A tricky utility supply project has been carried out in difficult conditions in Germany, without disturbing a village access road. The drilling work for the project was operated by boring contractor Beermann and the site was located on a plateau some 5km from the nearest village.
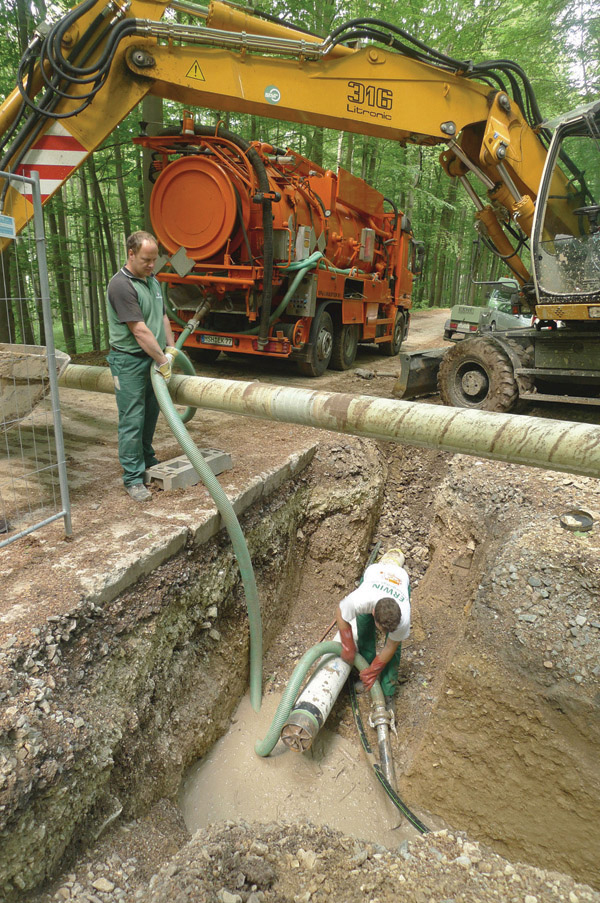
Using a powerful rig from Tracto- Technik, German contractor Beermann has managed to complete a steeply sloping utility installation under a village access road
A tricky utility supply project has been carried out in difficult conditions in Germany, without disturbing a village access road. The drilling work for the project was operated by boring contractor Beermann and the site was located on a plateau some 5km from the nearest village.
The forest lane leading to the working area was only accessible with 4-wheeldrive vehicles over its final 300m and it took one working day to setup the equipment at the jobsite. Water to mix the drilling fluid for the bore was extracted from the Wipper River some 6km away and was transported to the jobsite in 10m³ tanks hauled by tractors. The work was needed to replace an old gas pipe over a 2km length to the town of Sollstedt and the HDD rig chosen to install the new bore was a Type 25N Grundodrill built byThe distance between the HDD rig and the start of the steep slope was approximately 70m and this made an entrance angle of about 42% necessary to be able to meet the planned bore exit point at the foot of the steep slope. In comparison to most projects where the bore entrance angle is usually at 10-24%, the bore angle was very acute and required careful working.
The ground conditions on the bore path comprised layers of weathered and very solid limestone and the pilot bore had to take into account these ground conditions. An aggressive boring head with special hard metal bore tips was used while a depth sonde from specialist DCI was fitted for the monitoring and steering. The cover on the steep slope was almost 25m deep in parts, which resulted in the signal being marginal at times. However, the signal got stronger after the critical phase of the bore confirming that the contractor was on course and the pilot bore was completed on target. Two pilot bore expansion bores, with 250mm and 350mm diameter reamers, followed with the runs taking just 5 minutes per drill rod length to pull through. The drilling fluid was collected at the target point and passed on to a second deeper pit at the access road and then disposed of by a suction/vacuum transporter. After each expansion bore the backreamer was pushed back through the bore hole in order to compress and rinse out the bore spoils to prevent the product pipe getting stuck when it was finally pulled in. After the final cleaning process the bore was cleaned thoroughly and made ready for installing of the product pipe.
Some 12 steel 200mm diameter pipes with a PE and reinforced fibre glass coating were welded together, x-rayed and checked for tightness with water at 100bars. Then the PE and reinforced fibre glass coating was reinstated at the welding point. Installed along with the gas pipe were four HDPE pipes of 50mm diameter and 4.6mm wall thickness which were pulled in to host the control cable and also for the filling of the annular space.
A Bagela cable winch pulled the pipe string uphill to the bore hole and the pipe installation process began as soon as the final backreamer had been connected. The weight of the pipe string was calculated to be 5.7tonnes, while the tensile load was an average of 9tonnes and well below the rig's reserve load of 25tonnes. From the bore exit point, the pipeline installation used the open trench method and a milling cutter had already excavated a 1.3m deep trench.