With the launch of its innovative D7E diesel-electric bulldozer, Caterpillar has shaken up this traditionally conservative market Only rarely do product innovations come to market that can truly be described as groundbreaking, but Caterpillar's D7E fits that bill. To understand the giant leap that the D7E represents, it is important to recognise Caterpillar's long history in the bulldozer market, which is unmatched by any of its rivals.
Caterpillar pioneered the crawler track with founder, Ben Holt, havin
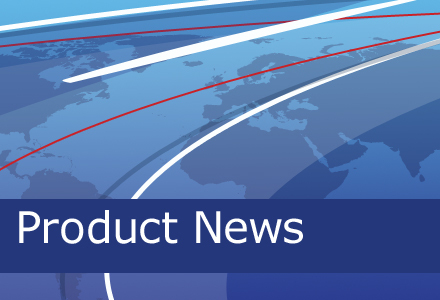
With the launch of its innovative D7E diesel-electric bulldozer, Caterpillar has shaken up this traditionally conservative market
Only rarely do product innovations come to market that can truly be described as groundbreaking, butCaterpillar pioneered the crawler track with founder, Ben Holt, having built the world's first successful tracked machine in 1904. The firm has played an increasingly dominant role in the world's bulldozer market ever since the first crude dozer blades were first fitted to crawler tractors around the time of WWI. Caterpillar's hold on the bulldozer market grew over the years and in the late 1970s the firm developed its distinctive high-drive undercarriage system for its mechanical drive bulldozers and this feature has been a cornerstone of its range ever since.
Until 2007, Caterpillar offered mechanical drive dozers only but this changed with the launch of the hydrostatic drive D6K. However the unveiling of the electric drive D7E prototype one year later was an even more radical move for the firm. As a result, Caterpillar is the position of being able to offer customers different dozer drivelines to suit different applications.
But it is worth recognising that the D7E is not the first tracked machine to have a diesel-electric powertrain. Dr Ferdinand
According to Caterpillar the electric drive offers numerous benefits with improved productivity and efficiency, greater versatility, easier operation, lower maintenance needs and reduced operating costs overall. David Nicoll, commercial manager for tractor products in the earthmoving division said, "Why did we start with the D7 class? We get asked that all the time. Well, it's right at the heart of the product line. We gave our engineers a clean sheet of paper. That doesn't happen very often at Caterpillar. It has a new cab and a new hydraulic system."
Nicoll claimed that the extensive field trials with customers show the D7E to be efficient and to offer a high dozing efficiency. He said, "It's a 10% more productive machine yet it uses 10-30% less fuel. Less fuel means less emissions. On average, we estimate it moves 25% more material/litre of fuel."
The electric motors have very low maintenance requirements and there are additional benefits from having a powerful electric generator on-board. Nicoll said, "Because we've got electric drive, we've had the opportunity to improve the electrical power systems. We've got a beltless engine and a self-contained heating, ventilation and air-conditioning system."
Mike Betz, engineering team leader for the new tractor platforms said, "Compared with the D7R, the D7E has a smaller engine that runs at lower rpm and that's one reason why it burns less fuel."
The D7E's propulsion module features two motors but the machine drives as if there is just one motor and steering is by the conventional differential system. The firm says it prefers to use the differential steer set-up instead of using separate motors for each track as this has been well proven in Caterpillar's existing dozer range. Betz said, "If we'd connected each motor to a track we wouldn't have had those benefits."
Because of the electric drive, start up from rest is more progressive than with a mechanical system and this will help cut wear and tear on the tracks, a significant saving for a bulldozer where undercarriage costs represent a substantial portion of overall running costs. The machine can carry out all the same jobs as a conventional bulldozer though, ranging from high production dozing to fine grading operations though and in many (if not most) applications, it will outperform Caterpillar's existing D7RII.
The 175kW Cat C9.3 engine is directly-coupled to a three phase, AC generator that is sealed and liquid-cooled. The generator provides sufficient electrical power to drive other machine functions as well and the electrical drive system is also liquid cooled and fully sealed and features integrated brakes and steering, as well as offering an infinitely variable array of speeds. The heavy-duty, double-reduction final drives are modular to reduce servicing while the propulsion system uses powertrain oil to simplify the cooling system. With no torque converter or powershift transmission, the D7E's cooling system is simpler and its drivetrain will require less maintenance than a conventional machine. All in all, the drive system of the D7E is covered by over 100 patents and Betz added, "This is a 100% Caterpillar-developed system."
To maximise safety, the electrical system is fully isolated and Betz said, "We also monitor electrical leakage to ground."
The D7E is the product of an intensive research and development programme that started at the firm's Tech Centre in Peoria and Betz said, "We started in the late 1990s on the development of this concept."
According to Caterpillar, the D7E costs around 12% less than the larger D8T and around 20% more than the conventional D7RII. However the company expects the reduced running costs with a 10% cut in costs/m3 moved to allow a payback time (over the cheaper D7RII) of around 30 months on average based on US fuel prices, and significantly less in some applications or in countries with higher fuel prices. All the same Caterpillar says that the D7RII will remain available until mid 2010.
The development process for the D7E has included extensive on-site trials with customers in the dirt and the feedback has been vital to fine-tuning the production models, as well as proving the concept. Firms that have used the D7E on-site have been extremely positive, saying that it can match the performance of the next size up of machine (D8) in some applications, as well as being easier to operate, offering greater visibility and burning less fuel than conventional machines in its class. The comments from those customers using the D7E have been extremely positive.
Dan Plote, owner of Illinois-based Plote Construction has used the D7E in a sand and gravel operation and said, "We've got a D7E on reclamation work on gravel pits. We parked a D8T to use this D7E and we're saving over 30% on fuel for the same work. When it hits a load of dirt, a traditional dozer will slow down but the D7E doesn't flinch."
Plote said that while his firm has yet to clock enough hours with the D7E to compare the expected cut in track wear, the undercarriage components for the D7E are smaller and cheaper than those for the larger D8T and that this will provide a substantial saving. Meanwhile Dole Hills Lignite in Louisiana has clocked somewhat more hours with the D7E and supervisor VJ Ropollo said that track wear rates are noticeably lower than for the firm's conventional D7R.
Like the smaller hydrostatic D6K, the D7E has a very different chassis to Caterpillar's more conventional mechanical drive bulldozers. As with the D6K, the designers of the D7E were free to mount the drive components much lower down in the chassis, lowering the centre of gravity and maximising stability. And as for the D6K, the D7E's engineers were able to design a simple and strong chassis without limits imposed by the configuration needs of a mechanical drivetrain. A combination of factors such as these mean that the 25.7tonne D7E (the 28.2tonne LGP version will be ready in 2010) is lighter than the firm's conventional D7R class dozers, further aiding fuel saving.
The machine is described as a diesel-electric hybrid by Caterpillar, though the firm is at pains to point out that there is no electrical storage capability in the shape of either batteries or capacitors. While it would be feasible to install batteries or capacitors, Nicoll said that the intensive working cycle of a bulldozer means that there is little cost advantage in fitting these, unlike wheeled loaders or excavators which have periods in the operating cycle where electric power can provide a practical option. For a bulldozer, reversing is generally the only part of the operating cycle when the machine is not under heavy load and where electrical power could be used, so the payback benefits from installing batteries would be longer. But the fuel saving gains already offered by the D7E with its smaller engine and efficient driveline will offer further benefits for some customers. Exhaust emission regulations are becoming extremely tough in many areas of the world with the US state of California having led the field and the prospect of a low fuel consumption, low emission bulldozer will prove attractive to contractors contending with such legislation. The D7E's combination of cost-effective, low emission and green credentials will likely win it custom in due course.
There is no small irony in the fact that Caterpillar's sophisticated D7E, arguably the world's most advanced bulldozer, is being built at the firm's East Peoria production facility. Track type tractors have been built at the East Peoria factory since 1910, predating the 1925 merger between the rival Holt and Best firms that formed Caterpillar. The D7E has passed all of its field trials and is in production now, with orders being taken and the first true production units heading to customers in Australia, Europe, North America and South America.
Bill Springer, vice president of quarry solutions, said that the D7E is one of the firm's most important product launches for years. He said, "I think the D7E is the best example of how we're trying to develop the company right now"