Volvo Construction Equipment says that its all-new F-Series ADTs will meet the tough Tier 4 Interim/Stage IIIB emissions legislation as well as delivering performance improvements over previous models.
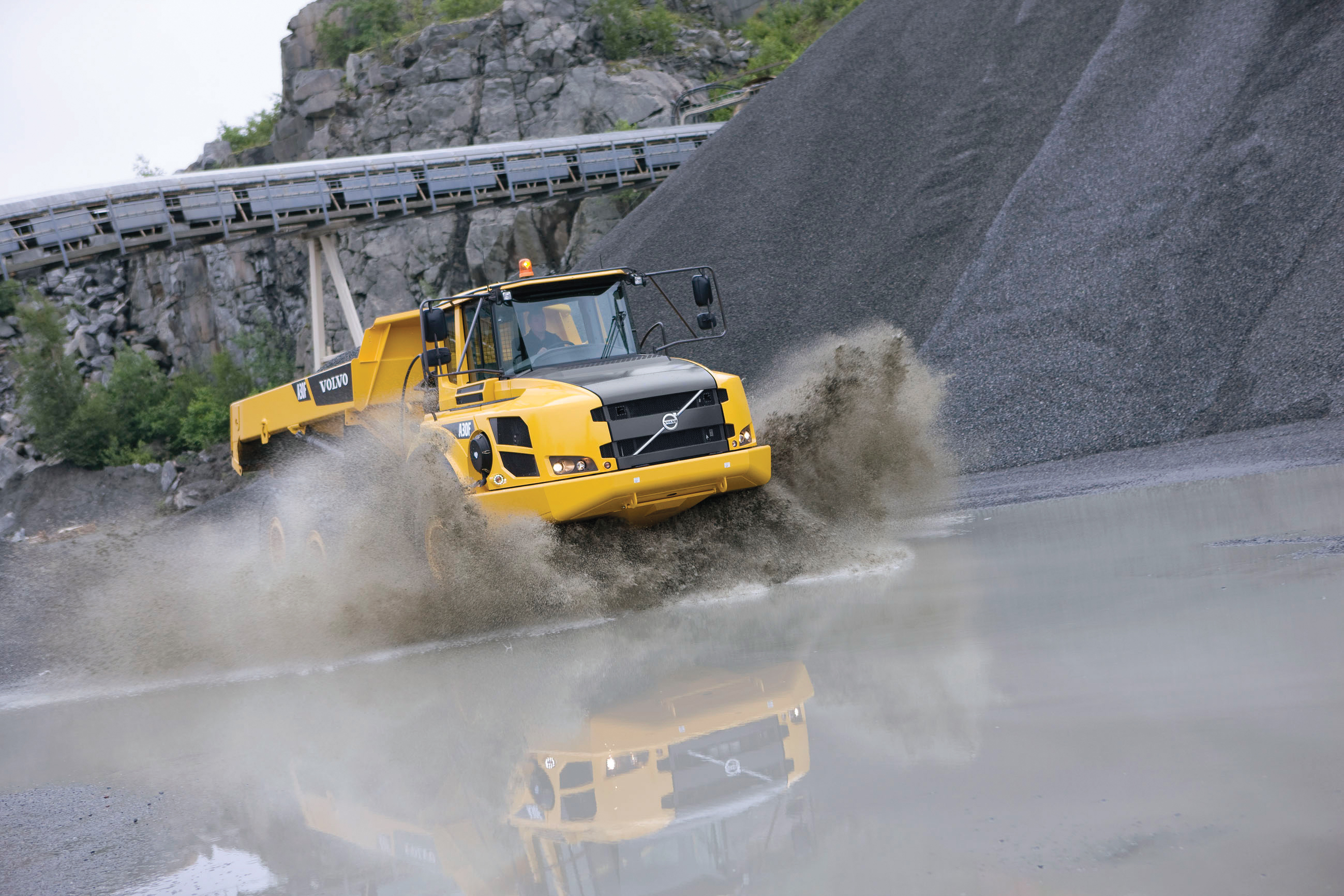
Volvo's New F-Series ADTs offer high operator comfort, improved fuel efficiency and ease of operation
There are six models in the line-up, with the most compact being the 24tonne capacity A25F while the top of the range model is the 39tonne payload A40F. Key design criteria for Volvo during development were ensuring high manoeuvrability, cycle speed and dumping capabilities, as well as safety, efficiency and reliability. Major improvements have also been made to operator comfort, ease of operation and fuel efficiency. These versatile and productive machines are said to suit a range of applications such as aggregate production, infrastructure construction, demolition and road building.
The truck feature Volvo's proven articulated steering system, with heavy duty front and rear chassis structures to cope with tough off-road duty cycles. The long life dump body is made from HB400 steel that features high dump clearance and tipping angle to minimise material retention when dumping. Closed-centre hydraulics are fitted, allowing for shorter cycle times and safer operation.
Power comes from Stage IIIB compliant Volvo V-ACT diesel engines with diesel particulate filter (DPF) after-treatment. Engine characteristics include high torque at low revs, delivering up to 4% gains in fuel efficiency over the earlier E-Series, helping to cut running and operating costs for customers. In addition Volvo's automatic traction control (ATC) is now a standard feature on the F-Series, having previously been a customer option available on the earlier E-Series. Other engine improvements include fast response and low wear, which will boost service life. The drivetrain is said to deliver optimum use of power and torque, even in tough working conditions and shafts, planetary gears and bearings have all been reinforced to cope. The sophisticated ATC system, switch to 6x4 drive when operating on good or paved roads and helps reduce tyre and drivetrain wear and fuel consumption. The three-point bogie beam design allows the rear wheels to move independently, ensuring good ground contact, traction and stability while minimising chassis stress loads.
Operator safety and comfort is maximised due to the fitting of the low noise Volvo care cab with both roll over protection (ROPS) and falling object protection (FOPS). Visibility is said to be good from the centrally positioned operator station, with a sloping engine cover, large rear-view mirrors, a wide front windshield and a full length glass door.
Hybrid answer
Following the success of
Komatsu's plan is to make the HB205 and HB215LC hybrid hydraulic excavators available in Japan, North America, China, Latin America, Southeast Asia, and Europe. Starting in 2008 Komatsu introduced its PC200-8 EO Hybrid, the world's first commercially available hybrid hydraulic excavator. Over 650 units of this earlier hybrid machine are in operation around the world.
The improved HB205 and HB215LC models benefit from experience gained with the PC200-8 EO Hybrid, with fine-tuned hydraulics and electronics to optimise overall performance. The new models deliver further reductions in fuel consumption as well as NOx and CO2 emissions. Komatsu has also made the HB205 and HB215LC easier to maintain, which should reduce downtime and running costs. As an option, the new models also come with hydraulics allowing the use of different attachments for a range of operating conditions.
The company says it is increasing production capacity for the hybrid hydraulic excavators in anticipation of expected demand and also intends to introduce hybrid technologies to larger excavator models and other construction machines in its range.