Hydrodemolition surface preparation keeps Liberty Tunnel rehabilitation project on schedule in Pittsburgh. The Pennsylvania state Department of Transportation selected hydrodemolition surface preparation for the US$18.8 million rehabilitation of Pittsburgh’s Liberty Tunnels. Time was of the essence to complete the project on deadline without penalties and hydrodemolition was selected as it offered a fast and cost-effective method to prepare the tunnel walls for a new, shotcrete surface.
This methods off
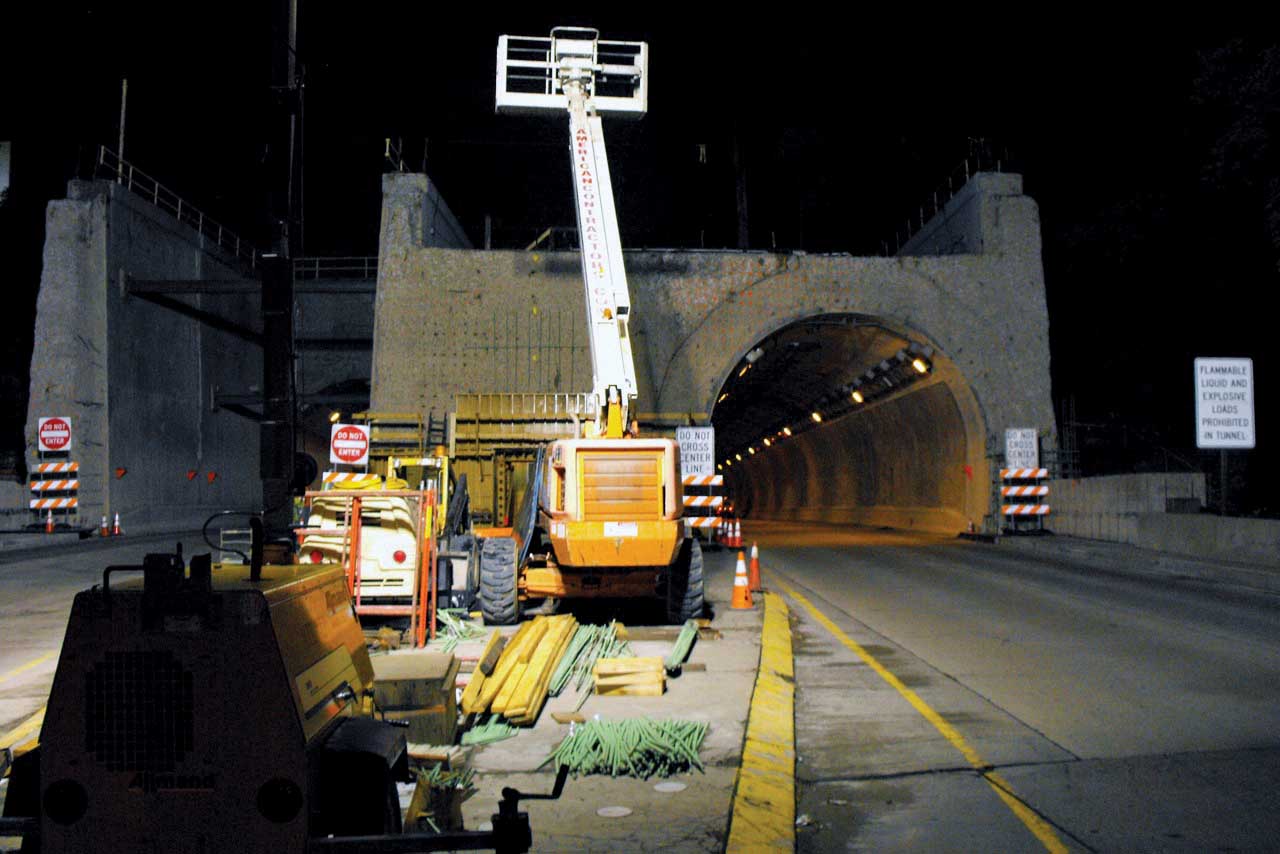
Two Conjet Robot 363 hydrodemolition machines have been adapted to suit the curvature of the horseshoe shaped walls of the twin Liberty Tunnels
Hydrodemolition surface preparation keeps Liberty Tunnel rehabilitation project on schedule in Pittsburgh
The Pennsylvania state Department of Transportation selected hydrodemolition surface preparation for the US$18.8 million rehabilitation of Pittsburgh’s Liberty Tunnels. Time was of the essence to complete the project on deadline without penalties and hydrodemolition was selected as it offered a fast and cost-effective method to prepare the tunnel walls for a new, shotcrete surface.
This methods offers quick concrete removal and easy clean-up, meaning that contractors can work faster than with conventional concrete removal methods. This allows the team to work within a narrow time slot and avoid heavy penalties for not opening the tunnel to traffic when required. In addition, no damage or cracking of the tunnel walls occurred using hydrodemolition, as may be the case when breaking equipment is employed instead.
The project is intended to increase the service life of the Liberty Tunnels as well as reduce maintenance cost, increase visibility for drivers and repair deterioration from 90 years of wear and tear. And the project has been extensive as the area targeted for refurbishment equated to 20,000m2.
Since the hydrodemolition began, commuters have experienced few delays as this method makes it possible to remove concrete during a night time closure from 10pm to 6am. The specialist work has been carried out by specialist subcontractors HTNE Hydrodemolition Service and Hydro-Technologies. Meanwhile Swank Construction is general contractor for the Liberty Tunnel project.
The twin Liberty Tunnels measure 1,795m long and allow motorists to travel between the South Hills of Pittsburgh and the city, through Mount Washington. There is an inbound tunnel and an outbound tunnel, each with two lanes of traffic and this link was constructed between 1922 and 1924, with the connection having aged since that time. When planning began for the repairs it was clear from the outset that the work would be difficult as the link carries around 48,000 vehicles/day.
Every night the hydrodemolition equipment and crews have had to enter the tunnel as soon as it shut the closure and get as much done as possible before shutting down the equipment, cleaning up debris, then exiting before the 6am opening. If the tunnel had not been opened by 6am, the contractor would be assessed liquidated damages of US$7,800/hour until the tunnel was opened to traffic. That left only eight work hours/night to carry out the work.
The method uses a high-pressure water jet operated by a hydrodemolition robot. On the Liberty Tunnel project, two Conjet 363 vertical robotic units performed partial depth, selective removal hydrodemolition on the tunnels’ vertical wall horseshoe profiles that have 4.42m posted vertical clearance. The186 Conjet 363 vertical hydrodemolition machines have water jets controlled by a technician over the entire surface of the tunnel walls. The flow rate, pressure, dwell time and cutting head are computer-controlled to provide the ideal settings required to selectively remove deteriorated concrete while leaving the sound concrete intact.
The Conjet robot is said to be versatile and can carry out high-speed, selective, vibration free removal of damaged concrete. Powered by an 11kW electric motor, the Robot 363 unit can handle the rotors and the oscillation tools efficiently. It can withstand reaction forces working with high-pressure pumps rated at up to 550kW, while the removal area can be as wide as 2m. The machines are also versatile and can also make two separate cuts with different depths and widths simultaneously. After the units have carried out material removal, the surface is water-blasted to provide a high quality surface ready for shotcreting.
Hydrodemolition in the US was initially used on bridges, but is now used on bridge decks, or wherever deteriorated, reinforced concrete has to be removed by the owner to rehabilitate and preserve a structure. And in the US, the2535 Pennsylvania Department of Transportation is using hydrodemolition for a wall rehabilitation project on State Route 51.
The Pennsylvania state Department of Transportation selected hydrodemolition surface preparation for the US$18.8 million rehabilitation of Pittsburgh’s Liberty Tunnels. Time was of the essence to complete the project on deadline without penalties and hydrodemolition was selected as it offered a fast and cost-effective method to prepare the tunnel walls for a new, shotcrete surface.
This methods offers quick concrete removal and easy clean-up, meaning that contractors can work faster than with conventional concrete removal methods. This allows the team to work within a narrow time slot and avoid heavy penalties for not opening the tunnel to traffic when required. In addition, no damage or cracking of the tunnel walls occurred using hydrodemolition, as may be the case when breaking equipment is employed instead.
The project is intended to increase the service life of the Liberty Tunnels as well as reduce maintenance cost, increase visibility for drivers and repair deterioration from 90 years of wear and tear. And the project has been extensive as the area targeted for refurbishment equated to 20,000m2.
Since the hydrodemolition began, commuters have experienced few delays as this method makes it possible to remove concrete during a night time closure from 10pm to 6am. The specialist work has been carried out by specialist subcontractors HTNE Hydrodemolition Service and Hydro-Technologies. Meanwhile Swank Construction is general contractor for the Liberty Tunnel project.
The twin Liberty Tunnels measure 1,795m long and allow motorists to travel between the South Hills of Pittsburgh and the city, through Mount Washington. There is an inbound tunnel and an outbound tunnel, each with two lanes of traffic and this link was constructed between 1922 and 1924, with the connection having aged since that time. When planning began for the repairs it was clear from the outset that the work would be difficult as the link carries around 48,000 vehicles/day.
Every night the hydrodemolition equipment and crews have had to enter the tunnel as soon as it shut the closure and get as much done as possible before shutting down the equipment, cleaning up debris, then exiting before the 6am opening. If the tunnel had not been opened by 6am, the contractor would be assessed liquidated damages of US$7,800/hour until the tunnel was opened to traffic. That left only eight work hours/night to carry out the work.
The method uses a high-pressure water jet operated by a hydrodemolition robot. On the Liberty Tunnel project, two Conjet 363 vertical robotic units performed partial depth, selective removal hydrodemolition on the tunnels’ vertical wall horseshoe profiles that have 4.42m posted vertical clearance. The
The Conjet robot is said to be versatile and can carry out high-speed, selective, vibration free removal of damaged concrete. Powered by an 11kW electric motor, the Robot 363 unit can handle the rotors and the oscillation tools efficiently. It can withstand reaction forces working with high-pressure pumps rated at up to 550kW, while the removal area can be as wide as 2m. The machines are also versatile and can also make two separate cuts with different depths and widths simultaneously. After the units have carried out material removal, the surface is water-blasted to provide a high quality surface ready for shotcreting.
Hydrodemolition in the US was initially used on bridges, but is now used on bridge decks, or wherever deteriorated, reinforced concrete has to be removed by the owner to rehabilitate and preserve a structure. And in the US, the