Atlas Copco has completed the introduction of its fifth generation soil compactor range with the roll-out of the compact CA models. The new Dynapac CA1300 and CA1500 machines share features with the larger machines launched earlier this year, with a focus on reduced operating costs, low operating noise and fuel consumption and ease of servicing.
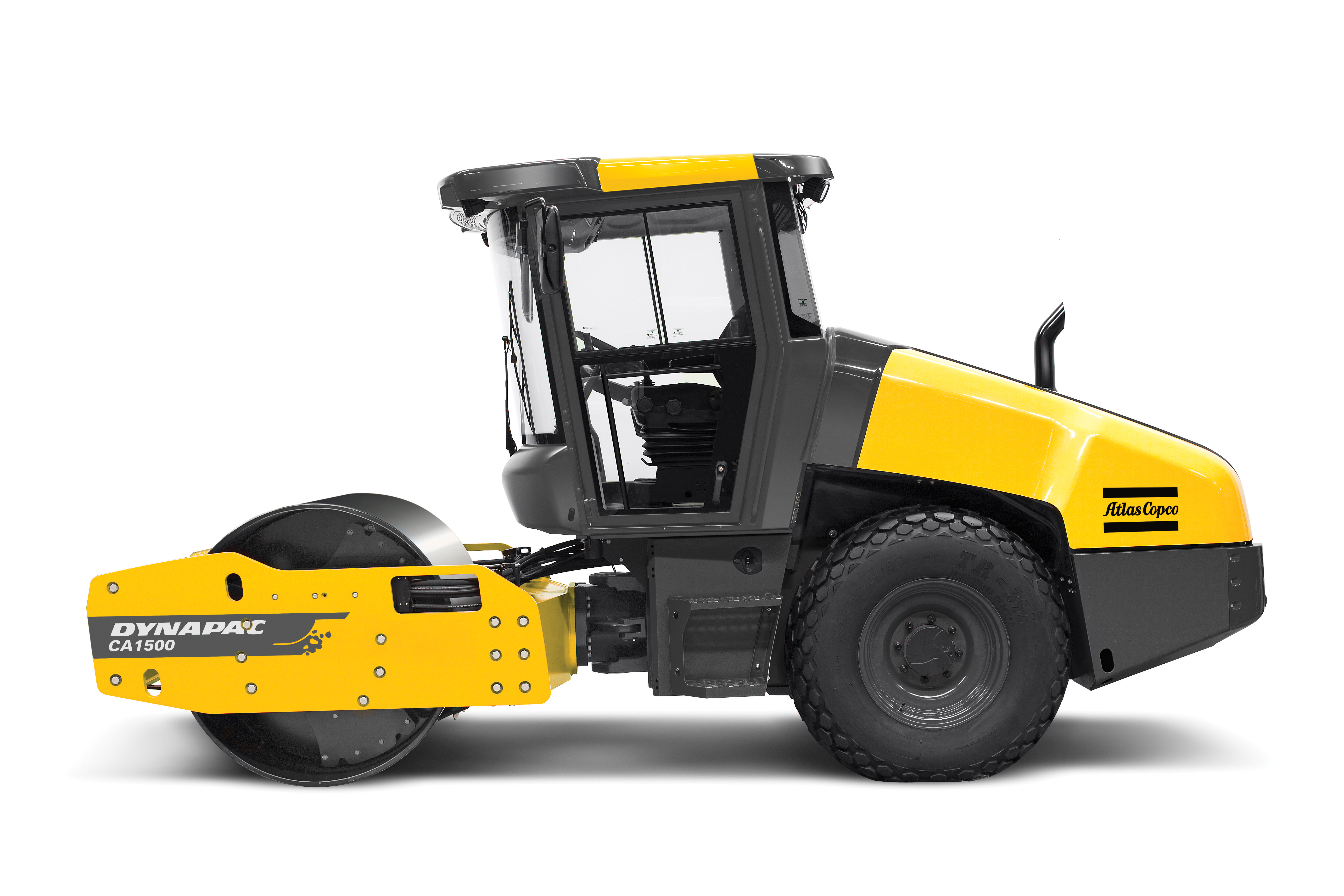
Atlas Copco says that customers for the new CA soil compactors can select from a wide range of options to suit the machines to an array of requirements
High performance is also claimed due to the sophisticated Active Bouncing Control system that prevents over-compaction and also minimises the risk of damage to the machine. Compaction performance is also aided by the optimised amplitude, which helps maximise productivity.
The CA1300 weighs 4.5tonnes in standard trim, features a drum width of 1.37m and is powered by a 55kW
The machines can be used to compact a range of materials, from sand and gravel to rockfill as well as silt and clay. Amplitudes of 1.8-2mm for the larger
This improved compaction depth allows a higher volume capacity and reduces the number of passes required to reach compaction specifications. This helps lower fuel consumption as well as the time required to carry out each job, reducing the cost/m3 of material compacted. The eccentric vibration concept is said to improve compaction performance further and is standard on Dynapac CA4000-CA6500 models. Advanced Controls boost raise productivity by allowing the user to control each job in three clear steps. A compaction job can be planned efficiently using the Dynapac CompBase software, while the Compaction Meter and analyser help ensure performance is monitored continuously and optimised. Analysis can be carried out of compaction work using the Dynapac Compaction Analyzer (DCA). Dynapac’s internet-based CostCtrl software and an extended warranty also help lower life cycle costs and maximise machine availability.
Other improvements include improved operator comfort, new safety functions and the choice of either Tier 3/Stage IIIA or Tier 4 Interim/Stage IIIB emissions compliant engines. This last is a key feature as it means the customer can select the most suitable engine package for the quality of fuel available as well as the local emissions regulations where the units will be operating. The transverse-mounted engines reduce machine length and optimise weight distribution. The diesels are said to be easy to access for maintenance and the engine cover is easy to open for quick maintenance while the hydraulic pumps are more readily accessible. A service interval alert in the instrumentation display shows when maintenance is needed and also shows what work is required.
The ECO fuel saving system reduces fuel consumption and CO2 emissions by ensuring that the roller does not consume more power than needed at any time. Combined with other improvements, this has helped deliver a significant fuel saving overall compared with the firm’s previous generation machines. Noise levels are low as cooling air comes in through the top of the hood while the outlets are at the sides, combined with the ejector exhaust outlet. This ensures the inlet air is as clean as possible. Meanwhile thick drum shells on the Dynapac CA rollers extends the wear life before drum changes are required. And a scraper blade with a novel divided design keeps the drum free of material during operation and can be replaced quickly and at low cost if necessary.
Large ergonomic cabs with air-conditioning and lower noise are said to provide greater operator comfort and lower fatigue through the working day. The new spin-around Seat, steering module and display cluster allows 180° movement and further improves all-round visibility for the operator. Safety features include Electronic Drive Control with a function that reduces braking distances if the lever is moved fast, and a tilt indicator. Loss of traction is reduced by the efficient gear shifting system or with an optional anti-spin package, even in tough conditions.
A wide range of models and options are offered including a bolt-on pad Shell for PD applications, different scrapers and lights for night working. Another option is a speed limiter that prevents compacting at too high a speed, using an electronic drive control and automatic vibration control.