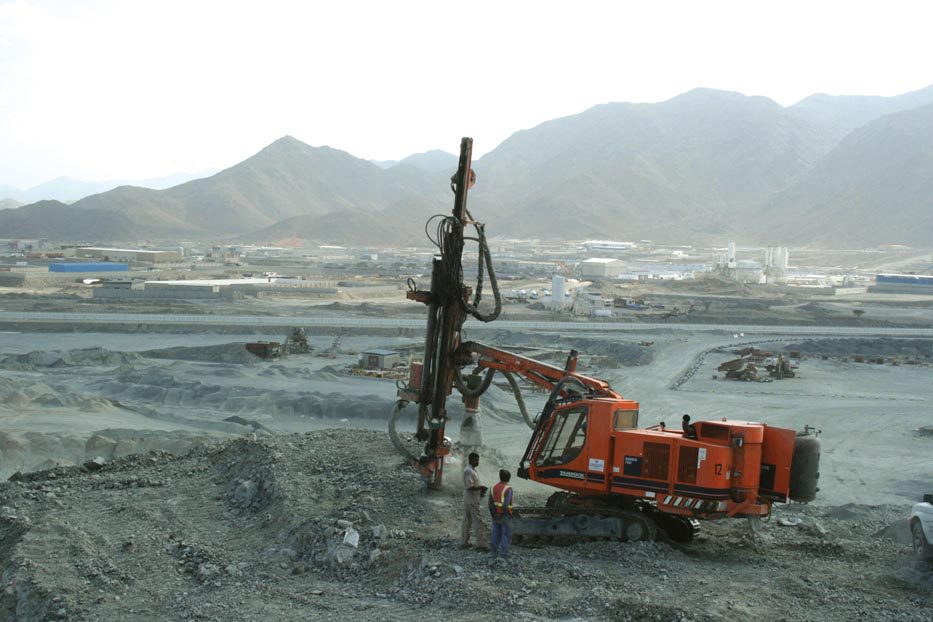
Recognised as one of the worlds hardest rocks, gabbro features a typical density in excess of 3tonnes/m, a crushing factor of 10 and a 61% silica content and demand remains strong for this quality construction material. Every hour of each day, a continuous team of trucks make the journey from the dozens of quarries in the Hajjar Mountains to projects across the UAE.
Despite the global economic slowdown, demand is still strong in the aggregate sector. With blasting strictly regulated across the Emirate, five companies specialise in drill and blast contracting for the quarrying sector. Market leader is Technical Drilling and Blasting, which specialises in quarry activities and handles contracts for around 24 quarries in Fujairah.
Technical manager Bill Armstrong of Technical Drilling and Blasting has a fleet of 16 surface top hammer drills and two DTH rigs, which includes nine Sandvik machines. According to project manager, Alok Ojha, the long life and productivity of its Sandvik rock tools, supplied through local distributor Dynatrade, has been a major benefit. He said, "Initially we used rock tools from the respective rig manufacturer but trials soon found that the Sandvik rock bits and rods were providing 100% longer operational life."
For the drill bits, life expectancy is up to three times longer when using the Sandvik Retrac bits. According to Armstrong the firm is achieving 700-800 drill metres/bit in the hard rock areas and up to 2000 drill metres in softer conditions. To ensure maximum performance the firm carries out bit regrinding after the first 400m with a second regrind after another 200m.
Each blast site is thoroughly surveyed and blasts are planned weeks in advance. UAE police and security witness all blasting operations and monitor the explosives used. However the growth in demand for aggregates has put extra strain on the police forces resources and the firm has been negotiating with the local authorities to make changes to restrictions. Until recently there have been restrictions on the quantities of explosives used and blaster have only been allowed to carry out two blasts/day at each site. However Technical Drilling and Blasting has demonstrated that using a single blast with a much greater quantity of explosive allows the police and other authorities to visit more sites without taking any extra time. And the firm is keen to show that further increases to the quantities of explosives used will make the process even more efficient.
Aggregate supply increase
A new Atlas Copco compressor is helping a Korean contractor meet its need for aggregates to complete construction work on the 75km road linking Nittambuwa and Kandy in Sri Lanka. An
Originally built by
The contractor opted for this unit as it already has a fleet of 10 Atlas Copco compressors in Sri Lanka, mostly XAS186's working on the highway projects. For three quarry operations, Keangnam had relied on the combination of Atlas Copco XAMS405 compressors and ROC442 PC drill rigs.
"Delivery of the latest XAMS856 compressor allowed us to increase production with ease," said plant manager, HLS de Zoysa, confirming that the rock encountered at Thulhiriya was very hard Gneiss with a hardness factor of 19.5.
The latest compressor is generally used for drilling at 6bar, "but," confirmed de Zoysa, "when really hard rock is excavated it can easily provide up to 8.6bar."
Complying with strict blasting controls, the contractor is generally drilling 15 holes x 6m depths for daily blasting using 65mm diameter holes; with holes taking up to 30 minutes to drill.