Rebuilding of one of the oldest motorways in Germany is testing out the possibilities for public-private project road construction reports Adrian Greeman
A freshly renovated section of the A8 Autobahn in southern Germany will be watched with some interest this summer as traffic begins driving along its rebuilt carriageway and additional third lanes. That is not because of any special road features, other than a distinctive reddish colour to its concrete surface, but because it is a first fullscale public
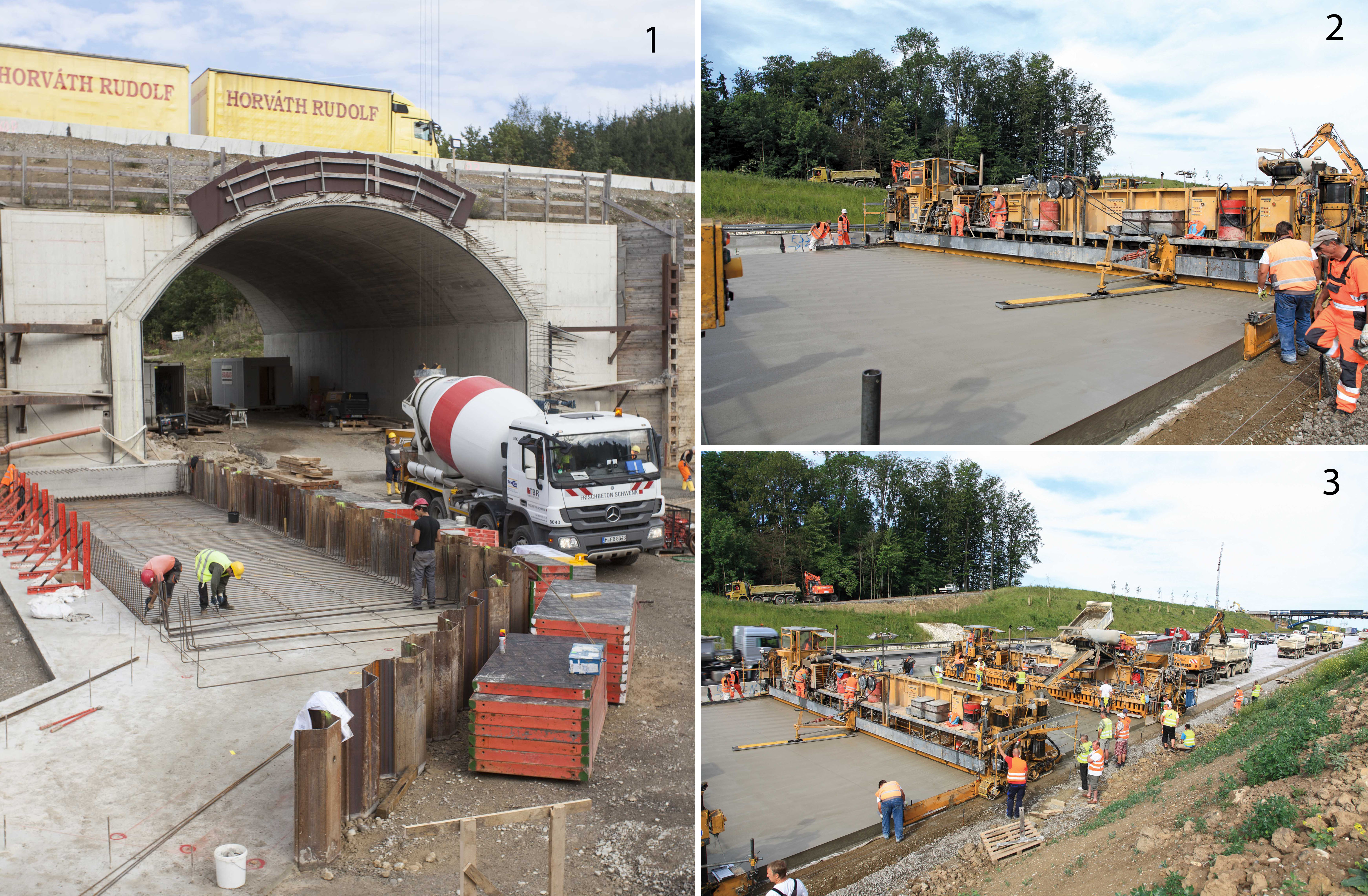
1. There are 79 bridges in all along the route; 2. Continuous checks of the surface are made to ensure it meets the tight specification; 3. Operating the paving train efficiently calls for effective logistics with regards to materials supply
Rebuilding of one of the oldest motorways in Germany is testing out the possibilities for public-private project road construction reports Adrian Greeman
A freshly renovated section of the A8 Autobahn in southern Germany will be watched with some interest this summer as traffic begins driving along its rebuilt carriageway and additional third lanes. That is not because of any special road features, other than a distinctive reddish colour to its concrete surface, but because it is a first full-scale public-private partnership scheme in the country and a possible harbinger of future development.
"Unlike many other European countries, Germany has not made much use of private sector investment in this way to date," said Gianluca Beraldo, technical director for Pansuevia, a joint venture finance and operating company that is overseeing the road upgrade and then maintenance and operation for the next 30 years. "But I think it is a good way to go."
The company, which uses the old Roman name for Bavaria, Suevia, is a special-purpose vehicle jointly set up by contractors945 Strabag from Austria and 981 Hochtief Solutions. It has been building the project since 2011 along a stretch of road between Ulm and Augsburg - one part lying in Baden-Württemberg and the other in Bavaria. It will join on to another rebuilt section from Augsburg on to Munich, which was completed in 2010 as a first stage.
The A8 is one of the oldest of the original autobahn routes and dates back to the mid-1930s when it was one of several, then strategic, highways built as much for military movements as for civilian traffic. The first autobahns feature long straight sections with a secondary purpose in mind for temporary use by military aircraft. In places, the twin lanes of the A8 still featured the original robust concrete structure of the time, although overlaid with asphalt in recent years. The route forms the southern of two east-west transport corridors through to Munich, the other running from Frankfurt through Nuremburg and then south to the Bavarian capital.
"Most newbuild and renovation work for autobahns is done directly at the Federal Republic level (Bundesrepublik) but in recent years the country has been looking at the options for some private investment," said Beraldo. This has come about partly because Germany introduced a tolling system for freight transport back in 2005. The LKW Maut system, run by the Toll Collect consortium of3992 Daimler-Chrysler, Deutsche Telecom and France's 6031 Cofiroute, works with on-board tracker units on trucks. These units monitor the distance travelled using GPS and the tachometers and are now almost universal on major trucks, known as LKWs in Germany.
Charges are imposed on all trucks that are more than 12tonnes according to distance, the emission class of the truck and the number of axles, which affects the wear rate on road surfaces. A fairly controversial government decision in March this year means the system will also be applied to foreign cars travelling through Germany. It is also possible the truck weight threshold will be reduced to 7.5tonnes.
But whatever happens the toll system provided a basis for a number of road projects to be bid in recent years on a private finance basis, said Beraldo. Four or five experimental schemes have been tried to see how it would work out. "It did not work out exceptionally well," he explained.
This is because the payback for the projects was based on a percentage of the tolls. These were collected by the federal system and then handed over. "But the difficulty is that the payback can vary considerably if fleet transport operators upgrade their vehicles," said Beraldo.
Operators have every incentive to do this, because the emissions class component of the toll calculation and the axle numbers can significantly reduce the toll rate. "But because you cannot foresee the rate of fleet upgrades, it makes revenue streams difficult to assess and predict precisely, which is important for financing schemes." The state of the economy, especially after the 2008 world financial crisis, also had an effect, slowing down some operators' investment plans and reducing freight movements and tonnage on the roads.
As a result, Pansuevia's project is being done on a different basis using a shadow tolling arrangement simply calculated on highway traffic alone rather than the classes of vehicles. It is likely to be the only one like it, however, as subsequent projects are using a road availability as the basis for payments Beraldo said, with payments reduced when flows are reduced for maintenance.
"We also have penalties for lane use reductions but only for major road works" he added.
Pansuevia's project is in two parts, the reconstruction and widening work, which covers a section of the road more than 41km and the maintenance and operation contract for both that section and for an additional 16km of road towards Ulm, which will remain as original motorway. The maintenance work began immediately with the contract, which was finalised in June 2011 after a long period of negotiation and will continue over 30 years.
"The motorway is already an operating route and has to remain so throughout the reconstruction and rebuilding," explained Beraldo. Initially he said, the work was carried out from an old depot belonging to the client near the west end of the concession. But he added that immediately the project was let, a plot of land was bought in the middle of the section for the new operations and maintenance (O&M) centre, which then opened in May 2012.
Maintenance covers the full range of operations needed to keep a motorway going. This ranges from dealing with snow and ice in the winter, which can be relatively severe in this central European location, to trimming and cutting vegetation, cleaning the motorway and its structures and removing graffiti. All this work is done from the depot close to the halfway point, where snow ploughs, trucks, a salt store and a vehicle workshop are kept and that is also home to the control centre.
"We have a GPS-based management system for the project, to track vehicles and personnel locations and plans operations" said Beraldo. The control system works with a series of dashboards and maps to show work operations and accidents when they occur, and draws in local detailed weather information, too. It was worked up in conjunction with software house Novasib in Efurt from an original software used by Hochtief for winter salting works elsewhere. "We looked at some other solutions and were offered one by a Swiss company but they were all over-complex and expensive," he said.
Accidents are tackled by the local emergency services with Pansuevia providing traffic diversions and lane control. "One of the biggest problems is big lorries, which just veer off the road," said Beraldo, "and you do wonder sometimes if they are reading the paper or something."
The need for maintenance has very much informed the reconstruction work and the road carriageway design. The old two-lane highway has been covered in asphalt overlays for many years but will now be reverting to a concrete design according to Beraldo. The point is to reduce the need for resurfacing to a minimum over the maintenance period; asphalt would require resurfacing during the concession term whereas concrete does not. "That reduces the amount of lane possessions we will need, which cost money from the toll revenue because of reduced road availability."
There is some asphalt work being done he said, namely for the 16km of road near Ulm, which is not being rebuilt, but will need some work shortly. "But we decided to include resurfacing on this stretch to be able to start with a clean sheet as it were."
Work for the longer stretch was let to a three-firm consortium comprising Hochtief, which has 50%, Germany's Züblin, which is now owned by Strabag, and concreting specialist Heilit & Woerner. The contract, worth some €400 million, is primarily for remaking the road as a new three-lane dual carriageway and hard shoulder.
"The old alignment is not to modern standards for curves and gradients so those have to be improved and there are a number of bridges and culvert structures – some 79 bridges in fact," said Beraldo, "including three interchanges. There are 38 water retention basins and 8.5km of noise protection".
He added, "But there is nothing significant in terms of major structures. The biggest are actually 'green bridges' for animal passage." There are two of these, which are more like covered sections of the motorway, 50m long and with topsoil and vegetation above. Using motorway fencing they funnel animals in the surrounding forest to the crossing points to recreate natural links between the two sides of the autobahn.
Construction work on the road itself, which finishes this year, is in three phases, widening the sides, diverting traffic and rebuilding the central road, first on one side, and then the other. "We also did the construction in sections with breaks in between," said Beraldo. The outer carriageways can be built first but the central phase of the work involves diverting traffic on to one side of the motorway, once the new lanes are in place. Traffic is confined to one side in narrowed lanes. To avoid driver fatigue, and to let the traffic sort itself out, the reconstruction has breaks, allowing the full motorway to be used at intervals; these sections are then done themselves. The complicated logistics have been a key part of construction planning.
Work began with an earthmoving operation to widen the road, particularly at the end nearest to Ulm where it descends from the so-called Schwäbishche Alps, a picturesque hilly region, most of which is national parkland and forest. The road path had to be cut back for the third lane and in places provided with retaining walls.
But the main operation has been rebuilding the carriageway and widening it out. First the old material has to be broken out, at least in the four lanes of the old part, most of the old concrete being crushed and finding its way back into the road. Where possible it goes into the sub-base or, if unsuitable, into base material for underpasses.
Then comes a ground mixing operation to improve the basic ground capacity. A big2395 Wirtgen stabiliser is being used to add the lime and churn it into the ground followed by a 172 BOMAG compactor. The result is an improved basic bearing capacity from 45N/m2 to 75N/m2 which allows a reduction in the bottom layer of the road itself, reduced from 360mm to 260mm said Beraldo. On top of that is 150mm thick layer of lean mix cement bound granular material for frost protection.
The 260,000m3 of lean mix has been supplied from its own batching plant at a works depot at approximately the halfway point along the project. A second larger batching plant makes the 360,000m3 of concrete for the main road structure here as well.
Above the bound layer is a geofabric, said Beraldo, before the two-layer concrete carriageway is laid above. "That allows the concrete to move freely when it expands and contracts," he explained.
The concrete road carriageway itself has two layers, the main part 240mm thick and a top riding layer of 50cm. These are laid simultaneously, 'wet on wet', using two full-width paving machines, separated by a 6m gap, said Beraldo. A small conveyor unit lifts concrete deliveries over the top of the first machine to the second. The construction JV has used Heilit & Woerner's own make of machines, which have proved excellent said Beraldo. They are capable of laying a full 15m width in one pass.
The sequence involves the first machine placing a main 240mm layer with reinforcement dowells inserted. There are also anchors installed for the longitudinal joints that run 5m apart. "The anchors are embedded whereas the dowels are sleeved to allow expansion movements," said Beraldo. "They are just to stop shear movements."
A top 50mm layer by the second machine uses a smaller and better aggregate he said, with a polish resistance to give skid resistance. Behind that comes a final bridge from which any flaws can be corrected manually and from which a top coating is applied. This is a sealing chemical for preventing drying during the initial cure and also has a retarder that holds back the hardening of about 3mm of the surface.
"Some hours later a steel brush is used to remove the matrix, leaving the aggregate protruding from the hardened concrete," explained Beraldo. "You need some experience to judge the right moment. But it slightly roughens the surface with small voids, which allow air to escape when it is compressed beneath the tyres, and that reduces noise by a few decibels."
A second follow-up operation, again time-critical depending on weather particularly, is cutting 100mm deep grooves to induce the natural shrinkage cracking during concrete curing to take place at just the required point for the joints. "It is almost magical how the concrete will crack at just the right point," he said.
Once hard enough the joints also have to be sealed against water ingress and the danger of water penetration, leading to frost-thaw damage deeper into the road structure. In previous times pitch was used to fill the gaps, but nowadays a plastic insert goes in. "They need replacing about once every 10 years," said Beraldo.
Concreting goes quite fast he said with 500m achieved/day during much of the work and to complete the schedule, day and night working producing 1km a day last year. The resultant carriageway has a slight pinkish tinge because the aggregate was imported from a source some distance away where the quarried rock is pinkish. This is because the local material is a limestone with a potential vulnerability to alkali-aggregate reaction, the so-called 'concrete cancer' that causes an expansion inside the concrete over many years and can crack and burst the concrete. The JV opted to use the pinkish limestone because it would avoid this risk.
Much of the concreting was finished by late spring this year with a few remaining stretches being completed and some structure to be done. Two early temporary bridges installed to keep traffic flowing during the works have to be replaced with permanent structures, for example.
Beraldo is pleased with the result in the main. Concrete rideabililty is very different using modern electronically controlled equipment and finishing to past concrete roads, which could be noisy as well as suffer poor wet weather skid resistance. Improved methods and technology have dealt with these issues.
The job now switches to the small team at the central depot, to keep the road open, clean, verges trimmed and free of snow or spillages. For the next 30 years.
A freshly renovated section of the A8 Autobahn in southern Germany will be watched with some interest this summer as traffic begins driving along its rebuilt carriageway and additional third lanes. That is not because of any special road features, other than a distinctive reddish colour to its concrete surface, but because it is a first full-scale public-private partnership scheme in the country and a possible harbinger of future development.
"Unlike many other European countries, Germany has not made much use of private sector investment in this way to date," said Gianluca Beraldo, technical director for Pansuevia, a joint venture finance and operating company that is overseeing the road upgrade and then maintenance and operation for the next 30 years. "But I think it is a good way to go."
The company, which uses the old Roman name for Bavaria, Suevia, is a special-purpose vehicle jointly set up by contractors
The A8 is one of the oldest of the original autobahn routes and dates back to the mid-1930s when it was one of several, then strategic, highways built as much for military movements as for civilian traffic. The first autobahns feature long straight sections with a secondary purpose in mind for temporary use by military aircraft. In places, the twin lanes of the A8 still featured the original robust concrete structure of the time, although overlaid with asphalt in recent years. The route forms the southern of two east-west transport corridors through to Munich, the other running from Frankfurt through Nuremburg and then south to the Bavarian capital.
"Most newbuild and renovation work for autobahns is done directly at the Federal Republic level (Bundesrepublik) but in recent years the country has been looking at the options for some private investment," said Beraldo. This has come about partly because Germany introduced a tolling system for freight transport back in 2005. The LKW Maut system, run by the Toll Collect consortium of
Charges are imposed on all trucks that are more than 12tonnes according to distance, the emission class of the truck and the number of axles, which affects the wear rate on road surfaces. A fairly controversial government decision in March this year means the system will also be applied to foreign cars travelling through Germany. It is also possible the truck weight threshold will be reduced to 7.5tonnes.
But whatever happens the toll system provided a basis for a number of road projects to be bid in recent years on a private finance basis, said Beraldo. Four or five experimental schemes have been tried to see how it would work out. "It did not work out exceptionally well," he explained.
This is because the payback for the projects was based on a percentage of the tolls. These were collected by the federal system and then handed over. "But the difficulty is that the payback can vary considerably if fleet transport operators upgrade their vehicles," said Beraldo.
Operators have every incentive to do this, because the emissions class component of the toll calculation and the axle numbers can significantly reduce the toll rate. "But because you cannot foresee the rate of fleet upgrades, it makes revenue streams difficult to assess and predict precisely, which is important for financing schemes." The state of the economy, especially after the 2008 world financial crisis, also had an effect, slowing down some operators' investment plans and reducing freight movements and tonnage on the roads.
As a result, Pansuevia's project is being done on a different basis using a shadow tolling arrangement simply calculated on highway traffic alone rather than the classes of vehicles. It is likely to be the only one like it, however, as subsequent projects are using a road availability as the basis for payments Beraldo said, with payments reduced when flows are reduced for maintenance.
"We also have penalties for lane use reductions but only for major road works" he added.
Pansuevia's project is in two parts, the reconstruction and widening work, which covers a section of the road more than 41km and the maintenance and operation contract for both that section and for an additional 16km of road towards Ulm, which will remain as original motorway. The maintenance work began immediately with the contract, which was finalised in June 2011 after a long period of negotiation and will continue over 30 years.
"The motorway is already an operating route and has to remain so throughout the reconstruction and rebuilding," explained Beraldo. Initially he said, the work was carried out from an old depot belonging to the client near the west end of the concession. But he added that immediately the project was let, a plot of land was bought in the middle of the section for the new operations and maintenance (O&M) centre, which then opened in May 2012.
Maintenance covers the full range of operations needed to keep a motorway going. This ranges from dealing with snow and ice in the winter, which can be relatively severe in this central European location, to trimming and cutting vegetation, cleaning the motorway and its structures and removing graffiti. All this work is done from the depot close to the halfway point, where snow ploughs, trucks, a salt store and a vehicle workshop are kept and that is also home to the control centre.
"We have a GPS-based management system for the project, to track vehicles and personnel locations and plans operations" said Beraldo. The control system works with a series of dashboards and maps to show work operations and accidents when they occur, and draws in local detailed weather information, too. It was worked up in conjunction with software house Novasib in Efurt from an original software used by Hochtief for winter salting works elsewhere. "We looked at some other solutions and were offered one by a Swiss company but they were all over-complex and expensive," he said.
Accidents are tackled by the local emergency services with Pansuevia providing traffic diversions and lane control. "One of the biggest problems is big lorries, which just veer off the road," said Beraldo, "and you do wonder sometimes if they are reading the paper or something."
The need for maintenance has very much informed the reconstruction work and the road carriageway design. The old two-lane highway has been covered in asphalt overlays for many years but will now be reverting to a concrete design according to Beraldo. The point is to reduce the need for resurfacing to a minimum over the maintenance period; asphalt would require resurfacing during the concession term whereas concrete does not. "That reduces the amount of lane possessions we will need, which cost money from the toll revenue because of reduced road availability."
There is some asphalt work being done he said, namely for the 16km of road near Ulm, which is not being rebuilt, but will need some work shortly. "But we decided to include resurfacing on this stretch to be able to start with a clean sheet as it were."
Work for the longer stretch was let to a three-firm consortium comprising Hochtief, which has 50%, Germany's Züblin, which is now owned by Strabag, and concreting specialist Heilit & Woerner. The contract, worth some €400 million, is primarily for remaking the road as a new three-lane dual carriageway and hard shoulder.
"The old alignment is not to modern standards for curves and gradients so those have to be improved and there are a number of bridges and culvert structures – some 79 bridges in fact," said Beraldo, "including three interchanges. There are 38 water retention basins and 8.5km of noise protection".
He added, "But there is nothing significant in terms of major structures. The biggest are actually 'green bridges' for animal passage." There are two of these, which are more like covered sections of the motorway, 50m long and with topsoil and vegetation above. Using motorway fencing they funnel animals in the surrounding forest to the crossing points to recreate natural links between the two sides of the autobahn.
Construction work on the road itself, which finishes this year, is in three phases, widening the sides, diverting traffic and rebuilding the central road, first on one side, and then the other. "We also did the construction in sections with breaks in between," said Beraldo. The outer carriageways can be built first but the central phase of the work involves diverting traffic on to one side of the motorway, once the new lanes are in place. Traffic is confined to one side in narrowed lanes. To avoid driver fatigue, and to let the traffic sort itself out, the reconstruction has breaks, allowing the full motorway to be used at intervals; these sections are then done themselves. The complicated logistics have been a key part of construction planning.
Work began with an earthmoving operation to widen the road, particularly at the end nearest to Ulm where it descends from the so-called Schwäbishche Alps, a picturesque hilly region, most of which is national parkland and forest. The road path had to be cut back for the third lane and in places provided with retaining walls.
But the main operation has been rebuilding the carriageway and widening it out. First the old material has to be broken out, at least in the four lanes of the old part, most of the old concrete being crushed and finding its way back into the road. Where possible it goes into the sub-base or, if unsuitable, into base material for underpasses.
Then comes a ground mixing operation to improve the basic ground capacity. A big
The 260,000m3 of lean mix has been supplied from its own batching plant at a works depot at approximately the halfway point along the project. A second larger batching plant makes the 360,000m3 of concrete for the main road structure here as well.
Above the bound layer is a geofabric, said Beraldo, before the two-layer concrete carriageway is laid above. "That allows the concrete to move freely when it expands and contracts," he explained.
The concrete road carriageway itself has two layers, the main part 240mm thick and a top riding layer of 50cm. These are laid simultaneously, 'wet on wet', using two full-width paving machines, separated by a 6m gap, said Beraldo. A small conveyor unit lifts concrete deliveries over the top of the first machine to the second. The construction JV has used Heilit & Woerner's own make of machines, which have proved excellent said Beraldo. They are capable of laying a full 15m width in one pass.
The sequence involves the first machine placing a main 240mm layer with reinforcement dowells inserted. There are also anchors installed for the longitudinal joints that run 5m apart. "The anchors are embedded whereas the dowels are sleeved to allow expansion movements," said Beraldo. "They are just to stop shear movements."
A top 50mm layer by the second machine uses a smaller and better aggregate he said, with a polish resistance to give skid resistance. Behind that comes a final bridge from which any flaws can be corrected manually and from which a top coating is applied. This is a sealing chemical for preventing drying during the initial cure and also has a retarder that holds back the hardening of about 3mm of the surface.
"Some hours later a steel brush is used to remove the matrix, leaving the aggregate protruding from the hardened concrete," explained Beraldo. "You need some experience to judge the right moment. But it slightly roughens the surface with small voids, which allow air to escape when it is compressed beneath the tyres, and that reduces noise by a few decibels."
A second follow-up operation, again time-critical depending on weather particularly, is cutting 100mm deep grooves to induce the natural shrinkage cracking during concrete curing to take place at just the required point for the joints. "It is almost magical how the concrete will crack at just the right point," he said.
Once hard enough the joints also have to be sealed against water ingress and the danger of water penetration, leading to frost-thaw damage deeper into the road structure. In previous times pitch was used to fill the gaps, but nowadays a plastic insert goes in. "They need replacing about once every 10 years," said Beraldo.
Concreting goes quite fast he said with 500m achieved/day during much of the work and to complete the schedule, day and night working producing 1km a day last year. The resultant carriageway has a slight pinkish tinge because the aggregate was imported from a source some distance away where the quarried rock is pinkish. This is because the local material is a limestone with a potential vulnerability to alkali-aggregate reaction, the so-called 'concrete cancer' that causes an expansion inside the concrete over many years and can crack and burst the concrete. The JV opted to use the pinkish limestone because it would avoid this risk.
Much of the concreting was finished by late spring this year with a few remaining stretches being completed and some structure to be done. Two early temporary bridges installed to keep traffic flowing during the works have to be replaced with permanent structures, for example.
Beraldo is pleased with the result in the main. Concrete rideabililty is very different using modern electronically controlled equipment and finishing to past concrete roads, which could be noisy as well as suffer poor wet weather skid resistance. Improved methods and technology have dealt with these issues.
The job now switches to the small team at the central depot, to keep the road open, clean, verges trimmed and free of snow or spillages. For the next 30 years.