Demolition is a highly specialised business, as the machinery required to carry out the work on high-rise demolition contracts can be very site specific. Today's high reach demolition rig is no longer simply a tracked excavator with a long boom, indeed some machines cannot be used as excavators at all. Likewise a machine that is dedicated to carrying a 2.5 or 3tonne shear or hammer will need to be built to take the stresses and strains of demolition life.
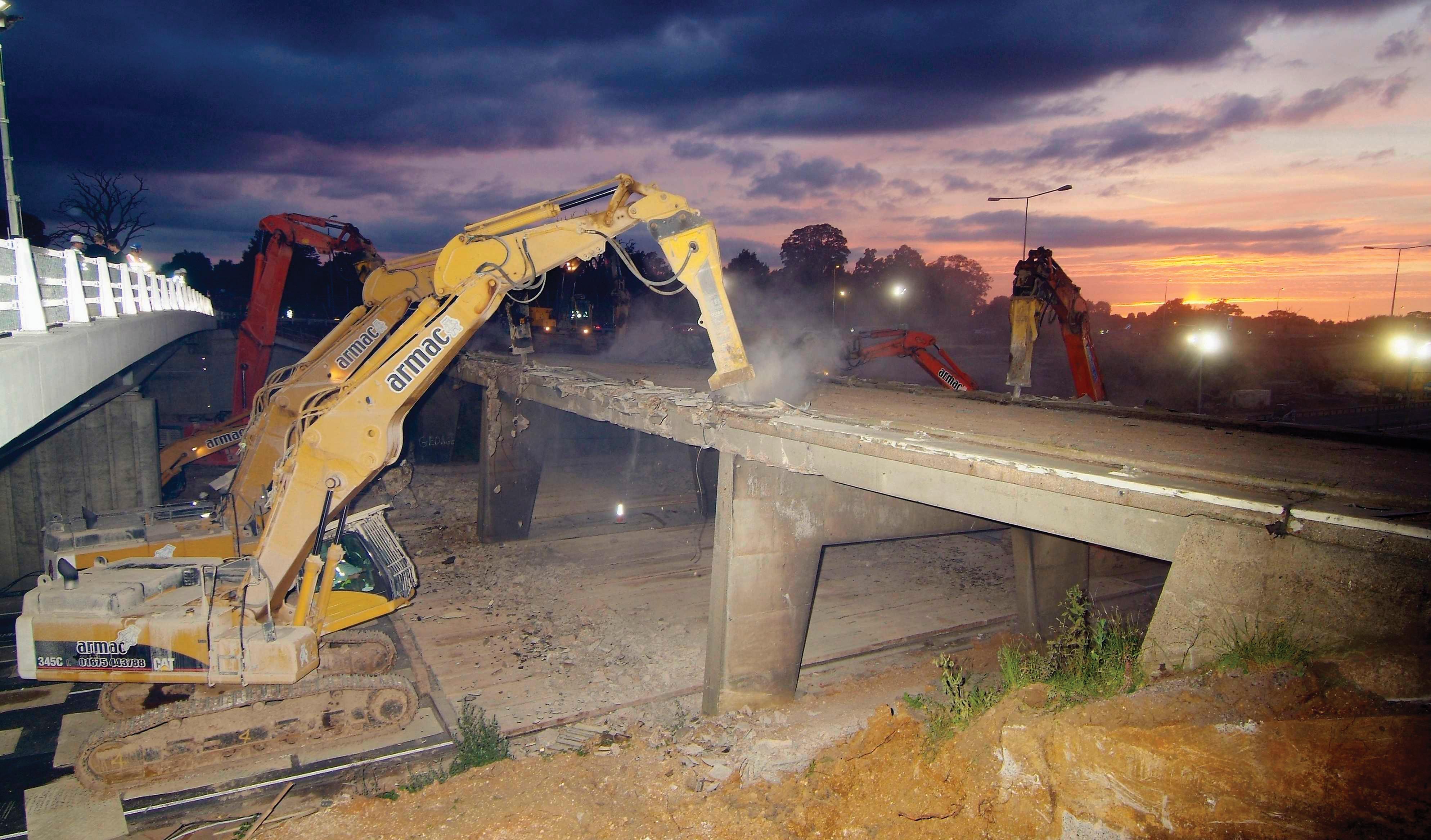
Using long reach demolition equipment allows structures such as overpasses and highway bridges to be removed quickly and safely
Demolition is a highly specialised business, as the machinery required to carry out the work on high-rise demolition contracts can be very site specific. Today's high reach demolition rig is no longer simply a tracked excavator with a long boom, indeed some machines cannot be used as excavators at all. Likewise a machine that is dedicated to carrying a 2.5 or 3tonne shear or hammer will need to be built to take the stresses and strains of demolition life.
Many of the ultra long boom machines are designed and built solely with high reach work in mind and may never wear a bucket. However, manufacturers are increasingly offering pinned booms, which allow operators to change between high reach equipment and heavy duty digging arms for clear-up work, increasing versatility.
Height and reach have for some years now been almost a holy grail for large demolition contractors and for the manufacturers supplying them. Ever longer booms, combined with greater counterweight, wider track frames and tilting cabs have allowed contractors to keep operatives well away from the area of work, literally at dipper arm's reach from the most dangerous areas of the site.
Traditionally the numbers involved have been relatively small, putting the design and engineering work firmly in the hands of specialist equipment builders such as the UK's1442 Kocurek Excavators, which has built some incredible machines, incorporating telescopic main booms as well as conventional three-piece high reach arms. Original equipment manufacturers have worked hand in hand with these specialists to provide a suitable base machine, but many of the booms and arms have been made to order for each contractor.
The last decade however has seen that mix change, with an increasing number of OEMs keen to get in on the act. This is partly due to the increased flexibility of manufacturing sites, which allow individual machine build specifications to be engineered within a production line, or more often on adjacent one-off lines that operate within the factory.
It is also due to the fact that manufacturers are working more closely with their customers, building to specific requirements rather than simply rolling out identical machines whatever the need on site.
Add into the mix the fact that those same manufacturers are in many cases the same firms that are offering the range of powered attachments that will be working with the carrier machine, and it is easy to see why they are almost all building demolition specification excavators these days.
Of course demolition spec need not mean a long boom and dipper arm, or even a three-piece boom. For many contractors demolition means strength and robust design, capable of handling hydraulic breakers and shears for up to eight hours/day. Excavators used on bridge demolition for example might need to work through the night with a breaker or cutting equipment to drop a motorway bridge within strict road closure or lane rental commitments. In these cases the demolition machine bears closer resemblance to a mass excavator, with a sturdy main boom and short dipper stick to carry heavy duty attachments, and tough cab and undercarriage protection to look after the operator and the machine.
They may need to carry frame-mounted falling object guards (FOG) on top of the standard ROPS/FOPS cab. Bolted-on side impact protection strips prevent damage as the machine's upper structure slews round, while double thickness heavy duty doors provide protection for engines and hydraulic components.
Down below the slew ring the machine will require full length track chain guards with heavy under plating beneath the slew area and around any hydraulic hoses and motors. The machine's internals will need to be protected too, with fine mesh screens preventing radiator cores from clogging and reversing fans capable of blowing dust and debris away from the cooling pack.
718 Liebherr was one of the first to provide a dedicated demolition specification on some of its crawler machines. The company has a reputation for building sturdy equipment and for making as much of the machine in-house as possible, including engines and hydraulic systems. Last year alone the firm added high reach options to its R954C and the giant R974 VH-HD, which tips the scales at more than 130tonnes and offers a maximum reach of 41m. However the range starts with a demolition specific version of the R934C, which weighs in at up to 47tonnes and provides a working height of up to 20m. Despite being the smaller model, even the R934C comes with Liebherr's Demolition Control system (LDC), which provides safe working envelope information to the operator and automatically prevents the machine over reaching.
178 Caterpillar is another manufacturer that has long specialised in building a range of high demolition rigs, with five models spanning from the 38tonne 325D to the 100tonne 385C. In each case the machine comes with a reinforced upper frame, tool cylinder protection and the option of a tilting high visibility demolition cab, with increased protection and falling object guards. Caterpillar also offers more conventional heavy duty excavators along with a wide range of work tools, including multi-processors, pulverisers, breakers, grapples and shears, each matched to the hydraulic output of its carrier models. Cat will have even more to offer demolition customers at this year's Bauma exhibition, with at least one new model, called the DEM50, making its first appearance. There are no solid details as yet on specification though.
Having an established demolition offering is a similar story at2300 Komatsu, with high reach versions of four models from the PC240-8HR to the PC450-8HR. All of the machines are built in-house at the firm's excavator facility in the UK, and the three larger models can all be specified with an excavation boom as well as the high reach equipment. This allows operators to change between high reach and digging booms as the work demands.
For the likes of Komatsu and fellow Japanese firm233 Hitachi there is certainly a lot of sense in building demolition specification machines. Both companies also produce mobile crushing equipment, so can offer a complete equipment solution for the demolition contractor that is not simply dependent on attachments for the base machines.
2394 Volvo offers two distinct lines of demolition excavator, what it calls the primary ultra-high reach models, and the secondary reinforced excavators for bucket and attachment work. There are four high reach machines available at present, from the 17m EC290C HR to the 32m boom EC700B HR. In each case capacities and flows have been optimised to work with pulverisers, grapples, crushers and hammers. The machines come with a tilting cab, offering 30º of rake for an improved view of the boom. Additional modular counterweights ensure stability, along with optional hydraulically variable undercarriage widths on some models. These Volvo demolition rigs also come with a Total Moment Indicator to warn the operator if the machine is approaching its safe working load. For the secondary demolition work, not requiring high reach capability, Volvo offers heavy duty versions of six models from the EC210C to the EC700B.
176 Case has a long history of building unusual booms and dippers at its factories in France, though to some extent this came to an end when it joined forces with Sumitomo for the production of excavators. However, last year the firm introduces CSX, or Case Special Excavators, in a separate site in Zeebrugge. CSX is dedicated to special attachment design, engineering and production, building everything from waste handling machinery to high reach demolition booms.
Even manufacturers not traditionally known for their involvement in the heavy demolition industry have started producing their own high reach equipment and heavy duty demolition specification machines.255 JCB entered the market a few years ago with the JS330XD and the high reach JS330XD HRD. The JS330XD comes with a heady duty dipper, side impact protection, 9mm underbelly protection plates and a Turbo II engine air pre-cleaner. It also gets a level II FOPS cage, dipper ram protection and optional full length track guides. The high reach machine is a dedicated demolition rig, though it has a modular boom system to allow rapid changes between digging and demolition configurations.
695 Doosan is another manufacturer that has made big in-roads into the demolition industry in the UK, though not just with high reach equipment. It does produce super long reach versions of the DX225, DC255, DX300 and DX520, however the company's regular excavators have become a popular choice with contractors too, thanks to their durable built and relative low cost.
5895 New Holland also offers a range of ruggedised excavator specified for demolition applications including several long reach models.
As mentioned, demolition has become a specialised business. However the supply of machinery to carry out that work is no longer only in the hands of the specialist equipment builders. Regular excavator manufacturers have realised the potential in the market and have reacted with a far wider range of options and models to suit the needs of the demolition industry.
This trend looks set to continue, with only the ultra-high reach and real one-off machines being purely the preserve of the specialists. Which is good news for contractors, as they will have easier access to machines, attachments and most importantly back-up service.
Many of the ultra long boom machines are designed and built solely with high reach work in mind and may never wear a bucket. However, manufacturers are increasingly offering pinned booms, which allow operators to change between high reach equipment and heavy duty digging arms for clear-up work, increasing versatility.
Height and reach have for some years now been almost a holy grail for large demolition contractors and for the manufacturers supplying them. Ever longer booms, combined with greater counterweight, wider track frames and tilting cabs have allowed contractors to keep operatives well away from the area of work, literally at dipper arm's reach from the most dangerous areas of the site.
Traditionally the numbers involved have been relatively small, putting the design and engineering work firmly in the hands of specialist equipment builders such as the UK's
The last decade however has seen that mix change, with an increasing number of OEMs keen to get in on the act. This is partly due to the increased flexibility of manufacturing sites, which allow individual machine build specifications to be engineered within a production line, or more often on adjacent one-off lines that operate within the factory.
It is also due to the fact that manufacturers are working more closely with their customers, building to specific requirements rather than simply rolling out identical machines whatever the need on site.
Add into the mix the fact that those same manufacturers are in many cases the same firms that are offering the range of powered attachments that will be working with the carrier machine, and it is easy to see why they are almost all building demolition specification excavators these days.
Of course demolition spec need not mean a long boom and dipper arm, or even a three-piece boom. For many contractors demolition means strength and robust design, capable of handling hydraulic breakers and shears for up to eight hours/day. Excavators used on bridge demolition for example might need to work through the night with a breaker or cutting equipment to drop a motorway bridge within strict road closure or lane rental commitments. In these cases the demolition machine bears closer resemblance to a mass excavator, with a sturdy main boom and short dipper stick to carry heavy duty attachments, and tough cab and undercarriage protection to look after the operator and the machine.
They may need to carry frame-mounted falling object guards (FOG) on top of the standard ROPS/FOPS cab. Bolted-on side impact protection strips prevent damage as the machine's upper structure slews round, while double thickness heavy duty doors provide protection for engines and hydraulic components.
Down below the slew ring the machine will require full length track chain guards with heavy under plating beneath the slew area and around any hydraulic hoses and motors. The machine's internals will need to be protected too, with fine mesh screens preventing radiator cores from clogging and reversing fans capable of blowing dust and debris away from the cooling pack.
Having an established demolition offering is a similar story at
For the likes of Komatsu and fellow Japanese firm
Even manufacturers not traditionally known for their involvement in the heavy demolition industry have started producing their own high reach equipment and heavy duty demolition specification machines.
As mentioned, demolition has become a specialised business. However the supply of machinery to carry out that work is no longer only in the hands of the specialist equipment builders. Regular excavator manufacturers have realised the potential in the market and have reacted with a far wider range of options and models to suit the needs of the demolition industry.
This trend looks set to continue, with only the ultra-high reach and real one-off machines being purely the preserve of the specialists. Which is good news for contractors, as they will have easier access to machines, attachments and most importantly back-up service.