Guy Woodford looks at vital bridge construction, repair and inspection projects in China, Europe, North America and Australia The Heron Road Bridge in Ottawa, Ontario in Canada is a vital link within the City’s transport network, as it crosses the Rideau River, which divides the east and west parts of the City. Constructed in 1966-1967, the Heron Road Bridge is approximately 275m long and includes six lanes.
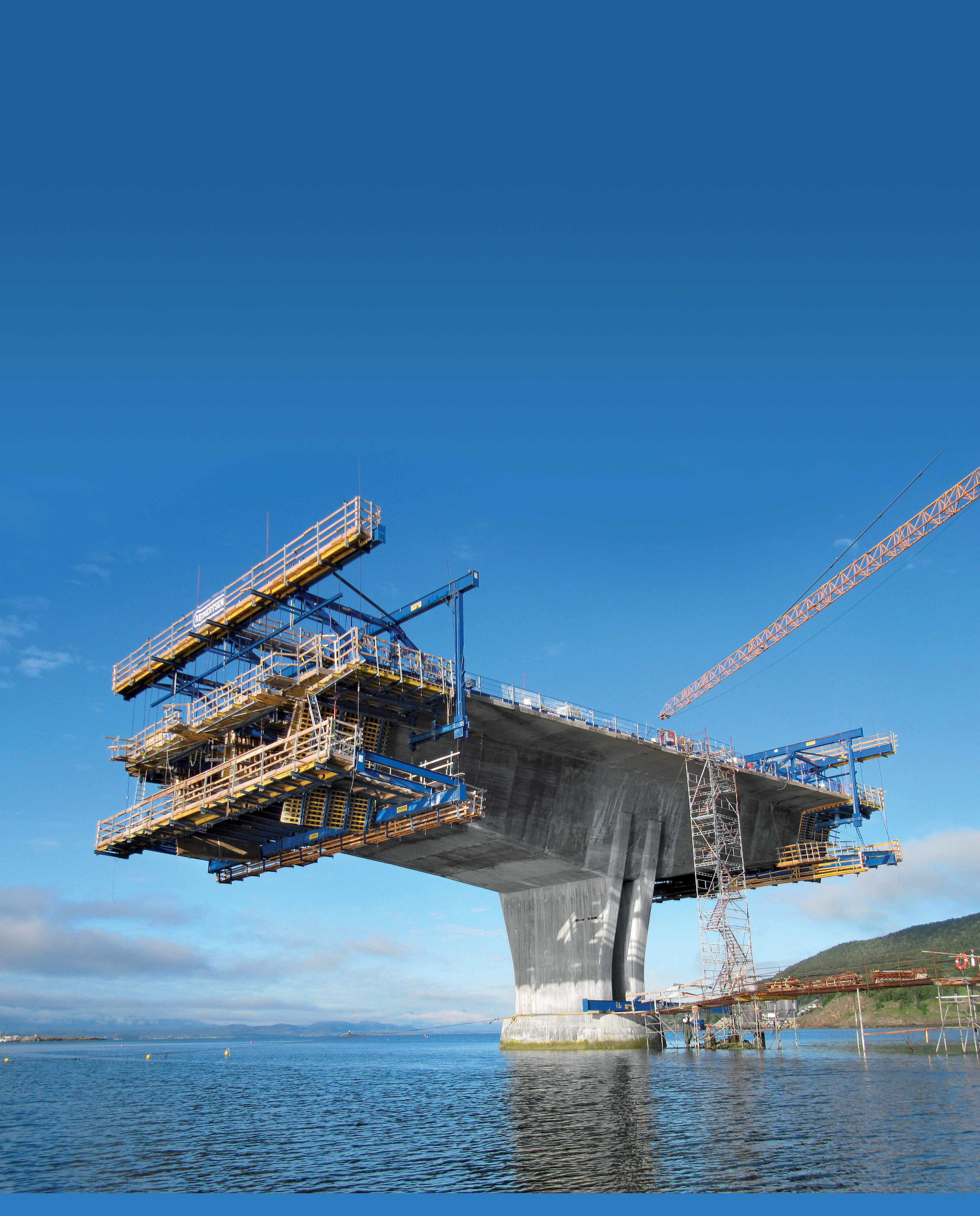
The modular design concept of Doka's cantilever forming travellers makes for highly efficient, cost-saving adaptability to the different cross-sections of a superstructure deck
Guy Woodford looks at vital bridge construction, repair and inspection projects in China, Europe, North America and Australia
The Heron Road Bridge in Ottawa, Ontario in Canada is a vital link within the City’s transport network, as it crosses the Rideau River, which divides the east and west parts of the City. Constructed in 1966-1967, the Heron Road Bridge is approximately 275m long and includes six lanes.An initial
As lead consultant, Delcan designed a major rehabilitation and seismic retrofit, which included innovations such as seismic isolation bearings; prototype bumper restrainers to prevent unseating of the suspended spans; and the first Canada-based usage of external post-tensioned carbon fibre reinforced polymer plates.
These innovations were said by Delcan to greatly reduce the overall cost of the rehabilitation, while assuring its structural viability and improving its long-term durability.
The objective of this project, as set by the City of Ottawa, was to upgrade the bridge “to the extent feasible, practical and economical in accordance with current standards, thus extending the service life of the bridge”. Delcan said it met the objective, while also achieving technical excellence through the successful completion of a number of design and construction elements.
These included the integration of design elements with agency requests and approval requirements; the management of traffic and pedestrian movements during construction; the incorporation of sustainable construction practices; the selection of rehabilitation strategies to minimise environmental impacts to the waterway; and employing design innovations where feasible in order to achieve cost and time savings.
Opening ahead of schedule in December 2012, Delcan said the project had made significant improvements to the economic, social and environmental quality of life by bringing this vital arterial to current codes and standards and enhancing public safety. The functionality of the bridge was also enhanced to accommodate transit priority, and improve pedestrians and cyclists’ experience along the bridge and adjacent pathways.
Examples on how the bridge has contributed to the enhancement of the economic, social and environmental quality of life include changing the roadway configuration from three general purpose lanes to two general purpose lanes, one reserved bus-only lane and adding a designated cyclist lane. Bicycle channels were also introduced at the stairs connecting the bridge to the pathway along the Rideau Canal and Colonel By Drive to help cyclists with transporting their bicycles along the stairs.
High quality bridge inspection units have also been in demand globally in recent months.
The Lantau Link is a 3.5km-long series of infrastructures, including a rail line and roads, linking Hong Kong International Airport to the urban areas of Hong Kong. It comprises the Tsing Ma Bridge, a suspension bridge linking Tsing Yi To Ma Wan Island; the Ma Wan Viaduct, a viaduct crossing Ma Wan; and the Kap Shui Mun Bridge, a cable-stayed bridge linking Ma Wan To Lantau Island. Adjacent to the Lantau Link is the cable-stayed Ting Kau Bridge.
Barin’s AB 23/SL unit being used at Lantau Link is mounted on to a four-axles
Said to be capable of carrying out its launching manoeuvre through suspended spans of Tsing Ma Bridge, the maximum horizontal underbridge of the AB23/SL is 23m. The model has a 26.5m overhead reach limit; a vertical depth underbridge of 30m; can overcome sidewalks up to 4.05m; and has a maximum 5.5m overcoming of bridge barriers. It also has a 250kg platform capacity.
The 58m-high cable-stayed bridge crosses the Yarra River and connects the centre of the city with Melbourne’s western industrial area. The longest distance between supports is 336m and the overall length is 2,582.6m – making it the third largest bridge in Australia. It had been renovated recently and now the under-bridge access unit will help to enable regular inspection and maintenance work on the underside of the bridge deck.
Australian norms and guidelines had to be considered during the engineering of the unit, especially taking into consideration the ranges of the Westgate Bridge. A crossing of 4m over the safety fence, which protrudes outward on the sides, can be reached.
The maximum horizontal range of the platform is 20m under the bridge and the maximum lowering depth is 8.4m. With a load capacity of 800kg, the spacious platform is said to offer enough area for several people at the same time.
The Rv 80 road building project aims to link the Tverland peninsula better to Bodø, the regional capital, around 1,200km north of Oslo.
Erected by Norwegian construction firm Reinertsen, the Tverlandsbrua bridge has a longitudinal gradient of up to 4.5% and is being built in the form of a spiral transition curve with varying radii. The bridge’s seven spans are borne by six piers of up to 13m in height – three of which are twins. Four of Doka’s Cantilever Forming Travellers (CFTs) are being used at the site.
For building the three bridge piers from which the CFTs were to start travelling, an exceptionally strong formwork solution was needed. The deployed Doka large-area formwork Top50 and Wall formwork FF20 systems are said to have impressively withstood a stormy endurance test.
The twin piers were each poured in a single casting step. To stabilise the formwork, Doka said platforms were built onto the foundations beneath the piers; with the high wind loads subsequently transferred into these platforms by spindle struts. CFT beams, from the cantilever forming travellers, and SL-1 system beams were used in building the platforms.
This equipment was also used to help construct the pier-heads. The beams rested on horizontally mounted Doka supporting construction frames, enabling them to sustain the load from the widely cantilevering pier-heads.
The pier-heads were poured in three casting steps: Large-area formwork Top 50 was used to form the bottom slab; Large-area formwork Top50 and Wall formwork FF20 to form the webs; and the Bridge formwork ParaTop, Large-area formwork Top 50 and Load-bearing tower Staxo systems were used to form the deck slab. Using ParaTop meant that no shoring was needed for the cantilever arm formwork – which also kept the equipment commissioning-quantity small.
The Tverlandsbrua bridge is due to be completed by the end of 2013.
During the bauma 2013 exhibition in Munich, Germany,
A supplement to the VARIOKIT heavy-duty shoring tower launched at bauma 2010, PERI said that during the new truss girder solution’s development it took into account load-bearing capacity of the tower and the challenging requirements of daily construction work.
The modular lattice system can be used for spans up to 40m and is said by PERI to have a very high-load bearing capacity. With the continuously adjustable telescopic support frame, PERI says all spans can be realised with centimetre accuracy. Furthermore, the calotte bearing allows easy adaption to the longitudinal and lateral inclinations of the superstructure. The heavy-duty truss girder can be quickly assembled by fitting pins.
PERI claims the compatibility with the VARIOKIT heavy-duty shoring tower through the Main Beam VRB provides ideal solutions in the heavy-duty shoring sector. Meanwhile, the optional PERI UP scaffolding in the bottom section provides, says the company, totally safe working conditions.
“We are going way beyond capacity of existing systems,” said Bernhard Lindner, product management civil engineer at PERI. “We can go up to 3,000kNm as a maximum bending moment. We want to work on spans up to 35 metres as a standard use. We also intend to go up to 40 metres.”
Lindner said Eastern Europe and North America were likely to be strong markets for the new heavy-duty truss girder solution. “We also have some clients from Serbia. They have looked at the solution and said, "We want to redesign our bridge to make it more suitable for your system."
In combination with the VARIOKIT heavy-duty shoring tower, the new VARIOKIT heavy-duty truss girder will be piloted at T4 – a 390m arched bridge being used to close the gap between Paradisia and Tsakona on the 160km A7 motorway in Greece. The bridge is due to be completed in early 2014.
Stirling Lloyd’s Bridgemaster waterproofing and anti-skid system was used as part of a major refurbishment project on the Weymouth Lifting Bridge, in Weymouth, south-west England, after an inspection by Dorset County Council highlighted serious wear and tear and concerns over surface break-up.
Bridgemaster comprises a primer, a methyl methacrylate resin-based screen combined with an aggregate overscatter and a final sealer coat.
The system is said by
Design consultants
The refurbished bridge was expected to have a working life of 120 years and include the replacement of the entre deck plate and all steel hollow box section (SHS) members. The new deck structure design had to consider the lifting capacity required and the appropriate weight distribution.
To improve durability, a 6mm-thick deck plate was to be used which would be supported on 230 transverse members that were to be welded to the existing rolled steel joists at 150mm centres.
With a quick turnaround essential, and with intense pressure on the Council to keep Weymouth Lifting Bridge’s closure to a minimum, Stirling Lloyd completed the application of the Bridgesmaster system to the 380m² deck within just three days, ahead of schedule.