Major gains in tunnelling productivity and performance are claimed for a series of new machines now coming to market
These new tools will help contractors boost productivity and versatility in an array of applications. The new equipment items are designed for a variety of tasks, including drilling and shotcreting duties.
One of the leaders in the underground equipment sector, Atlas Copco, has a new line-up of single and twin boom drill rigs, which suit duties in smaller tunnelling applications. The fi
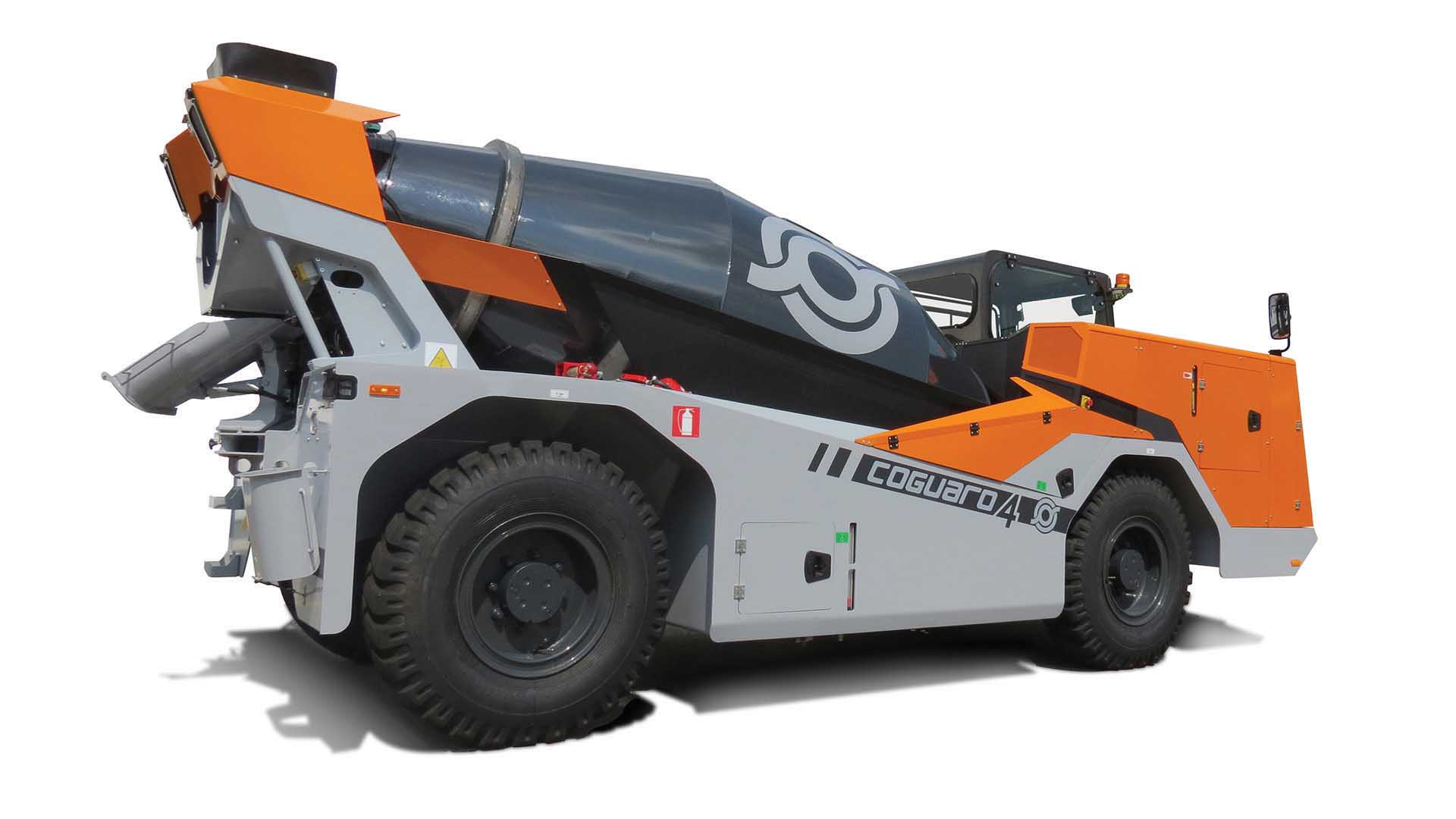
CIFA has designed its new shotcreting machine to meet tough tunnelling requirements
Major gains in tunnelling productivity and performance are claimed for a series of new machines now coming to market
These new tools will help contractors boost productivity and versatility in an array of applications. The new equipment items are designed for a variety of tasks, including drilling and shotcreting duties.
One of the leaders in the underground equipment sector,161 Atlas Copco, has a new line-up of single and twin boom drill rigs, which suit duties in smaller tunnelling applications. The firm’s latest Boomer M-series drill rigs have benefited from a major upgrade and are now being made available worldwide.
According to the firm, these new models build on the proven features of the earlier designs and are said to combine improved efficiency with additional capabilities. More powerful and safer to operate than previous models, these new units are said to be robust and durable and can cope with much tougher operating requirements.
The firm says that it has responded to customer needs by developing rigs that are also more versatile and can handle both face drilling and bolting tasks. This means that a contractor can use the same machine for both jobs, reducing the need for separate items of equipment on a project. The M-series rigs are equipped with COP 1838HD+ rock drills and can be specified with either the well-proven hydraulic control system or the firm’s highly sophisticated RCS 5 rig control system.
The fitting of Atlas Copco’s sophisticated rig control system allows the machines to deliver hole accuracy, providing a significant gain in blasting efficiency and delivering major reductions in tunnelling time and costs. Higher productivity, longer service intervals and lower running costs have also been achieved in extensive field-testing carried out in Australia.
The machines are equipped with Atlas Copco’s much stronger BUT 36S booms, which provide better articulation and faster, more accurate positioning. The machines also benefit from a new filtration system that keeps lubrication air and hydraulic oil free from water and fine particles. This improves the quality of the air and the oil, which, in turn, prolongs the life of the hydraulic components and the rock drills.
The rigs also provide better safety for the operator. The BUT 36S boom’s safe bolting configuration makes it possible to swing the feed all the way back to the cab. This feature allows the operator to load the unit with bolts while standing on platforms on either side of the rig. As a result, there is no need to work in front of the machine under an unsupported roof, substantially reducing the risk of injury from a rockfall. And for added safety, the large cab is also ROPS/FOPS certified.
Designed to handle mixing duties in a range of tough underground applications, the new Coguaro from2203 CIFA can work in various demanding tunnelling projects. Although compact in design, the machine offers a carrying capacity of up to 4m3. An electronically-controlled hydrostatic transmission is said to boost the machine’s capabilities underground, allowing it to manoeuvre precisely in tight underground applications, even when fully laden. The 299 Perkins STEP 3-A diesel powers the machine through twin hydrostatic motors mounted directly on the axles, a configuration that ensures maximum traction and reliability, while also reducing fuel consumption. This driveline provides power to all four wheels and the machine also has all-wheel-steering for manoeuvrability, as well as a strong chassis design that can cope with tough working applications.
Highly sophisticated, the machine is said to offer customers both functionality and good ergonomics for operators. And for safety, the drum rotation control locks out for maintenance work. Machine functions are managed by the control speed drive (CSD), while safety is further improved by the provision of a fully-enclosed ROPS-FOPS cab. Another safety feature is the infrared rear-view camera, which helps when manoeuvring in tunnels. Other safety options include electronic sensors for obstacle detection and an active fire control system.
The firm has won an order for the machine already, with the first unit being used in a challenging application in Peru, operating at an altitude of 4,700m and in high humidity, as well as in the presence of acidic water.
German company1259 Putzmeister is broadening its range of tunnelling equipment for lifting with the introduction of its new MINELIFT 4 scissor lift platform. This new unit offers a lifting height of 4m and a 4tonne capacity, providing contractors with a highly stable working platform that is also said to be versatile and mobile. The machine can be used for lifting both heavy loads and personnel in tunnelling applications. This machine can be used for an array of duties such as for piping and ventilation work.
The machine can be configured to allow contractors to install water, air, drainage, and tailing pipes. It features a drop-wing platform extension that increases lateral width by 700mm, providing a work surface total of 3,400x2,550mm. Meanwhile its high capacity crane allows pipes to be lifted safely. The machine also features a pipe handling system with two independent telescopic arms, designed for pipes with diameters from 100-200mm and each unit offers a load capacity of 300kg. Using this machine is said to allow both safe and efficient operation during pipe installation.
The machine can also be specified with an auxiliary lift platform for use in ventilator installation jobs. This device offers a load capacity of 2.5tonnes and lifts to a height of 1.1m from the main platform.
The machine is said to have a compact design with heavy-duty axles, as well as four-wheel-steering and four-wheel-drive for manoeuvrability and traction underground. Power comes from a diesel rated at 130kW and that drives through an integrated continuously variable drive (ICVD). This is said to ensure efficiency and maximum power in all operating applications. The combination of the hydrostatic drive system, slope measurement, and Putzmeister control software are key to the machine’s automatic downhill speed control system. This allows the machine to automatically adapt its maximum speed to the slope, taking full advantage of the engine retention capacity, reducing the risk of accidents. Multi-plate, oil immersed disc brakes are fitted to both axles and these are hydraulically-operated with two independent circuits for additional safety. This system provides great stopping power and a long working life, even in the most demanding conditions.
The MINELIFT 4 also has a FOPS/ROPS certified driving cab that is said to be ergonomic in design and is available with air-conditioning and heating if required. The machine is equipped with LED working lights both on the platform and on the vehicle, providing operators with a safe environment when underground. A reversing camera with a night vision function also allows the operator to manoeuvre in underground applications.
These new tools will help contractors boost productivity and versatility in an array of applications. The new equipment items are designed for a variety of tasks, including drilling and shotcreting duties.
One of the leaders in the underground equipment sector,
According to the firm, these new models build on the proven features of the earlier designs and are said to combine improved efficiency with additional capabilities. More powerful and safer to operate than previous models, these new units are said to be robust and durable and can cope with much tougher operating requirements.
The firm says that it has responded to customer needs by developing rigs that are also more versatile and can handle both face drilling and bolting tasks. This means that a contractor can use the same machine for both jobs, reducing the need for separate items of equipment on a project. The M-series rigs are equipped with COP 1838HD+ rock drills and can be specified with either the well-proven hydraulic control system or the firm’s highly sophisticated RCS 5 rig control system.
The fitting of Atlas Copco’s sophisticated rig control system allows the machines to deliver hole accuracy, providing a significant gain in blasting efficiency and delivering major reductions in tunnelling time and costs. Higher productivity, longer service intervals and lower running costs have also been achieved in extensive field-testing carried out in Australia.
The machines are equipped with Atlas Copco’s much stronger BUT 36S booms, which provide better articulation and faster, more accurate positioning. The machines also benefit from a new filtration system that keeps lubrication air and hydraulic oil free from water and fine particles. This improves the quality of the air and the oil, which, in turn, prolongs the life of the hydraulic components and the rock drills.
The rigs also provide better safety for the operator. The BUT 36S boom’s safe bolting configuration makes it possible to swing the feed all the way back to the cab. This feature allows the operator to load the unit with bolts while standing on platforms on either side of the rig. As a result, there is no need to work in front of the machine under an unsupported roof, substantially reducing the risk of injury from a rockfall. And for added safety, the large cab is also ROPS/FOPS certified.
Designed to handle mixing duties in a range of tough underground applications, the new Coguaro from
Highly sophisticated, the machine is said to offer customers both functionality and good ergonomics for operators. And for safety, the drum rotation control locks out for maintenance work. Machine functions are managed by the control speed drive (CSD), while safety is further improved by the provision of a fully-enclosed ROPS-FOPS cab. Another safety feature is the infrared rear-view camera, which helps when manoeuvring in tunnels. Other safety options include electronic sensors for obstacle detection and an active fire control system.
The firm has won an order for the machine already, with the first unit being used in a challenging application in Peru, operating at an altitude of 4,700m and in high humidity, as well as in the presence of acidic water.
German company
The machine can be configured to allow contractors to install water, air, drainage, and tailing pipes. It features a drop-wing platform extension that increases lateral width by 700mm, providing a work surface total of 3,400x2,550mm. Meanwhile its high capacity crane allows pipes to be lifted safely. The machine also features a pipe handling system with two independent telescopic arms, designed for pipes with diameters from 100-200mm and each unit offers a load capacity of 300kg. Using this machine is said to allow both safe and efficient operation during pipe installation.
The machine can also be specified with an auxiliary lift platform for use in ventilator installation jobs. This device offers a load capacity of 2.5tonnes and lifts to a height of 1.1m from the main platform.
The machine is said to have a compact design with heavy-duty axles, as well as four-wheel-steering and four-wheel-drive for manoeuvrability and traction underground. Power comes from a diesel rated at 130kW and that drives through an integrated continuously variable drive (ICVD). This is said to ensure efficiency and maximum power in all operating applications. The combination of the hydrostatic drive system, slope measurement, and Putzmeister control software are key to the machine’s automatic downhill speed control system. This allows the machine to automatically adapt its maximum speed to the slope, taking full advantage of the engine retention capacity, reducing the risk of accidents. Multi-plate, oil immersed disc brakes are fitted to both axles and these are hydraulically-operated with two independent circuits for additional safety. This system provides great stopping power and a long working life, even in the most demanding conditions.
The MINELIFT 4 also has a FOPS/ROPS certified driving cab that is said to be ergonomic in design and is available with air-conditioning and heating if required. The machine is equipped with LED working lights both on the platform and on the vehicle, providing operators with a safe environment when underground. A reversing camera with a night vision function also allows the operator to manoeuvre in underground applications.