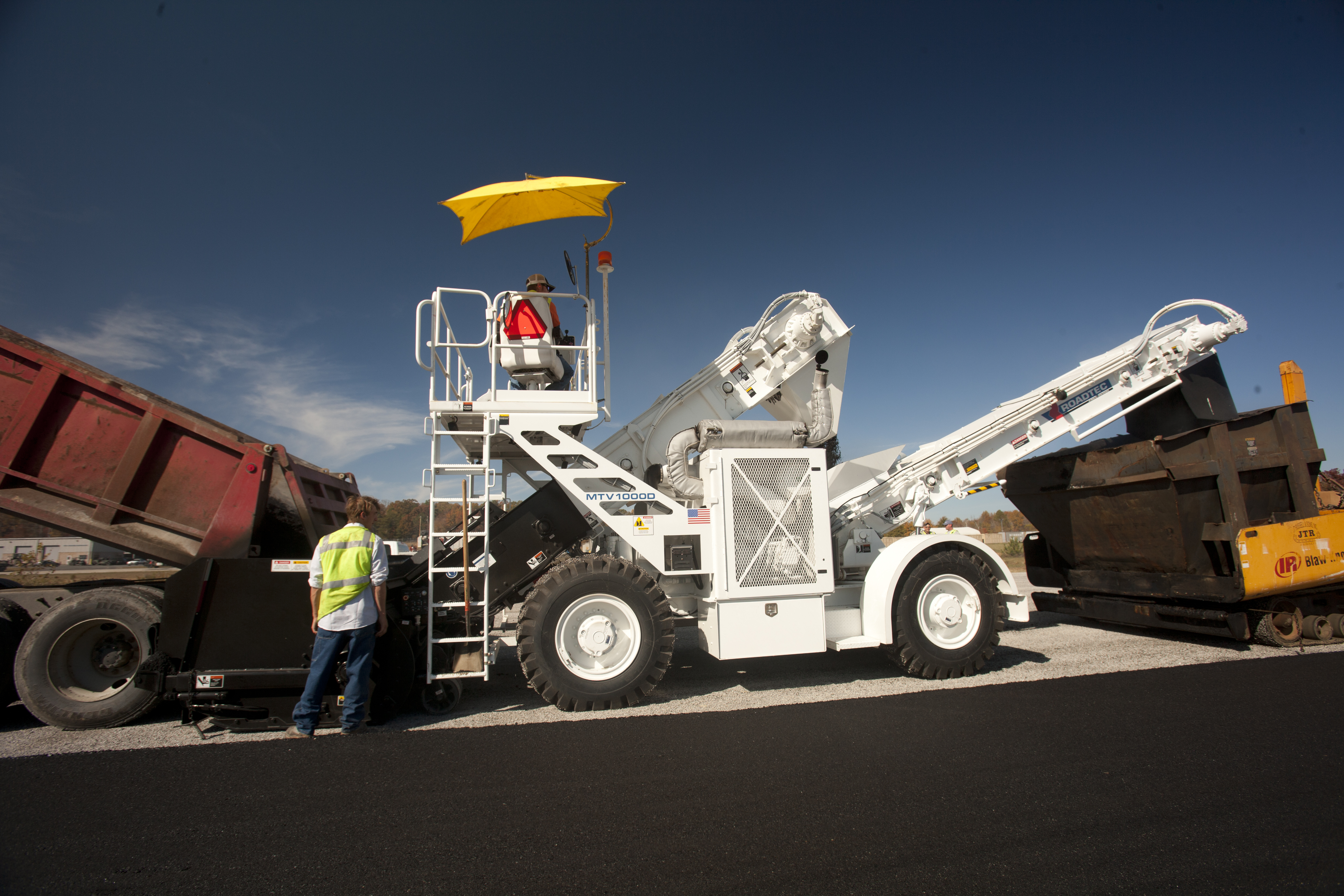
Several of the major asphalt paver manufacturers have unveiled new machines and systems that can optimise operations. Improved operating features for the
Some proven features have been retained, such as the high quality screeds, which benefit from a long and heavy design. Jonathan Stringham, vice president of marketing at BOMAG explained, “It has the heaviest screeds with the longest smoothing surfaces in its class.”
Customers can select either the S 500 or S 600 screeds, with standard paving widths using hydraulic extensions of 2.5-5m and 3-6m respectively. Maximum paving widths of 9m or 10m respectively can be achieved using bolt-on extensions. According to BOMAG, the screeds can deliver up to 94% pre-compaction, delivering a quality surface. The screeds also retain the well-proven Magmalife heating system, with coils embedded in aluminium plates and providing very fast heating times from start.
Power comes from a
Other features include the patented sideview system for the operator that allows the seat and console to slide up to 600mm over the side of the machine for a better view of paving operations. They also include a shock-mounted bumper roller to allow the truck to dock smoothly and this system combines with the integrated rocker to provide even material transfer.
A key development for the latest version of
John Irvine is president of the firm and said, “We received a patent on that. You can tell how many tonnes are going through the machine so you can tell when you need to rebuild the conveyor.” He added that this is a particularly important feature for countries or states with abrasive rock, such as Sweden or New Zealand, or US states such as Georgia. Irvine continued, “The conveyor slats are taller but move slower, so they wear less but carry more material.”
Meanwhile, other features designed to increase wear resistance inside the machine’s mixing area include chromium carbide wear liners and augers, while chain capacity has been increased.
Roadtec also offers a range of optional features for the Shuttle Buggy, including tyre spraying, an engagement system for trucks, a hopper level indicator, a lighting kit for night use and a lubrication system.
Also new from the company is the MTV 1000D material feeder, a simpler unit that features the high productivity but without the remixing capability of the Shuttle Buggy.
Meanwhile the firm has also developed its SP-100e Stealth Paver to work with its Shuttle Buggy and to meet the needs of North American customers. This has a streamlined design that is said to deliver a consistent quality, while featuring low maintenance needs and running costs. The machine works in tandem with the Roadtec Shuttle Buggy, with material fed directly to the auger from the hopper, minimising segregation. The hopper has a capacity of 10tonnes and has side chutes that prevent buildup, and electric flow gates allowing control of material movement. Gravity feeds material into the auger, eliminating the need for wear parts such as push rollers, slat conveyors, or tandem bogies. Maintenance and inspection areas are accessed from doors on the sides or the top of the paver. The lift hood is powered hydraulically, with a manual lift backup.
The driver for WITOS is the growing trend for client and contractor to document, in real time, the progress of paving projects. WITOS does this by bringing together the different players on the project - from construction managers to asphalt plant operators and truck drivers. The system ensures greater transparency across the entire paving process.
WITOS Paving, for example, can document how many trucks are approaching the job site and so allow the on-site team time to get ready for their arrival. As such, the pave speed can remain constant - which in turn improves paving quality.
One of the benefits of WITOS Paving is its integration into the ErgoPlus 3 operating system. This allows paver operators to receive a constant flow of information on their console display about incoming mix lorries and the current progress of construction - all without a separate display. All the requisite information is displayed directly in the paver operator's field of vision.
WITOS Paving has five function modules: control, materials, transport, jobsite and analysis. WITOS Paving Control, for instance, supports simple project planning by means of an assistant that guides the construction manager through all the parameters relevant for planning, step by step. The control module calculates the required quantity of mix as a function of the length and width and the variable geometries of the proposed construction project.
The number of trucks required to supply mix to the paver is passed on to the materials module. The system suggests a variable working cycle to the asphalt mixing plant supervisor, and this cycle is continually aligned with the frequently varying capacities of the lorries. In many cases that also allows the number of lorries required to be reduced, Vögele says.
Meanwhile Volvo Construction Equipment’s P6820D and P4820D ABG pavers are said to offer higher productivity after being fitted with the Swedish global OEM’s new EPM 3 central control system and new Pave Assist data management technology.
The EPM 3 system consolidates the control buttons, arranged in a bird’s-eye view layout, to guide the operator intuitively through individual working functions. The functions can be easily selected and adjusted using an ergonomically positioned jog wheel.
For single projects, the Settings Manager stores bespoke settings within the EPM 3, enabling the operator to recall saved parameters when encountering similar projects in the future. This feature is said to simplify machine start-up and can be fine-tuned by the operator once paving is underway to maximise productivity and job-to-job paving quality.
Powered by Volvo Co-Pilot, Pave Assist is designed to improve functionality, giving operators real-time insight to the quality and productivity of the paving operation. The highly innovative and Volvo in-house developed solution is said to help operators manage paving operations with a greater ease and autonomy. Tools available with Pave Assist include Material Manager, Thermal Profiling and Weather View.