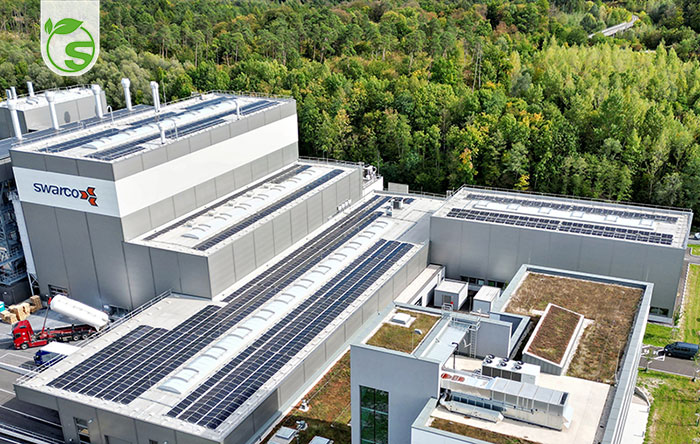
SWARCO Road Marking Systems says that its next generation SOLIDPLUS premium reflective glass beads combine greater road safety as well as being sustainably produced.
Ongoing improvements in the production process allow for an efficient and responsible use of resources and reduces the environmental impact. New data analysis software now helps leverage additional potential to make production even more sustainable.
Thanks to their excellent retroreflection, these premium reflective glass beads enhance the visibility of road markings in difficult conditions and make roads safer. They are the result of many years of continuing research and development at SWARCO Road Marking Systems’ Center of Competence for Glass Technology and Marking Systems.
Modern driver assistance systems depend on clearly visible road markings. Dark and wet conditions, as well as headlight glare from oncoming traffic continue to represent challenging situations. They require clearly detectable marking systems that can be recognised by vehicle sensors even in adverse conditions. This is of great importance for the development of advanced driver assistance systems and automated vehicles. The better road markings are detected by cameras and LiDAR sensors, the safer road transport is for humans and machines.
Meanwhile, SWARCO says that SOLIDPLUS has always been produced in the most environmentally responsible ways. Since last year, “the next generation of glass beads” has been made in one of the most state-of-the-art and efficient facilities for the production of reflective glass beads, explains Friedrich Wiesinger, head SWARCO’s Center of Competence. One hundred per cent of the electricity needed comes from renewable energy sources and some of it from photovoltaic panels on the roof of the production plant.
More is to come, he says. “We have set ourselves very ambitious goals in order to make our products even more eco-friendly. With our research on new glass formulations based on natural raw materials, we aim to produce the most sustainable reflective glass beads in the world.”
New special data analysis software is now being used to help achieve these goals by thoroughly examining the emissions in supply chains and all production processes as well as the product life cycle. This even makes it possible to precisely determine the ecological footprint of individual products such as SWARCO SOLIDPLUS.
The data collected helps the Center of Competence to carry out highly targeted research. For instance, the software identifies which raw materials leave a particularly high carbon footprint. Subsequently, they are replaced with more eco-friendly resources where possible.
“Our product development team conducts research on how to switch from environmentally harmful materials to alternatives with the smallest possible ecological footprint,” says Wiesinger. “This helps reduce emissions, waste and transport over large distances and achieve an effective circular economy. These are concrete plans to make the production of SWARCO SOLIDPLUS even more sustainable in the long term.”