Vital repairs to a drinking water transport pipeline in Norway included the first ever use in the country of trenchless water pipe bursting to fix damaged cast-iron pipes. Leaks caused by corrosion had become commonplace over 900m of the 40-year-old ND 600 cast iron-made pipeline in Trondheim. Due to the pipeline running 3m below a busy street and in front of a kindergarten and school, contracted civil engineering firm Sandum decided to replace the pipeline using a trenchless pipe bursting method rather tha
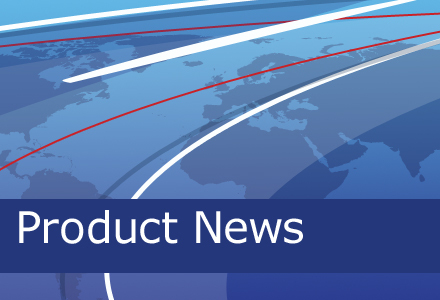
Vital repairs to a drinking water transport pipeline in Norway included the first ever use in the country of trenchless water pipe bursting to fix damaged cast-iron pipes.
Leaks caused by corrosion had become commonplace over 900m of the 40-year-old ND 600 cast iron-made pipeline in Trondheim. Due to the pipeline running 3m below a busy street and in front of a kindergarten and school, contracted civil engineering firm5917 Sandum AS decided to replace the pipeline using a trenchless pipe bursting method rather than an open trenching method. The move also saved construction time and reduced costs by 30%.
During the four-month pipeline repair project, it was crucial to maintain its cross section. Corrosive soil conditions led to HD-PE pipe OD 710 x 52.2mm (with coating) being chosen as the new pipe.
As an active member of the Scandinavian Society for Trenchless Technology (SSTT) Trondheim residents and businesses are familiar with trenchless installations and replacement methods and were keen to promote the use of these techniques with the repair works.
Sandum said the diameter of the drinking water pipe was a particular challenge, requiring accurate planning in close cooperation with the engineering office5918 Asplan Viak AS and machine manufacturer 2738 Tracto-Technik. Eco-friendly Bentonite was used to lubricate the pipe string, which significantly reduced the casing friction to make pipe pulling easier.
The pipe bursting started with a test section, with an option to continue the project. The Grundoburst 2500G with 250tonnes pulling force and a special roller blade for cutting the ductile cast iron pipe was deployed. An upsizing head of 830mm was used to displace the split old pipe into the surrounding soil.
After a successful test, the 900m of pipe requiring repairs was divided into seven sections, with the shortest being 120m and the longest being 170m long. The single 18m long segments of the PE pipe OD 710, PE 100, SDR 13.6 were welded together to form a complete pipe length for the respective section, pressure tested and securely connected using a pulling head.
The roller blade and expander head were attached to the bursting rods, which had been pushed through the old pipe in advance. When being pulled back the old pipe was cut and the new pipe pulled into the expanded void using Bentonite to reduce simultaneous casing friction. The tensile load affecting the new pipe was constantly monitored and logged with the Grundolog measuring device. An average tensile load of 500kN was measured, way below the legal limit.
Leaks caused by corrosion had become commonplace over 900m of the 40-year-old ND 600 cast iron-made pipeline in Trondheim. Due to the pipeline running 3m below a busy street and in front of a kindergarten and school, contracted civil engineering firm
During the four-month pipeline repair project, it was crucial to maintain its cross section. Corrosive soil conditions led to HD-PE pipe OD 710 x 52.2mm (with coating) being chosen as the new pipe.
As an active member of the Scandinavian Society for Trenchless Technology (SSTT) Trondheim residents and businesses are familiar with trenchless installations and replacement methods and were keen to promote the use of these techniques with the repair works.
Sandum said the diameter of the drinking water pipe was a particular challenge, requiring accurate planning in close cooperation with the engineering office
The pipe bursting started with a test section, with an option to continue the project. The Grundoburst 2500G with 250tonnes pulling force and a special roller blade for cutting the ductile cast iron pipe was deployed. An upsizing head of 830mm was used to displace the split old pipe into the surrounding soil.
After a successful test, the 900m of pipe requiring repairs was divided into seven sections, with the shortest being 120m and the longest being 170m long. The single 18m long segments of the PE pipe OD 710, PE 100, SDR 13.6 were welded together to form a complete pipe length for the respective section, pressure tested and securely connected using a pulling head.
The roller blade and expander head were attached to the bursting rods, which had been pushed through the old pipe in advance. When being pulled back the old pipe was cut and the new pipe pulled into the expanded void using Bentonite to reduce simultaneous casing friction. The tensile load affecting the new pipe was constantly monitored and logged with the Grundolog measuring device. An average tensile load of 500kN was measured, way below the legal limit.