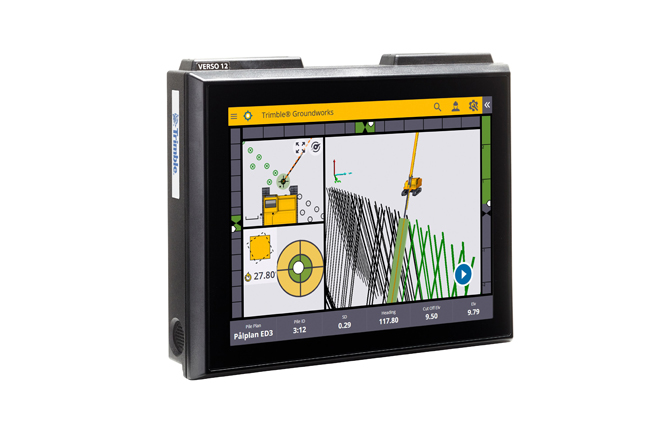
“Engineered for ease of use, Trimble Groundworks features an updated, intuitive user interface designed for construction environments,” said Scott Crozier, general manager for Trimble’s Civil Engineering and Construction Division. “Contractors can achieve centimetre-level accuracy with stakeless navigation, which reduces rework and decreases the need for personnel working near the machine during operation.”
The system features a touchscreen control, with full colour graphics and is said to be easy to learn. The large screen is also said to be easy to read, even in bright sunlight, while the firm says that operators can personalise the interface to match their workflow. In addition, a variety of configurable views make it easier for users to achieve maximum productivity. The software is designed for full integration with other solutions in the Trimble Civil Engineering and Construction portfolio to make company-wide training faster and easier.
The Trimble Groundworks system is said to give contractors the ability to drill at the specified location and to the required depth, orientation and inclination angle, with a higher degree of accuracy than with conventional methods. This is a key issue as being able to drill blastholes to the specified design more accurately will result in better rock fragmentation and lower hauling costs. This also minimises the problems of excess fines or overbeak, while providing a flatter floor to the blasted area. These better results can be achieved by optimising drill hole spacing, angles, and the location of the machine for a more even blasting pattern.
Minimising the need for stakes and construction surveying, Trimble Groundworks can help promote jobsite safety by reducing the number of people working near the machine while drilling. Also, avoidance zones can be set to keep operators from entering hazardous areas. With Trimble Groundworks, machines can operate 24 hours/day and 7 days/week in almost any conditions, decreasing the chance of delays due to darkness or inclement weather.
Meanwhile, the accuracy of the system enables contractors to increase operational efficiency and reduce surveying costs associated with staking and as-built checks. Accurate positioning in Trimble Groundworks can ensure that navigation time between piles is reduced. Less time moving the machine and more time piling maximises daily production, which can result in increased revenue.
Built-in, automated quality assurance and quality control reporting includes the capture of start and end positions, time and elevation as well as actual embedment depth, blow count reporting, and inclination and orientation control. In addition, the system logins allow managers to filter reports by operator for better accountability, production optimisation and forecasting.
Using the system for piling work allows this portion of a construction operation to be optimised and incorporated into BIM practices. Data can be analysed and recorded as part of the site model for future reference.