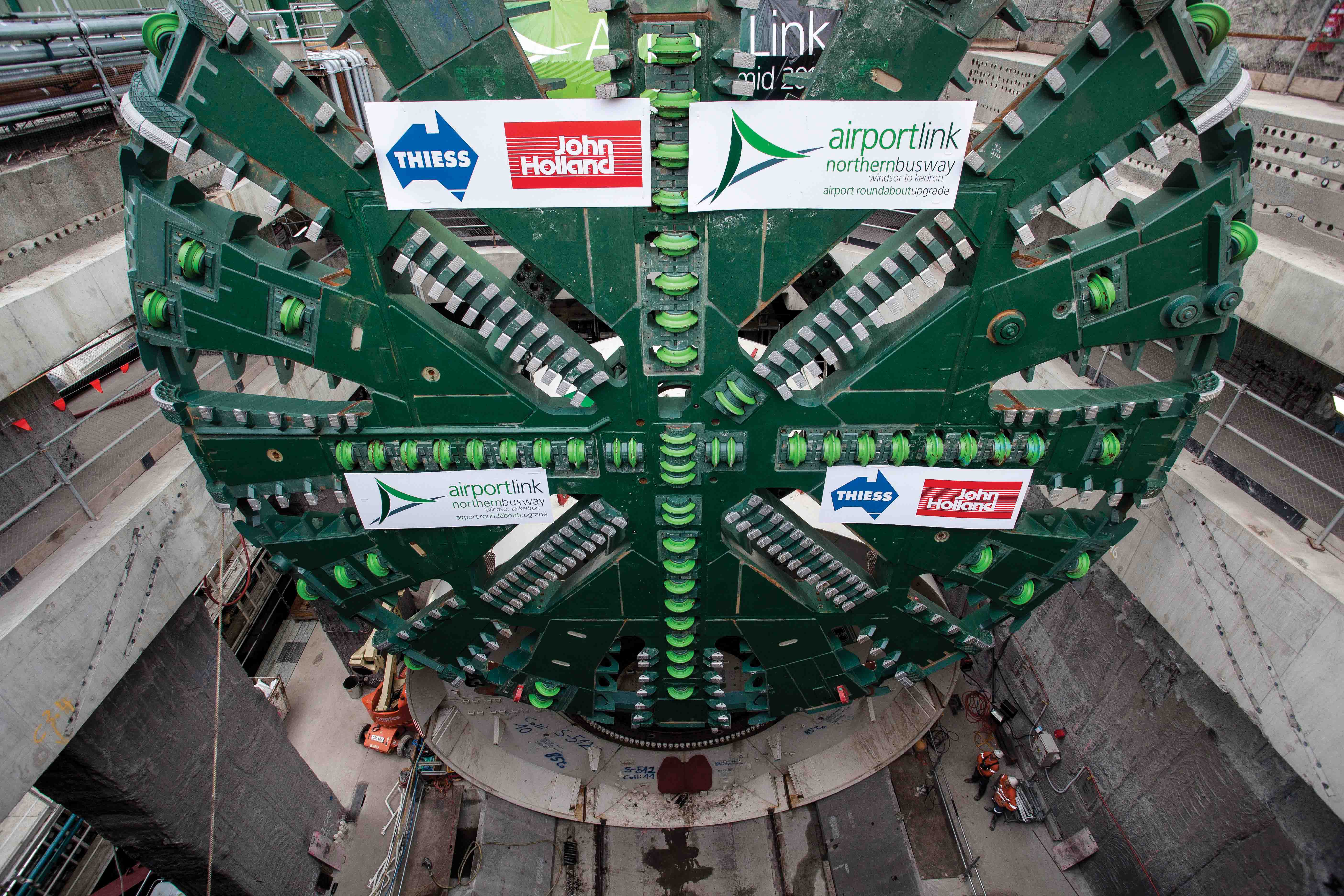
Tunnelling innovation is creating mountains of data for contractors and designers, delegates to a recent British Tunnelling Society (BTS) conference heard
Successful innovation in tunnelling techniques and technologies is creating more and more data, thanks to digitalisation. The question now is what to do with the vast amount of information and facts that is piling up. Just how useable is it, or can it be, asked many delegates to a BTS conference in London in October.
Manual analysis of data is quickly being overtaken by increasingly efficient and fast software, said Angus Maxwell, director of Maxwell Geosystems. Maxwell, an engineering geologist with more than 20 years’ experience in major underground excavation and construction projects in Europe and Asia, is founder and chief executive of Maxwell GeoSystems, with offices in Hong Kong and Singapore.
On one project, Maxwell estimated that it took personnel 10 man-years to do data analysis, all of which he said could have been done automatically with the right software in much less time. “We have to understand data to manage required design changes to increase project efficiencies and avoid costly mistakes and divergences,” he said.
At the same time – and importantly - the driver of a tunnel boring machine should have access to more up-to-date data, and in real time if possible, to better manage the drive.
More data is also coming in from sensors embedded in tunnel segments. Maxwell estimates that by embedding sensors into concrete and other works, up to 80% of wiring needed for conventional bending measurement hardware can be saved. The work space, especially if it is a confined area, is getting safer for workers.
His company was involved in the Brisbane Airport Roadway Link, Australia’s largest infrastructure project. Its close proximity to a dense urban centre and multiple tunnelling and excavation challenges made this a very complex project. It featured more than 10 simultaneous drives with multiple faces using tunnel boring machines, road headers with New Austrian Tunnelling Method linings and cut and cover techniques.
With so many shallowly founded structures above and with many of them highly sensitive to ground movement, it was clear that the proper management of instrumentation data linked with the construction progress and design prediction was going to be critical.
Maxwell worked with the onsite design teams to deliver reports and analytical tools through its proprietary data management systems. The resulting information was used to check on the tunnel works in real time. Ultimately Maxwell Data Systems became the data resource on which the daily ‘Permit to Tunnel’ was decided. The road tunnel was completed in 2012.
Non-destructive testing
The demand for non-destructive testing is increasing, said Aled Davies, senior tunnel engineer for the contractorA recent innovation is a method of early age strength testing for sprayed concrete linings – SMUTI - Strength Monitoring Using Thermal Imagery. SMUTI allows strength testing of the entire shotcrete lining in real time, they told delegates.
The technique to test the strength of sprayed concrete was successfully applied in a production environment for the first time in May this year. It was used by a joint venture between contractors Costain and Laing O’Rourke on behalf of London Underground, the UK city’s metro operator.
SMUTI uses a thermal imaging camera to track the temperature of concrete as it is sprayed to form the tunnel lining. Knowing this temperature history enables the engineers to calculate the amount of hydration that has taken place in the concrete and, therefore, its strength.
It is a significant step forward for health and safety, said Davies. “SMUTI allows operatives to directly monitor the strength development while remaining at a safe distance. This is a substantial improvement over the current method, which relies upon a small test panel being representative of the entire sprayed concrete advance to prevent personnel being at risk from sprayed concrete lining falls.
The magnitude of tunnel projects is getting larger and larger, meaning more complicated site work, from logistics issues for a main tunnel and those for associated and parallel tunnels during construction.
Bigger tunnels
And as the data mountain grows, so does the physical size of the tunnel, said Werner Burger, chief engineer for German TBM manufacturerThe largest TBMs are around 17.6m in diameter at the moment – 15 years ago this would have been an unheard of size, said Werner. Now, clients are suggesting 20m TBMs, but the leap in technology for associated equipment, maintenance and safety is too great, in his view. Better to increase the size gradually to learn best practice and design features. Importantly, the real issue remains the TBM’s frontal pressure, he added.
No matter how sophisticated the TBM is mechanically, the industry is still a long way from knowing 100% what lies in front of one its creations, said Werner.
Lok Home, president of US-based Robbins, another TBM maker, agreed that issues over ground support are making tunnelling operations more complex logistically. But advances in modular electronics for inspections have done away with hundreds of metres of cabling.
Home said he has seen a demand by clients for not only larger tunnels – especially road tunnels - but also ‘non-round’ tunnels. The challenge is to bore such tunnels effectively and efficiently as possible.
Along these lines, it is essential that more and more useful data is put in the hands that operate the machines, noted Lok. “We can collect now a lot of data, but very little of it is put to practical use,” he told delegates.
On the business side of TBM manufacturing, Lok said that companies need to be more accepting of buy-back packages as being called for by clients. This should not be an issue for major manufacturers to take back their machines, and isn’t for Robbins, he noted. Some of the Robbins machines have worked successfully on 10 or 12 projects.
NPA Satellite Mapping
Adam Thomas, InSAR surveying manager for NPA Satellite Mapping – part of Paris-headquartered CGG (Companie generale de geophysique) – presented a coloured map showing how London’s ground level has moved in recent years. The position of the tunnels for the rail link
Thomas also highlighted NPA’s work as part of the Live Land project which aims to use a variety of technologies including InSAR to forecast landslides and subsidence that can impact on transport networks. Live Land, funded by the European Space Agency, is conducting a pilot project in Scotland, monitoring sites considered to be at risk. If proved successful, it will be rolled out to other parts of the UK and Europe.
Interferometric Synthetic Aperture Radar (InSAR) uses images of the earth taken from satellites to calculate changes in ground conditions. The first satellite images date back to 1992 which means historic ground movement patterns can be seen. To create its InSAR maps, NPA processes data from satellites Sentinel-1A and Sentinel-1B, whose data comes free courtesy of the European Space Agency.
During construction, inSAR is used to provide baseline studies before work begins to show how the ground moves naturally. It pinpoints areas of movement which may need further investigation and also can monitor sites post-construction. One of its benefits is that it allows much wider areas to be monitored and far more cheaply than traditional surveying methods. As Thomas observed, it “highlights the unexpected”.