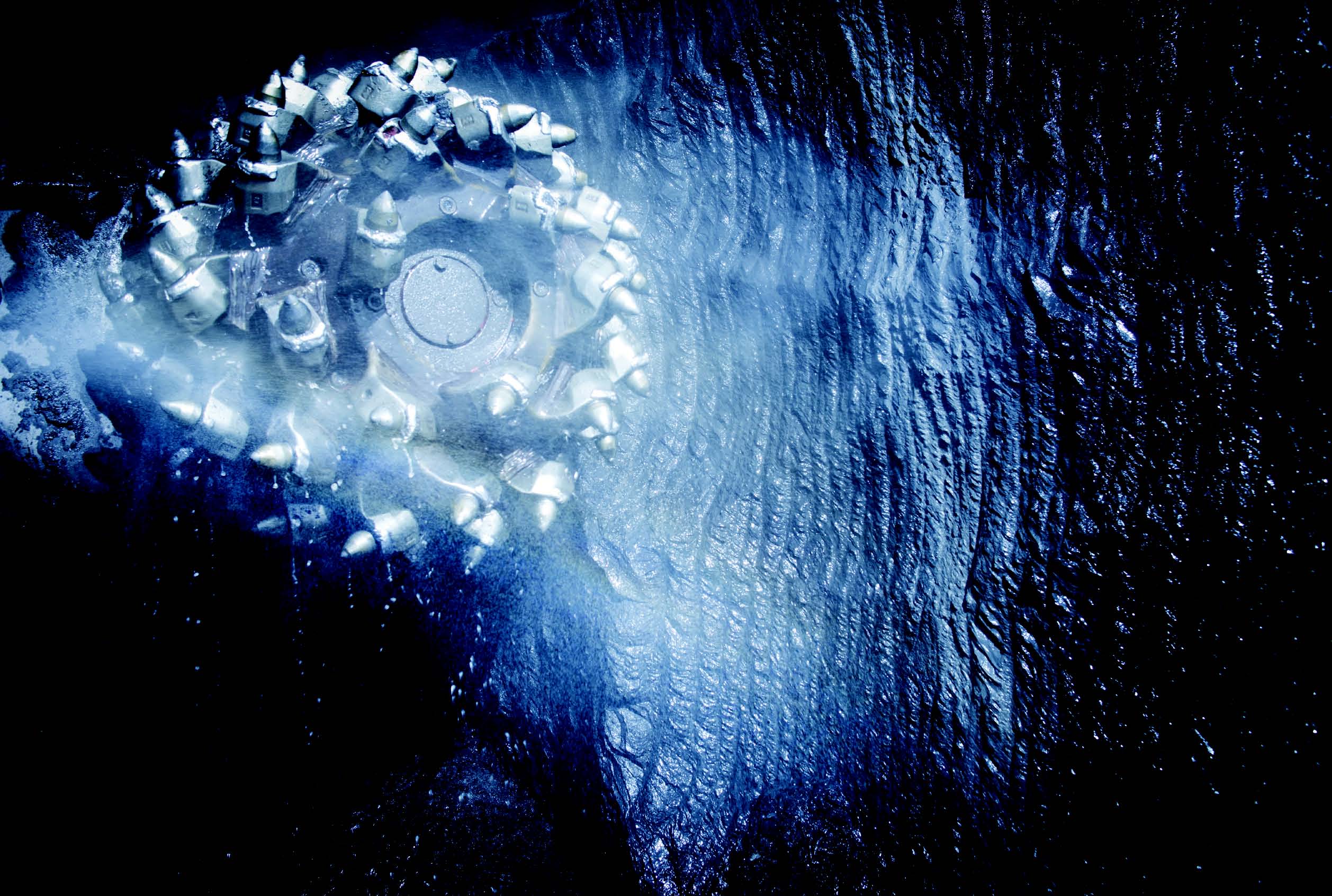
A wealth of major road tunnel construction projects and significant cant ITS installations within existing key road tunnels have been recently completed or will soon be underway. Guy Woodford examines some of them
A state-of-the art Tunnel Boring Machine (TBM) - the 10th largest ever to be built worldwide will be put to work later this year onThe giant
The recent handover of the TBM, which will have a top speed of 80mm a minute, or 0.0005km/h, was marked by an official signing at Guangzhou in south east China, where the German firm Herrenknecht has a factory. It follows 14 months of design, building and testing the huge machine, said to be tailored to meet the rare ground conditions it will encounter on the Waterview Connection works.
The equivalent height of a three storey building (14.5m) and length of a rugby field (97m), the TBM’s circular cutting head is painted black with a silver fern logo. The machine will be dismantled for shipment to New Zealand and is due to arrive in Auckland in eight pieces, collectively weighing 2,300tonnes, in July before being reassembled at the project’s southern tunnel portal to begin tunnelling in October 2013.
The Waterview Connection is part of the Western Ring Route road of national significance and will join SH20 (Southwestern Motorway) and SH16 (Northwestern Motorway) to complete a 47km-long motorway alternative to SH1 and the Auckland Harbour Bridge.
“The size of this project and the size of the tunnel boring machine are both on a scale the likes of which we have never seen before in New Zealand,” says the New Zealand Transport Agency’s (NZTA) state highways manager for Auckland and Northland, Tommy Parker.
“Since mid-2012 we have been preparing a trench that will not only form the southern tunnel approach, but provide the TBM’s launch pad,” Parker adds. “This requires us to excavate to a depth of 30metres, initially, drilling and blasting through a 15m-thick layer of very hard volcanic rock.”
To construct two 2.5km-long tunnels, each wide enough for three lanes of traffic, the TBM will pass beneath the rock and tunnel through softer, clay-like soil known as the East Coast Bay Formation. It is expected to take a year to complete the first tunnel, emerging beyond Great North Road in Waterview, where work is already underway to prepare for its arrival and turnaround for the return journey.
When completed in 2017 having seen around 800,000m³ of earth removed from both tunnels, enough to fill 320 Olympic-sized swimming pools, Parker says the project will help unlock Auckland’s potential for economic growth and will also have considerable benefits for its Northland and Waikato/Bay of Plenty neighbours.
“Easing pressure on the city’s existing motorway network will have flow-on effects that will encourage business growth, tourism and jobs. For the first time there will be a direct motorway link between Auckland International Airport and the CBD. The network will become more resilient – two motorway links through Auckland reduce the risk of any disruption to traffic bringing the city to a standstill.”
The Waterview Connection, Parker adds, aims to deliver maximum regional and national benefits with a minimum long-term impact on the communities surrounding the project.
“Tunnelling obviously allows us to do this, and a strong focus on urban design and landscaping – like the rehabilitation work we’ve already carried out around Oakley Creek – ensures that the effects of all above ground work are carefully mitigated.”
In Europe, Herrenknecht has delivered a TBM for the construction of a road tunnel under the Vistula River in Gdansk, Poland.
With its freight and ferry terminal and the airport, Gdansk which has a city population of more than 400,000 and a metropolitan population of over one million, is a major transport hub in Poland as well as for connections from Scandinavia to Central and Eastern Europe.
Now the new 10km-long Slowacki route is to improve the transport infrastructure in the greater Gdansk area. It links
The Slowacki route will pass under the Vistula with a twin tube tunnel with a total length of 1.4km. The tunnel tubes will each accommodate two road lanes and will be connected by seven cross passages for escape routes. For the construction of this major tunnel, the building contractor OHL ordered a Mixshield with a diameter of 12.56m.
According to Herrenknecht project manager Peter Griesbach, a challenging advance under the Vistula awaits the machine and the jobsite crews: "At certain points there will only be about eight meters above the machine to the bottom of the river," says Griesbach.
The machine will be sealed against penetrating groundwater or subsoil at pressures of up to four-bar: between shield skin and lining segment with a triple wire brush seal and a quadruple sealing system on the drive. The equipment was said to be designed in such a way that tunnelling can also be carried out on the steep 4% downward and upward gradients at the beginning and in the second half of the tunnel respectively.
Group subsidiary Herrenknecht Formwork produces the moulds in which the segments for lining the tunnel tubes are made. As a full-service provider in tunnel construction, at the customer's request Herrenknecht is also supplying additional equipment: the separation plant and the pumps for slurry circulation in the tunnel, the compressor station, the navigation system (VMT), the start-up construction and equipment for the material and personnel transport in the tunnel (MSD).
Herrenknecht says its specialists will support the customer's personnel with service and equipment during on-site assembly of the machine and through to successful completion of the project.
Remaining in Europe, a US$1.745 billion (NOK 10bn) sub-sea road tunnel, known as Rogfast, under Boknafjorden, between Mekjarvik and Arsvågen, in south west Norway will form part of a new E39 motorway.
According to the government construction work on the E39 Rogfast will begin by 2015, at the latest. The tunnel will be around 25.5km long and 385m below sea level at its deepest point, both of which would be new world records. Creating a fast and ferryless connection between the cities of Stavanger and Haugesund, the E39 Rogfast is also expected to reduce the travel time between Stavanger and Norway’s second largest city, Bergen.
The overall US$26.45 billion (NOK 150bn) E39 motorway project is backed by the Norwegian Government and is expected to take up to 20 years to complete.
Meanwhile, the
Selected for funding under the 2011 TEN-T Annual Call, the project will develop several safety measures around the E25/ A2 urban tunnel, including the construction of a firehouse near the south entrance of the tunnel, the building of two escape tubes in the tunnel, and the construction of foot and bicycle paths and bridges. The project also includes the construction of a connection with the railway station and inland water ports in Maastricht.
The Maastricht urban highway tunnel will remove a key bottleneck in the heavy north-south freight transit between Aachen and Liège, through which goods travel to/from Rotterdam and Antwerp – the largest ports in Europe. The two-level double tube tunnel will increase road capacity and will facilitate lower carbon inter-modal connection of the biggest inland ports in The Netherlands (Maasbracht and Born) and in Belgium (Liège).
Managed by the
Vital Technology has provided a multidiscipline supervisory control and data acquisition (SCADA) system for the Medway Tunnel under the River Medway between Strood and Chatham in Kent, southern England.
The work at Medway has been a SCADA replacement project in which Ematics, a subsidiary company within
The custom-developed SCADA system at Medway is a Graphical User Interface (GUI) said to interact with diverse subsystems including access control, lighting, ventilation, drainage, fire systems, intruder alarms, air-conditioning, radio rebroadcast, video surveillance and a video incident detection system.
Making the tunnel safe by optimising driver conditions is a principal concern and particular attention has been paid to lighting. The tunnel lighting is said to have been adjusted to match ambient light at the approach roads to the tunnel entrances and exits in a graduated manner. This means that drivers do not find themselves dazzled or struggling to make out detail.
The system provided by Vital Technology consists of a SCADA client-server layer which provides the operator with the GUI required for tunnel operations and a PLC control layer which handles the business logic and tunnel control activities. In the event of SCADA or PLC failure, Vital Technology says there is automatic transfer to a back-up system such that no single point of failure can interrupt tunnel operations.
The Medway Tunnel works include the supply and installation of 24 video surveillance cameras, for which two independent video wall systems were provided in separate locations. These video streams are processed and distributed to the video walls through DigiWall software. This software is also client-server based and has been developed in-house by Sicura Systems, another Vital Technology firm. Sicura Systems also specified and supplied analogue and IP-addressable CCTV cameras from
Alpine BeMo Tunnelling decided to use the powerful 135tonne
The tunnel project is part of a US$83.87 million (€64.5mn) investment aimed at enhancing its home region’s tourist industry, while simultaneously improving the local community’s quality of life.
The MT720 machine used on the Markovec tunnel project machine had recently been used in the Brisbane Airport Link project in Australia. Normally after a three month service period the machine is overhauled in Zeltweg, Austria, where the tubes and electrical system are restored and wear parts replaced. But, in this case,
A principal factor in choosing the Sandvik Tunnelling Roadheader MT720, and bringing the specific model back from Australia, was said to be the high housing density of the local area, with no more than 15m of distance between the tunnel and the buildings at the northern end of the portal. Due to a successful campaign by the local community, combined with the difficult geology of the rock involved, it was decided that any construction work should be carried out without any blasting operations, and thus cutting should be the only permitted heading method of tunnelling.
The MT720 was said to deliver such impressive results that Alpine decided to use this heading method in the other tunnel sections, with the production figures endorsing this decision.
Using a two shift operation, from 6am until no later than 10pm, the average daily advance has been a notable 6.18m. On the advance rate Michael Schuster, the Alpine BeMo Tunnelling project manager, says that “no other machine on the market has such a capacity.”
While tunnelling with the MT720, crews achieved excavation rates of approximately 35 to 45 m³/hr (equal to 4 m/day in top heading excavation) in hard-rock formation, and approximately 55 to 65 m³/hr (equal to 8 m/day in top heading excavation) in the marl-sandstone formation. Two main benefits were said by Sandvik to be identified from the use of the MT720 roadheader: firstly, a very low pick consumption of only 0.008 picks per m³ contributed to low tunnelling cost; and secondly, the exact tunnel profile contour required a reduced volume of concrete. Thus the time consuming and expensive filling of over-break cavities with sprayed concrete has been avoided.
Sandvik says that through the use of its MT720 tunnelling roadheader, the Markovec tunnel project has been achieved at a lower cost that was initially estimated, and with minimal disruption for local residents.
China State Construction wins Hong Kong tunnel contract
A unit of