Two of the largest cranes in Switzerland recently were called upon to lift an 884tonne, 162m-long connecting bridge between two buildings at the Coop distribution centre in Schafisheim.
“The individual bridge components had enormous gross weights of up to 275tonnes and required us to use working radii of up to 29m,” said Andre Huber, project manager at Toggenburger, the company that took on the task.
To get the job done, Toggenburger rolled out its biggest machinery which also happen to be the two lar
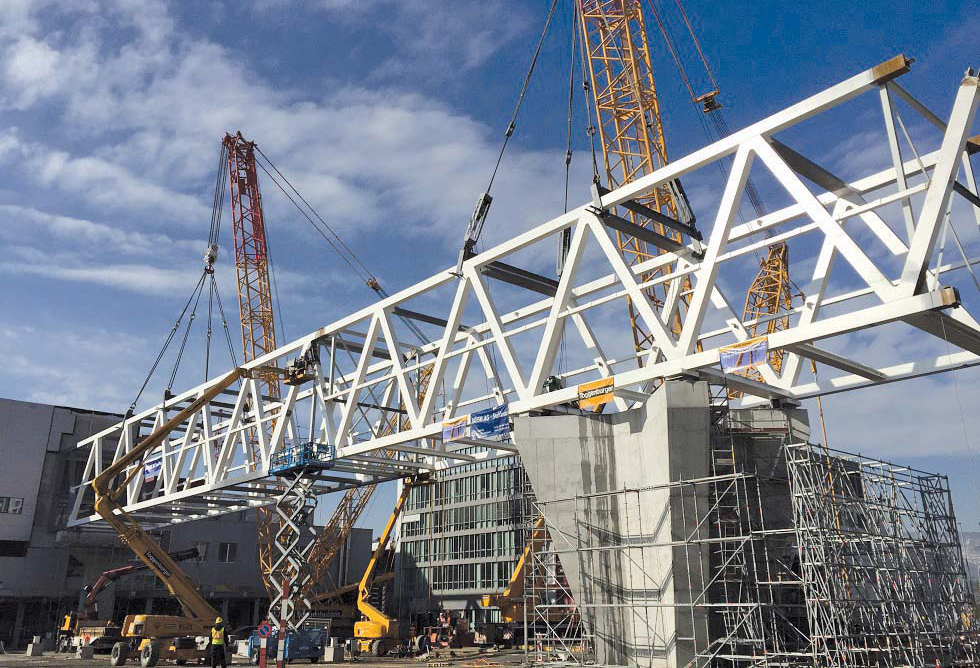
Terex CC 2400-1 and CC 2500-1 lattice boom crawler cranes at work
Two of the largest cranes in Switzerland recently were called upon to lift an 884tonne, 162m-long connecting bridge between two buildings at the Coop distribution centre in Schafisheim.
“The individual bridge components had enormous gross weights of up to 275tonnes and required us to use working radii of up to 29m,” said Andre Huber, project manager at8227 Toggenburger, the company that took on the task.
To get the job done, Toggenburger rolled out its biggest machinery which also happen to be the two largest cranes available in the country – the1222 Terex CC 2400-1 and CC 2500-1 lattice boom crawler cranes.
It took 48 trucks to deliver the cranes to the job site in Schafisheim, explained Huber. Despite limited space on site, Toggenburger’s experienced team of seven easily assembled both cranes in only two and a half days – all the delivery operations continued at the premises.
The CC 2400-1 crane was set up with an SSL configuration featuring a main 49m boom, a counterweight of 160tonnes, a 40tonne central ballast and an SL counterweight of 240tonnes. The CC 2500-1 crane was configured almost identically. The only difference was the SL counterweight of 250tonnes. A 130tonne hydraulic crane acted as an assist crane.
Huber said the layout of the site made it impossible to lift the two-level bridge as a single unit over the road between the two buildings. To overcome this, the bridge manufacturer delivered the steel structure in component form. These were welded into seven bridge elements at the work site and placed on the bridge’s three piers in five lifts.
“This required an extraordinary level of precision, since the tolerances for joining the individual elements were a matter of millimeters,” said Toggenburger’s Mchael Dudler, who, along with Huber, oversaw the project.
Special yokes fabricated to pick up the elements made it possible to attach hoist cables with shackles and lift two elements simultaneously. To do this, one element was rigidly rigged to one of the cranes. The other crane supported an arrangement with 140tonne strand jacks placed at three rigging points between the hoist cables and the yoke. These strand jacks, in turn, made it possible to precisely control the lateral and longitudinal position of the second element using hydraulic power.
The size of the bridge elements meant the Toggenburger team had to use5047 Genie aerial work platforms to rig the load-securing equipment. “Despite the sophisticated setup for maneuvering the loads, we were a little worried. Any strong winds would have prevented us from performing the lifts,” Dudler said.
But the anxiety proved to be unwarranted, as the weather was perfect on both lifting days. Several hundred people turned out on the beautiful morning in February to watch the spectacular first two lifts at the site, a day-long procedure.
The Terex CC 2400-1 crawler crane started by picking up the double package of elements 1 and 2 directly from the assembly site at a working radius of 18m. The crane then lifted the element, which had a total length of 55.5m and weighed 275tonnes together with the corresponding load-securing devices, to a height of 12m before safely putting it down on the piers. During this operation, the crane operated at around 97% capacity.
Meanwhile, the CC 2500-1 crane brought bridge element number 3, which was 41m long and had a gross weight of 250tonnes, to its installation position. A modular trailer moved the element forward from the assembly site for the crane to pick it up at a working radius of 18 meters and place it into position. In this case, the crane operated at 74% capacity.
With this, the first half of the span – to the center pier – was in place. “Afterwards we moved the cranes about 100m forward so that they would be in place for the next day,” reports Huber.
On Sunday, the CC 2400-1 crane lifted element 4, a 22m-long section weighing 95tonnes. It required load-securing equipment weighing 20tonnes at a working radius of 29m.Bridge elements 5/6, which were nearly 49m long and had a gross weight of 240tonnes, were the job of the CC 2500-1 crane, which used a working radius of 2m and operated at 83% of capacity.
The assist crane finished off the job on schedule dropping in place the 17.5tonne final element 7.
“When you have the right machines, a good team and professional planning, even the most demanding projects become routine. But you’re still relieved at the end when everything goes smoothly,” said Huber.
“The individual bridge components had enormous gross weights of up to 275tonnes and required us to use working radii of up to 29m,” said Andre Huber, project manager at
To get the job done, Toggenburger rolled out its biggest machinery which also happen to be the two largest cranes available in the country – the
It took 48 trucks to deliver the cranes to the job site in Schafisheim, explained Huber. Despite limited space on site, Toggenburger’s experienced team of seven easily assembled both cranes in only two and a half days – all the delivery operations continued at the premises.
The CC 2400-1 crane was set up with an SSL configuration featuring a main 49m boom, a counterweight of 160tonnes, a 40tonne central ballast and an SL counterweight of 240tonnes. The CC 2500-1 crane was configured almost identically. The only difference was the SL counterweight of 250tonnes. A 130tonne hydraulic crane acted as an assist crane.
Huber said the layout of the site made it impossible to lift the two-level bridge as a single unit over the road between the two buildings. To overcome this, the bridge manufacturer delivered the steel structure in component form. These were welded into seven bridge elements at the work site and placed on the bridge’s three piers in five lifts.
“This required an extraordinary level of precision, since the tolerances for joining the individual elements were a matter of millimeters,” said Toggenburger’s Mchael Dudler, who, along with Huber, oversaw the project.
Special yokes fabricated to pick up the elements made it possible to attach hoist cables with shackles and lift two elements simultaneously. To do this, one element was rigidly rigged to one of the cranes. The other crane supported an arrangement with 140tonne strand jacks placed at three rigging points between the hoist cables and the yoke. These strand jacks, in turn, made it possible to precisely control the lateral and longitudinal position of the second element using hydraulic power.
The size of the bridge elements meant the Toggenburger team had to use
But the anxiety proved to be unwarranted, as the weather was perfect on both lifting days. Several hundred people turned out on the beautiful morning in February to watch the spectacular first two lifts at the site, a day-long procedure.
The Terex CC 2400-1 crawler crane started by picking up the double package of elements 1 and 2 directly from the assembly site at a working radius of 18m. The crane then lifted the element, which had a total length of 55.5m and weighed 275tonnes together with the corresponding load-securing devices, to a height of 12m before safely putting it down on the piers. During this operation, the crane operated at around 97% capacity.
Meanwhile, the CC 2500-1 crane brought bridge element number 3, which was 41m long and had a gross weight of 250tonnes, to its installation position. A modular trailer moved the element forward from the assembly site for the crane to pick it up at a working radius of 18 meters and place it into position. In this case, the crane operated at 74% capacity.
With this, the first half of the span – to the center pier – was in place. “Afterwards we moved the cranes about 100m forward so that they would be in place for the next day,” reports Huber.
On Sunday, the CC 2400-1 crane lifted element 4, a 22m-long section weighing 95tonnes. It required load-securing equipment weighing 20tonnes at a working radius of 29m.Bridge elements 5/6, which were nearly 49m long and had a gross weight of 240tonnes, were the job of the CC 2500-1 crane, which used a working radius of 2m and operated at 83% of capacity.
The assist crane finished off the job on schedule dropping in place the 17.5tonne final element 7.
“When you have the right machines, a good team and professional planning, even the most demanding projects become routine. But you’re still relieved at the end when everything goes smoothly,” said Huber.