Manufacturers continue to innovate with sophisticated new soil compaction machines - Mike Woof reports This year has seen the introduction of a series of new soil compaction machines, as manufacturers develop their product ranges. Meeting emission legislation requirements in Europe and North America has helped drive firms to install the latest engine designs. Meanwhile machines have also evolved as companies further refine operating features.
The global market for compaction machines has been dominated by
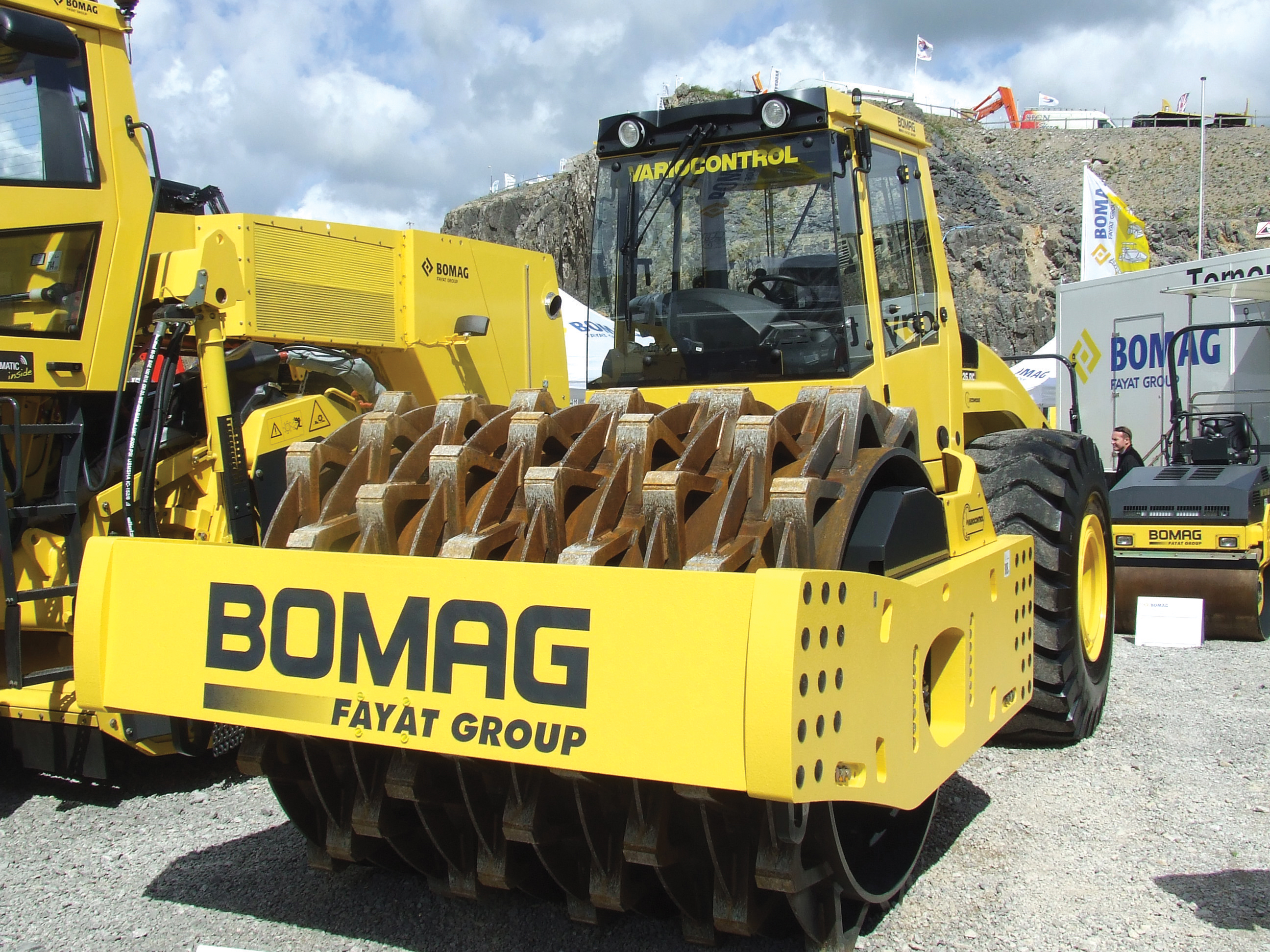
The novel BOMAG rock crushing drum can be used for in-situ crushing on road projects
Manufacturers continue to innovate with sophisticated new soil compaction machines - Mike Woof reports
This year has seen the introduction of a series of new soil compaction machines, as manufacturers develop their product ranges. Meeting emission legislation requirements in Europe and North America has helped drive firms to install the latest engine designs. Meanwhile machines have also evolved as companies further refine operating features.The global market for compaction machines has been dominated by a comparatively small number of European and US manufacturers for many years, including
However, a notable development has been the entry of Chinese firms to this business. For the most part the latest Chinese firms compete in market segments where emissions compliance is limited to earlier standards. But it can only be a matter of time before emissions compliant Chinese machines become widely available in Europe and North Americas. Compaction control systems and GPS technology is becoming more widely available in the soil compaction market, offering major benefits to productivity and consistency for clients, contractors and fleet owners alike.
But other developments are also coming to market that help widen the sphere in which soil compactors can operate, due to innovative modification packages.
From Amman come the new ASC 110 and 150 ACE Pro single drum rollers, which are powered by
These machines feature operating weights of 11.26tonnes and 15.21tonnes respectively and come with the firm’s latest intelligent compaction technology. The company claims its sophisticated continuous compaction control (CCC) offers consistent performance on-site. The rollers deliver frequency ranges of 27–35Hz and 27–36Hz respectively, while static line loads are 34.5kg/cm for the 110 model and 51.2kg/cm for the heavier 150. An optional GPS tool is available for the ACE Pro system, which allows it to display compaction progress in real-time and provide on-line documentation for the user. The system ensures full documentation of work, as well as providing the operator with guidance as to levels of compaction carried out. Using the ACE Pro system with GPS location data feeds compaction data values back into the roller. The machine can automatically adjust amplitude and frequency to achieve the target compaction rate and stop compacting when the correct level is reached.
An innovation from BOMAG is a development of its 26.4tonne BW226 roller, which is now offered with a novel rock crushing drum. The machine is powered by the same 150kW
Les Wrighton of BOMAG GB explained, “The vibration system is based on our VarioControl. You set the angle of the weights to maximum on the operator panel and then drive forward and that crushes the rock. I’ve seen it breaking rock sizes of 400-500mm down to about 200mm and smaller in some instances and with a low percentage of fines.”
He explained, “You can’t just lay out the rock you want to break onto soft ground or the roller will just punch the rock into the dirt. You need to pre-compact the area. But you can’t lay out rock on concrete as there’s too much reflected vibration and you get bounce-back.”
However he added, “It is unusual and it is a niche market.” Customers can buy the BW226 with either the standard smooth or padfoot drums, the firm’s polygonal drum or the rock drum, as well as with any combination of those four. Apart from the drum, the only difference between the standard BW226 and the rock crushing version is with the tyre selection, which has to match the more aggressive underfoot conditions.
Caterpillar is pushing hard to boost its share of the compaction market with a range of new machines that share common features in the shape of its B-series CS and CP single drum models. The CS68B and CS78B are smooth drum machines while the CP68B and CP78B are equipped with padfoot drums. All four share features such as the new high comfort, high visibility, climate-controlled cab and the CS68B and CP68B compete in the 14tonne class while the larger CS78B and CP78B are 17tonne class compactors.
High productivity is claimed due to the combination of proven vibration excitors, greater weight at the drums and optimised amplitude, according to Caterpillar. Dual pump propel systems provide traction and gradeability while automatic speed control and automatic vibration deliver consistent compaction. Power comes from the firm’s own Tier 4 Interim/Stage IIIB compliant engines that offer fuel economy and running costs are further reduced due to extended hydraulic service intervals of three years/3,000 hours.
The machines can all be equipped with a sophisticated compaction control system as well as two different compaction measurement packages. These can be fitted in the factory, along with SBAS or RTK GNSS mapping capabilities linked to an operator display.
The Compaction Meter Value (CMV) system is an accelerometer-based tool for use on smooth drum machines in granular soils. This package measures 1-1.2m into the ground and can identify buried objects such as rocks as well areas of insufficient compaction. Meanwhile the Machine Drive Power (MDP) package shows soil stiffness by measuring rolling resistance. This system is offered on the firm’s smooth drum rollers, padfoot machines and also smooth drum units with shell kits fitted. A versatile package, it can be used whether the drum is vibrating or not and on all soil types, while it measures to depths of 300-600mm.
According to Dynapac, its new fifth generation CA single drum vibratory rollers offer performance upgrades over rival machines. The CA5000, CA6000 and CA6500 feature transverse-mounted engines that improve serviceability and help boost utilisation and reduce downtime. Optimised amplitude is said to boost compaction performance while a novel Active Bouncing Control reduces the risk of damage, as well over-compaction. High comfort cabs, good manoeuvrability and reduced noise levels and fuel consumption also help to make these machines easier to operate for longer periods, while reducing running costs.
The three new CA rollers have provide linear loads of 50, 60 and 65kg/cm, respectively. High amplitude of 2.1mm enables rockfill to be compacted in almost 2m thick layers and the rock size can be up to 1m in diameter. Higher volume capacity is claimed along with and fewer passes to reach compaction specifications. This further saves on fuel and reduces the cost per compacted/m3.
The sophisticated process control boosts productivity and the firm offers Dynapac CompBase software for planning. A compaction meter and analyser on the roller allow work to be monitored, while results can be evaluated using the Dynapac Compaction Analyser (DCA). Dynapac’s CostCtrl software on the web and an extended warranty for CA rollers allow customers monitor life-cycle costs and maximise machine availability. The new CA rollers are available with Stage 4 Interim/Tier IIIB Deutz diesels. A system minimises fuel consumption and CO2 emissions. This combines with higher compaction parameters to deliver major fuel savings over earlier models. In addition, the machines can be used with a mix of biodiesel and fossil diesel fuel; some can be run on 20% biodiesel.
The new cabs operator comfort and good visibility. A spin-around seat and steering module allows movement of up to 180°. Short machine length and good turning radii, make manoeuvring easier in difficult conditions. The automatic bouncing control prevents damage by eliminating drum double jump, or over-compaction. The CA6000D also features a speed limiter to avoid compacting at too high speed. A service interval alert in the instrumentation display indicates when service is required and what action to take. The new CA rollers are available in standard models with a long list of different specifications and an extensive choice of optional extras.
With the market launch of the Hamm H series, there are now five compactors including the H18i, H18iP, H20i, H20iP and H25i. Full production versions are now available and these have operating weights of 18, 20 and 25 tonnes. The range does feature improvements over the prototype unveiled last year but retain much of the novel cooling package configuration for the Tier 4 Interim compliant engines. The layout of the cooling system is said to provide good rearward view, while frame construction gives an unobstructed view of the surface to be compacted. The cab is also said to be ergonomically designed to reduce fatigue and help boost productivity.
Chinese firm