Terex cranes have been involved in a multiple bridge repair project in the US
More than 96,000 vehicles per day travel a stretch of I-96, including its 52-year-old bridges. The Michigan Department of Transportation is in the midst of a two-year US$77 million project to repair bridges and relieve increasing congestion along Interstate 96 at the U.S. Highway 23 interchange in Livingston County.
Toebe Construction along with joint venture partner Kamminga & Roodvoets are bringing in a lot of lifting powe
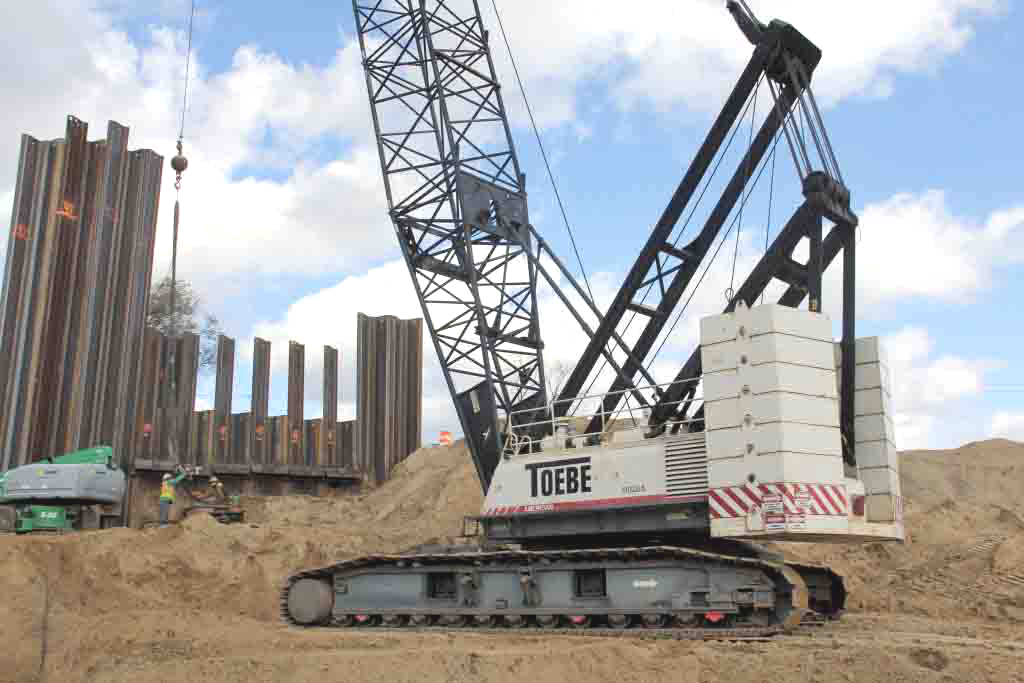
High times for Terex HC cranes on Michigan bridge work
More than 96,000 vehicles per day travel a stretch of I-96, including its 52-year-old bridges. The
Toebe Construction along with joint venture partner Kamminga & Roodvoets are bringing in a lot of lifting power - nine
To minimise disruptions to commuter traffic, the MDOT added two travel sections down the centre of the current I-96 eastbound/westbound route without demolishing the existing roadway ingress/egress ramps and bridge work. The new lanes create a direct expressway over US-23 and old US-23. After construction of the new interstate section, the existing I-96 roadway will be turned into collector-distributor lanes for easier and safer lane changes for ramp traffic. Existing bridges will receive a much-needed structural facelift.
This method for addressing the necessary upgrades at the interchanges requires new bridges over both highways. “We are constructing six new bridges first and then reconstructing seven existing bridges,” said Josh Goldsworthy, Toebe’s project manager.
It’s for this work – construction of the new I-96 eastbound and westbound interstate bridges and roadways by this fall – that the nine Terex HC series crawler cranes are being used.
To place the massive I-96 concrete bridge beams spanning SB US-23, Toebe is using the 208tonne class Terex HC 230 and 250 tonne class Terex HC 275 lattice boom crawler cranes.
With some of the beams measuring up to 55.2m long and 2.3m deep, the 111.6tonne) bridge beams were unlike anything that Toebe’s crews had encountered before. “They were the longest concrete beams ever set in the state of Michigan,” explained Goldsworthy. The MDOT shut down the highways during beam placement, so the lifts took place at night and crews had a limited number of hours in which to work.
The plan required a tandem lift with the two Terex cranes. Each crane was equipped with 27.4m of main boom and a six-part line. The cranes worked within a 15.2m maximum radius while positioning the massive beams. Maximum 68.4tonne upper and 14.5tonne lower counterweight for the HC 230 crane and 93.9tonne upper and 26.3tonne lower counterweight for the HC 275 crane were required for the lifts.
Given the beam size and weight as well as lift complexity, Toebe consulted both Jeffers Crane Service, a Terex Cranes equipment distributor, and Terex itself for capacity verification throughout the lift. “We provided Toebe with customised 0.3m increment load charts specifically for this pick and crane configuration,” said Dave Kuhlman, national accounts manager for Terex.
With the highway lanes closed, the crew members, using the HC 230 and HC 275 cranes, proceeded with the tandem lifts to place the beams on the piers. “The erection went as smooth as silk,” said Goldsworthy.
Having three 150tonne class Terex HC 165 lattice boom crawler cranes on the I-96/US-23 project helped Toebe more efficiently handle the mix of concrete beam placements combined with day-to-day lifting needs and their bridge pier pile driving needs.
The HC 165 cranes were dedicated to driving piles, freeing up the larger HC 275 cranes for concrete beam placement and smaller 100tonne capacity class HC 110 crawler cranes for miscellaneous load lifting. Toebe worked directly with Terex for instructions and guidance on safe and proper usage of the HC 165 model cranes during all pile driving applications.
Toebe equipped the Terex HC 165 cranes with 54.9m of main boom and the full 49.2tonnes of counterweight and 3.6tonnes of car body counterweight. “Even with full counterweight and the system’s maximum 82.3m boom,” explained Kuhlman, “the HC 165 can be moved in just eight truckloads.” To shorten on-site set up, the crane “self-rigs” and can lift its entire counterweight stack into position in a single operation.
Having the right equipment, coupled with the continued support from Terex and its distributor Jeffers Crane Service, is helping to keep Toebe on schedule. The 96,000-plus commuters traveling along I-96 will have a much more modern, less congested and safer highway by the year’s end.
Tulsa bridge work
Acrow Bridge has provided the temporary shoring for holding up the concrete girders and deck of an existing bridge in the US city of Tulsa.This rehabilitation work is much-needed as the bridge provides a vital traffic corridor in downtown Tulsa and carries an estimated 62,000 vehicles/day.
It is said to be the single largest project ever awarded by the Oklahoma Department of Transportation. Started in June 2009, this US$75 million project will rebuild the north and west legs of Tulsa’s Inner Dispersal Loop (IDL), replace the decks on 44 bridges on the north and west legs and repair the surface on portions of the east and south legs which include portions of I-444, US-75, US-64 and SH-5.
But bridge rehabilitation in crowded urban areas is always challenging, according to Acrow Bridge. For its work on the IDL project, the footprint available to work in is tight and located between two fast highways in a narrow median, while the loads to support are heavy.
Acrow’s temporary shoring, called Superprop Shores, is being used at three locations underneath I-444 where the piers and pier caps were worn out and failing during repair. A single Superprop Shore, assembled from Acrow bridge components, can support up to 270tonnes. By bracing Acrow shores with Acrow panels, a shoring system of simplicity in design can be used in any vertical, horizontal and knee-bracing application.
The firm was also able to quickly address a design change in the middle of the project that required a re-engineering of the installation and support system. According to the company, a key factor in this was its rental programme and its ability to provide crucial structural components quickly and economically.