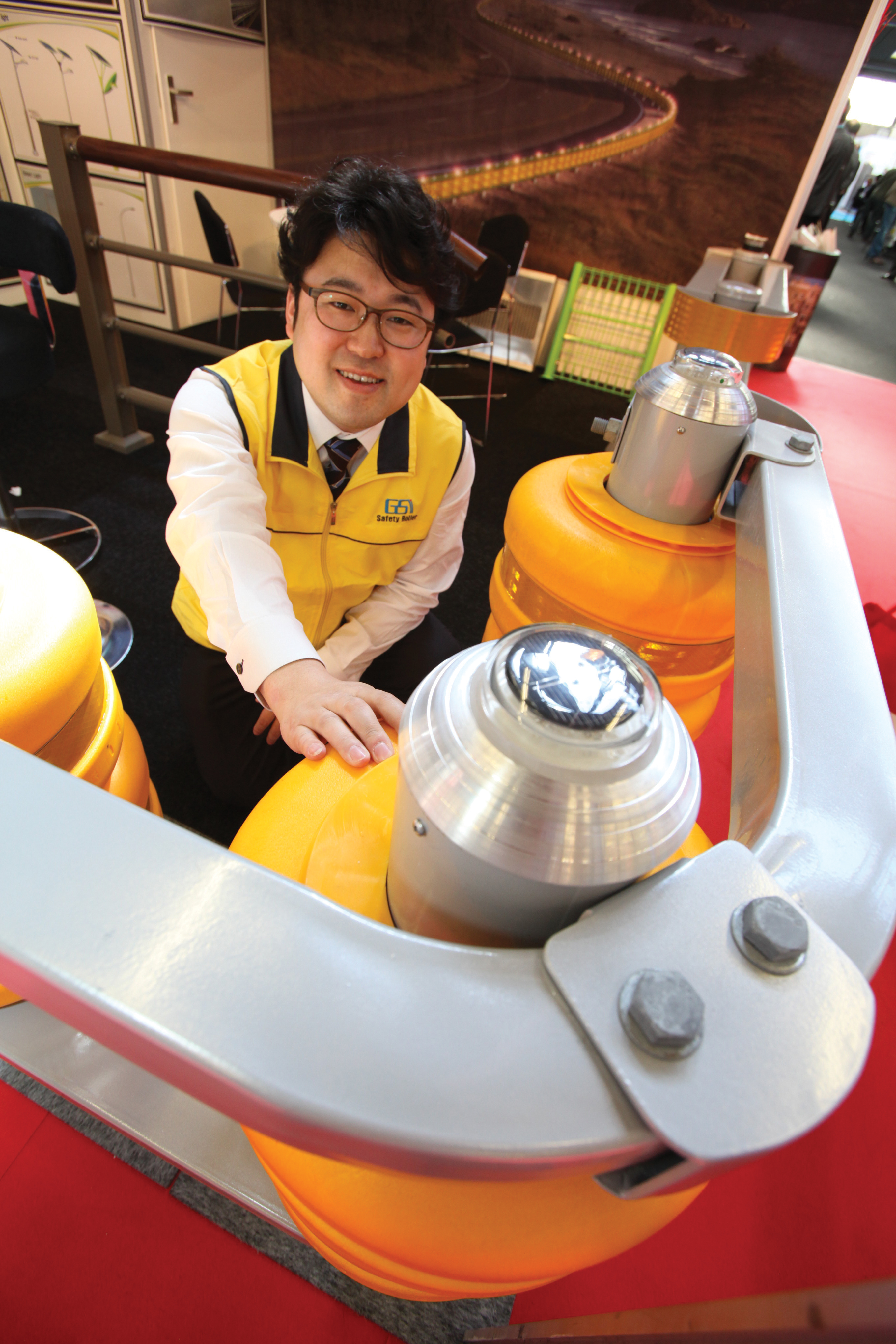
Protecting road users, with barriers, crash cushions or access control systems, is crucial for network safety - Mike Woof writes
Tough regulations are now in place in Europe and the US, requiring road authorities to provide safer road infrastructure than in the past. Technologies to reduce the severity of vehicle impacts against obstructions or redirect vehicles into the roadway should help cut injuries amongst drivers and passengers alike.The specifications for the use of crash cushions and barriers can vary considerably, while different systems can be used to suit specific applications. To explain the tools available for the US market, the
The information will allow road authorities in the US, or other countries using US standards such as those in Latin America, to achieve proper classification of crash cushions. This task is critical to ensure the appropriate placement of crash cushions as at present, few Departments of Transportation (DOTs) have in-house expertise on crash cushions. According to the IRF, not enough DOTs realise the importance of specifying crash cushions for on-site conditions, design performance specifications and reusability after a design capacity impact, to ensure the optimum usage of available road safety funds.
By following the IRF’s webinar, DOTs, road agencies, contractors and other road industry professionals were given information on to select the proper system for all applications. This data is crucial as it can provide significant savings when purchasing and maintaining crash cushions. This webinar also provided the details needed to implement crash cushion classifications for their state, agency or country, while explaining how each type of crash cushion works. Targeted participants included road agencies, US DOTs, consultants, academia, contractors, and asset management and other road industry professionals. Topics covered included: specific site data information required to select the appropriate crash cushion; a detailed comprehension of NCHRP 350 and MASH testing criteria; an explanation of an objective method to classify crash cushions based on life cycle costs; a recommended process to develop classifications based on site specific information, crash cushion performance; life cycle cost.
In the highway safety barrier sector, an array of innovative roadside technologies has come to market in recent months. Some of these meet European regulations, while others suit US standards and there are also novel technologies coming to market from various Asia-based suppliers. Some of the Asian products meet European standards already, or will soon, boosting competition in the sector.
The Taiwanese firm Aplus Molds and Plastics (AMP) has developed polycarbonate and polypropylene barrier sections to suit an array of protective requirements. The firm says that its polypropylene sections are lighter and cheaper than comparable steel components and suit duties on roads with low traffic volumes and speeds. Meanwhile the company’s polycarbonate sections offer greater impact performance and suit guardrail applications on highways. Weighing just 17kg apiece, the polycarbonate sections are lightweight and easy to handle, allowing them to be installed manually and without the need for lifting equipment. The light weight also helps reduce transport costs in comparison with conventional steel units, allowing more sections to be carried on each delivery vehicle and cutting freight charges.
The products are injection molded rather than extruded, which is said to maximise structural strength, while the barrier sections are said to be long lasting due to good UV resistance and are also corrosion-free. Impact performance is also said to be good as the material helps absorb shock, while a minimum working life of 10 years is claimed and the barrier sections can also be recycled. Various colours are available to boost conspicuity, while lighting can be fitted if required to boost visibility or provide hazard warnings. The sections also come with integral reflectors, which are colour coded. These boost safety by reflecting red light should a driver be travelling in the wrong direction.
The products comply with Taiwan’s requirements for vehicle redirective capabilities and impact performance and have also been supplied into China, the Philippines and South Africa. The polycarbonate sections can withstand the impact of a 3.8tonne vehicle striking at angles from 15°-25° and at speeds of up to 100km/h. The firm says it is at present looking for a European distribution partner and will then address the issue of obtaining EN1317 safety ratings. The components are also said by AMP to be free from stress cracking problems, as well as being electrical insulators.
In standard applications, the barrier sections are fitted to round steel posts installed at 2m intervals. The ductility of the units is also said to allow them to be bent to fit on curves without the need for special modification and also without losing structural performance.
Turkish barrier supplier Çepaş intends to increase its product range in due course. The new products are being tested to the European EN1317 standards at present and will be launched on the market once the testing is complete. The company said that its sales are currently strong, with orders in an array of key territories including the home market.
And also from Asia, South Korean company
This move will benefit GSI, as well as other South Korean suppliers, and GSI is hoping to commence testing to EN137 standards shortly, which will then allow it to sell its products in Europe. In addition the firm has also developed a light duty barrier designed for use in separating cycle lanes or motorcycle lanes from pedestrian walkways, as well as a centrelane barrier without rollers.
However, European firms are also offering new technologies or looking to develop sales in new markets. Spanish barrier specialist Industrias Duero hopes to see further sales into Latin America following expected changes in regulations in some key countries.
The authorities in Colombia and Uruguay are at present discussing the adoption of barrier standards for use on the respective road networks of these countries. At present it looks as if the two countries will allow barrier products that meet either US or European safety standards to be used in the country and should this ruling go forward,
Italian firm
Also from Italy is the barrier installation machine supplier
Access control
Auckland’s Victoria Park Tunnel project provides a major infrastructure improvement, linking the city’s harbour bridge to the central motorway. At the heart of the project is an additional on-ramp built to increase the accessibility of the northbound highway lanes directly from urban downtown streets. This additional access is only available during peak hours when a movable barrier is shifted out, which meant that the entry point of that on-ramp needed to be opened and closed on a daily basis. To allow this operation the unique SwiftGate automated lane closure system was installed.
The SwiftGate system features solar powered automated traffic control gates that can be opened and closed remotely. For the project the SwiftGates needed to be linked into the sophisticated ITS infrastructure required and are integrated through the
The gates are situated at the busy Beaumont/Fanshawe intersection and operation is integrated with the movable barrier machines.
The SwiftGates were installed in March 2012 and this project is the second permanent SwiftGate installation which includes full integration into an existing or new ITS infrastructure. The first project of this kind was at the Jacques-Cartier Bridge in Canada in 2011, which allowed for the safe operation of the Bridge’s reversible lane. Versilis is now working on a number of new ITS projects to increase highway safety in an efficient and economical manner.