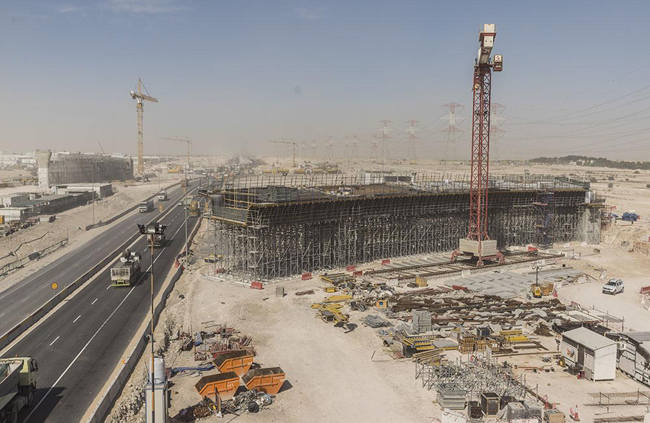
The Gulf state is also in the midst of its Qatar National Vision 2030, launched in 2008 with the aim to "transform Qatar into an advanced society capable of achieving sustainable development" by 2030. Improving infrastructure will help the country of just under 3 million people attain greater social and economic levels, according to the government.
Finishing critical projects on time is essential for the government’s strategy, such as the orbital highway around the capital city Doha. The country’s Public Works Authority -
Having tendered the project in May 2014, the contract was awarded as a joint venture between QDVC and Bin Omran Trading & Contracting. The scope of the project involved connecting the Salwa Road to the North Relief Road with 47km of highway. This includes five dual lanes for light vehicles, two dual lanes for heavy goods and industrial vehicles, six viaducts as well as 17 bridges and underpasses.
In the preparation phase, Doka calibrated elements such as the shoring erection sequence, weight to be carried, integrated safety equipment on the material, access to the work area and dismantling sequence. Some of the value-added elements used by the Doka team included 3D modelling, screw-jack extensions for each shoring tower made with AutoLISP and wood boxes cut by CNC machining.