Sunderland sees a bridge slide into place and two bridges inch their way across a Polish highway
Slowly but surely, a 2,500 tonne section of a new bridge deck was eased out from the banks of the River Wear near Sunderland in northern England. It now straddles the water, pointing towards the opposite bank which it will eventually reach after another sliding operation likely to take place next year.
The project to build the New Wear Crossing is now halfway through with the first half of the steel deck b
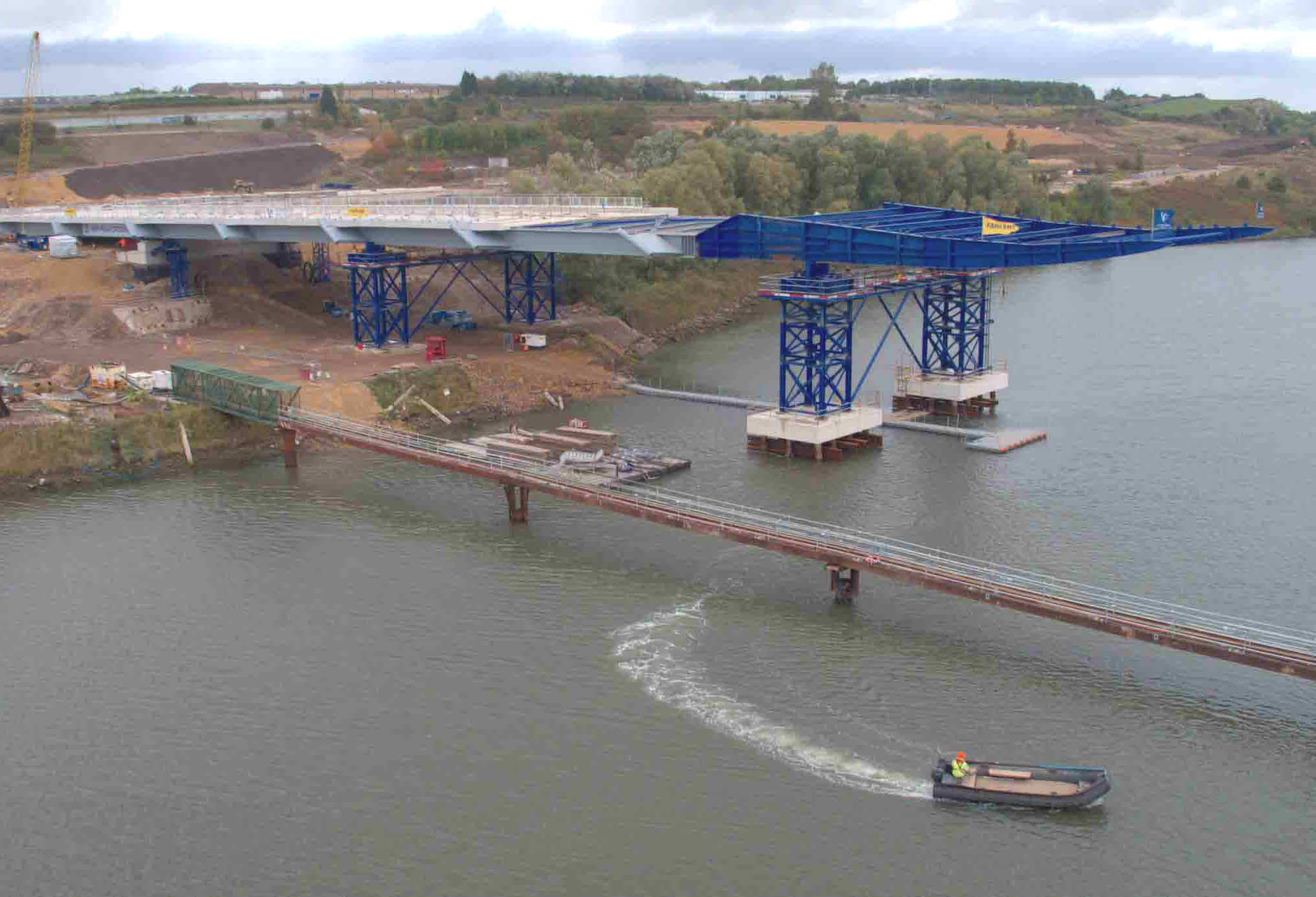
Sunderland’s new bridge slides into existence
RSSSunderland sees a bridge slide into place and two bridges inch their way across a Polish highway
Slowly but surely, a 2,500 tonne section of a new bridge deck was eased out from the banks of the River Wear near Sunderland in northern England. It now straddles the water, pointing towards the opposite bank which it will eventually reach after another sliding operation likely to take place next year.
The project to build the New Wear Crossing is now halfway through with the first half of the steel deck bridge poised mid-river. Completion of the bridge is expected in the spring of 2018.
This month, hydraulic jacks slowly pulled the first deck section – a 230m-long steel structure – around 120m out across the water during a seven-hour operation.
The deck is being held in place above the water on a series of temporary supports constructed within the riverbed. This enables assembly of the second section of bridge deck directly behind the first on the south side of the river.
Once the 105m high A-frame pylon, which is the centrepiece of the bridge, arrives on site early in 2017 and is raised into position, the extended bridge deck will then be pulled into position across the width of the river.
The permanent deck is 186m long and the temporary ‘nose’ - used to allow the deck to land on the temporary supports - is 37m long. The temporary ‘tail’ that connects the jacking system to the deck is 7m long.
Of the section’s 2,500 tonnes, around 1,350 tonnes consists of 212 precast concrete units that will form the road bed.
A further 256 concrete units, weighing 1,600 tonnes, will be added to the bridge deck before the next launch across the River Wear. The remaining 172 concrete panels will then be installed after the bridge deck is in its final position.
The project is on schedule, said Stephen McCaffrey, project director of the FVB joint venture, formed by1622 Farrans Construction and Belgium-based Victor Buyck Steel Construction which is delivering the project on behalf of Sunderland City Council.
FVB JV will be supported by their design team led by Buro Happold Engineering as well as Roughan & O'Donovan.
The process involves sections of bridge deck being prefabricated and prestressed off site or in a designated area on site. These sections are then transported to the work area where they are slid forward on prepared piers with the use of hydraulic devices.
This method is particularly recommended where ground conditions prevent the use of conventional shoring systems or when using them is inefficient and costly. The method is also suited where a span is particularly long and is characterised by fixed-size cross-sections such as being straight or of a constant radius.
Sections vary in lengths. One is 14m long, three stages are 24m each and the remaining ones 30m. In this case, hydraulic cylinders pull the superstructure onto the piers in 30cm increments.
Ulma designed and provided formwork for the construction of foundations, abutments, prefabrication positions and piers, as well as scaffolding to operate slide bearings. Formwork design and launching position for the sections has been based on moving the 30m section.
The formwork design is based on the universal MK System: ENKOFORM VMK and ENKOFORM HMK. The MK System’s extremely varied configuration options allows a wide array of applications, from heavy-load structures for civil engineering to lighter loads for buildings, but always using the same basic components. The use of the hydraulic system being offered by8607 ULMA Construction enables stripping and re-closing of formwork during one duty-cycle for the entire stretch, including the formwork for the bottom slab, external formwork and cantilevers.
This system enables an easy and safe detachment - lowering - of the entire external formwork structure over the length of about 30m, an equivalent of 700m² of formwork, and re-establishing it on the concreting position.
After each pour, with a hydraulic system the outer formwork was detached and prepared for the following cycle while the inner formwork units were rolled back for the next pouring. Applying the hydraulic system significantly facilitates and speeds up the assembling work.
For the construction of the top slab, a mobile table formwork was designed on the basis of MK-120 steel beams, VM timber beams and E-type push-pull props. Transport of the tables is by VR carriages. Ulma’s solution allows construction of 30m of deck within seven days.
Intermediate 12m-high piers are formed using the beam formwork ENKOFORM VMK. Safe working during erection of piers and the entire launching process is guaranteed by the use of working platforms as well as BRIO stairs.
Construction was divided into 29 stages. Two first and two last stretches were about 17m long, the remaining 25 segments were around 27m. The length of the manufacture position was 30m. Finished sections are slid using a stepper cylinder which enables lifting of the superstructure and moving it forward in 25cm increments.
Formwork systems for the box structure and cantilevers was the same as that for the E1 Bridge. For construction of the deck slabs, Ulma designed a mobile formwork on roller cantilevers based on MK-120 steel beams, elements of wall system COMAIN and E-type push-pull props.
Roller cantilevers are used only for supporting the top slab during the slide. The solution that was applied enables relocation of the formwork of the top slab in a form of one complete set onto the next section. RSS
Slowly but surely, a 2,500 tonne section of a new bridge deck was eased out from the banks of the River Wear near Sunderland in northern England. It now straddles the water, pointing towards the opposite bank which it will eventually reach after another sliding operation likely to take place next year.
The project to build the New Wear Crossing is now halfway through with the first half of the steel deck bridge poised mid-river. Completion of the bridge is expected in the spring of 2018.
This month, hydraulic jacks slowly pulled the first deck section – a 230m-long steel structure – around 120m out across the water during a seven-hour operation.
The deck is being held in place above the water on a series of temporary supports constructed within the riverbed. This enables assembly of the second section of bridge deck directly behind the first on the south side of the river.
Once the 105m high A-frame pylon, which is the centrepiece of the bridge, arrives on site early in 2017 and is raised into position, the extended bridge deck will then be pulled into position across the width of the river.
The permanent deck is 186m long and the temporary ‘nose’ - used to allow the deck to land on the temporary supports - is 37m long. The temporary ‘tail’ that connects the jacking system to the deck is 7m long.
Of the section’s 2,500 tonnes, around 1,350 tonnes consists of 212 precast concrete units that will form the road bed.
A further 256 concrete units, weighing 1,600 tonnes, will be added to the bridge deck before the next launch across the River Wear. The remaining 172 concrete panels will then be installed after the bridge deck is in its final position.
The project is on schedule, said Stephen McCaffrey, project director of the FVB joint venture, formed by
FVB JV will be supported by their design team led by Buro Happold Engineering as well as Roughan & O'Donovan.
Ulma in Poland
In Poland, a substantial number of bridges are being built up to 2020 using the incremental launching method. Many use systems designed by Spanish formwork specialist Ulma. The company's recently-designed incremental launching technology has been used on two bridges in Poland: the MS-6 Viaduct on the S5 highway and the E-1 Bridge on the S19.The process involves sections of bridge deck being prefabricated and prestressed off site or in a designated area on site. These sections are then transported to the work area where they are slid forward on prepared piers with the use of hydraulic devices.
This method is particularly recommended where ground conditions prevent the use of conventional shoring systems or when using them is inefficient and costly. The method is also suited where a span is particularly long and is characterised by fixed-size cross-sections such as being straight or of a constant radius.
E1 Bridge on the S19
The 476m-long E-1 Bridge is being constructed on the S19 between junctions wilcza junction (DK4) and Rzeszów Południe. The bridge design is straight-shaped in a horizontal projection with a longitudinal gradient of 0.8%. Superstructure box sections of the viaduct are 11m wide and 3.5m tall.Sections vary in lengths. One is 14m long, three stages are 24m each and the remaining ones 30m. In this case, hydraulic cylinders pull the superstructure onto the piers in 30cm increments.
Ulma designed and provided formwork for the construction of foundations, abutments, prefabrication positions and piers, as well as scaffolding to operate slide bearings. Formwork design and launching position for the sections has been based on moving the 30m section.
The formwork design is based on the universal MK System: ENKOFORM VMK and ENKOFORM HMK. The MK System’s extremely varied configuration options allows a wide array of applications, from heavy-load structures for civil engineering to lighter loads for buildings, but always using the same basic components. The use of the hydraulic system being offered by
This system enables an easy and safe detachment - lowering - of the entire external formwork structure over the length of about 30m, an equivalent of 700m² of formwork, and re-establishing it on the concreting position.
After each pour, with a hydraulic system the outer formwork was detached and prepared for the following cycle while the inner formwork units were rolled back for the next pouring. Applying the hydraulic system significantly facilitates and speeds up the assembling work.
For the construction of the top slab, a mobile table formwork was designed on the basis of MK-120 steel beams, VM timber beams and E-type push-pull props. Transport of the tables is by VR carriages. Ulma’s solution allows construction of 30m of deck within seven days.
Intermediate 12m-high piers are formed using the beam formwork ENKOFORM VMK. Safe working during erection of piers and the entire launching process is guaranteed by the use of working platforms as well as BRIO stairs.
MS-6 viaduct on S5
Ulma’s formwork system was next deployed for construction of the two-lane 746m-long MS-6 viaduct on the S5 express road between Korzesk and the Widawa Wrocław junction. Box section superstructures of the work were designed in arches of about 2,600m radii with constant transverse gradients and variable longitudinal gradients.Construction was divided into 29 stages. Two first and two last stretches were about 17m long, the remaining 25 segments were around 27m. The length of the manufacture position was 30m. Finished sections are slid using a stepper cylinder which enables lifting of the superstructure and moving it forward in 25cm increments.
Formwork systems for the box structure and cantilevers was the same as that for the E1 Bridge. For construction of the deck slabs, Ulma designed a mobile formwork on roller cantilevers based on MK-120 steel beams, elements of wall system COMAIN and E-type push-pull props.
Roller cantilevers are used only for supporting the top slab during the slide. The solution that was applied enables relocation of the formwork of the top slab in a form of one complete set onto the next section. RSS