Productive performers provide increased output for customers in the loading and hauling sector of the earthmoving market - Mike Woof writes. Loading and hauling machines play key roles in earthmoving operations, with the excavator and ADT combination proving both versatile and productive. While machines such as scrapers may be more efficient in specific earthmoving applications, these do not offer the versatility of the excavator and ADT combination, reducing utilisation.
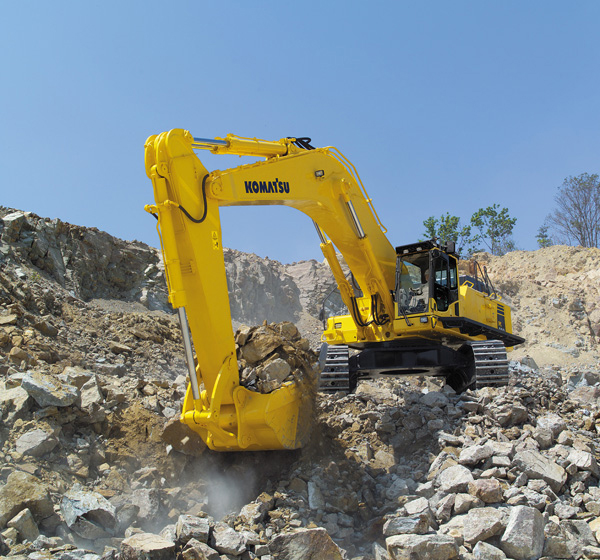
The new Komatsu PC800-8 and PC800-8 LC excavator variants offer low emissions and high performance
Productive performers provide increased output for customers in the loading and hauling sector of the earthmoving market - Mike Woof writes
Loading and hauling machines play key roles in earthmoving operations, with the excavator and ADT combination proving both versatile and productive.While machines such as scrapers may be more efficient in specific earthmoving applications, these do not offer the versatility of the excavator and ADT combination, reducing utilisation. The focus for many manufacturers has been on boosting performance both of ADTs and excavators, with an array of new models coming to market during this year.
New model improvements focus particularly on the instroduction of Tier 4 Interim/Stage IIIB emission compliant engines, with novel cooling systems tailored to ensure that forward visibilty is maximised due to the use of sloping engine covers.
In the ADT sector
Most recent of all is Komatsu's HM300-3 ADT, which is powered by a Komatsu SAA6D125E-6 emissions compliant diesel rated at 242 kW. The engine has been developed from the proven Tier 3/Stage IIIA platform and is said to offer more power and lower fuel consumption, as well as meeting the tough emissions requirements. The HM300-3 is said to be highly competitive and features a gross vehicle weight of 52.2tonnes and has a payload of 28.1tonnes. Maximum speed is 58.6 km/h and the truck benefits from a redesigned traction control system that boosts operating efficiency in tough conditions. The truck also has the latest version of the six-speed Komatsu advanced transmission with optimum modulation control system (K-ATOMiCS). This fully automatic transmission uses electronics to eliminate shift shock and torque cut-off, improving efficiency. The system selects the optimum gear ratio dependant on travel speed, engine rpm and the shift position chosen, boosting acceleration, allowing smoother down-shifting and better matching engine speed when climbing slopes. The new Komatsu traction control system (K-TCS) is said to provide optimum traction when operating in soft ground conditions. In poor ground conditions any tyre slippage is detected by speed sensors located on four wheels and the inter-axle differential lock is applied automatically.
Should this prove insufficient to deal with the issue then the brakes can operate automatically and independently to prevent tyre slippage. An automatic retarder system allows the operator to select the optimum operating speed on downhill travel under full load.
The truck also has a new cabin layout, making it more comfortable to drive for a full working shift. A high resolution LCD monitor displays information in 25 languages and allows the operator to modify settings for items such as the auto-idle shutdown or the auto-reversing fan. A separate reversing camera is standard with every machine, to boost safety when backing up for tipping. The truck comes with the KOMTRAX package allowing fleet operators to monitor performance and machine health remotely, while the new ADT has also been designed for ease of maintenance. As a result, unning costs are said to be lower than for the model its replaces.
The excavator market has been equally awash with new Tier 4 Interim/Stage IIIB compliant machines during this year. Firms including
The latest of these is the upgraded Komatsu 80tonne class offering, which is available in the PC800-8/PC800LC-8 variants. These models are developed from proven designs and feature increased productivity and safety. The Tier 4 Interim/Stage IIIB emission compliant Komatsu SAA6D140E-5 engine is rated 370kW and is fitted with cooled exhaust gas recirculation (EGR). Low external noise levels are achieved by using a hybrid blade variable speed cooling fan.
Depending on specification, the machines have operating weights of 78.8-84.7 tonnes, while buckets with capacities of up to 6.9m3 can be fitted, dependant on factors such as boom and arm length, material density, and application conditions. The variants both have two power and economy working modes, which match engine speed, pump flow and system pressure to the working application. The economy mode has four level settings, allowing the operator to achieve required production with the lowest possible fuel consumption.
Meanwhile the heavy lift mode gives the operator 10% more lifting force on the boom when needed to handle large rocks. The one-touch power max function temporarily increases digging force by almost 10%.
As with other machines in the firm's range, the excavators come with Komatsu's KOMTRAX technology providing daily machine data updates to the owner wirelessly through a secure website.
All data is relayed to the Internet application for analysis. In addition, the firm's equipment management monitoring system (EMMS) is fitted and is said to to reduce downtime. This package monitors critical systems, alerting and guiding the operator should a problem occur.