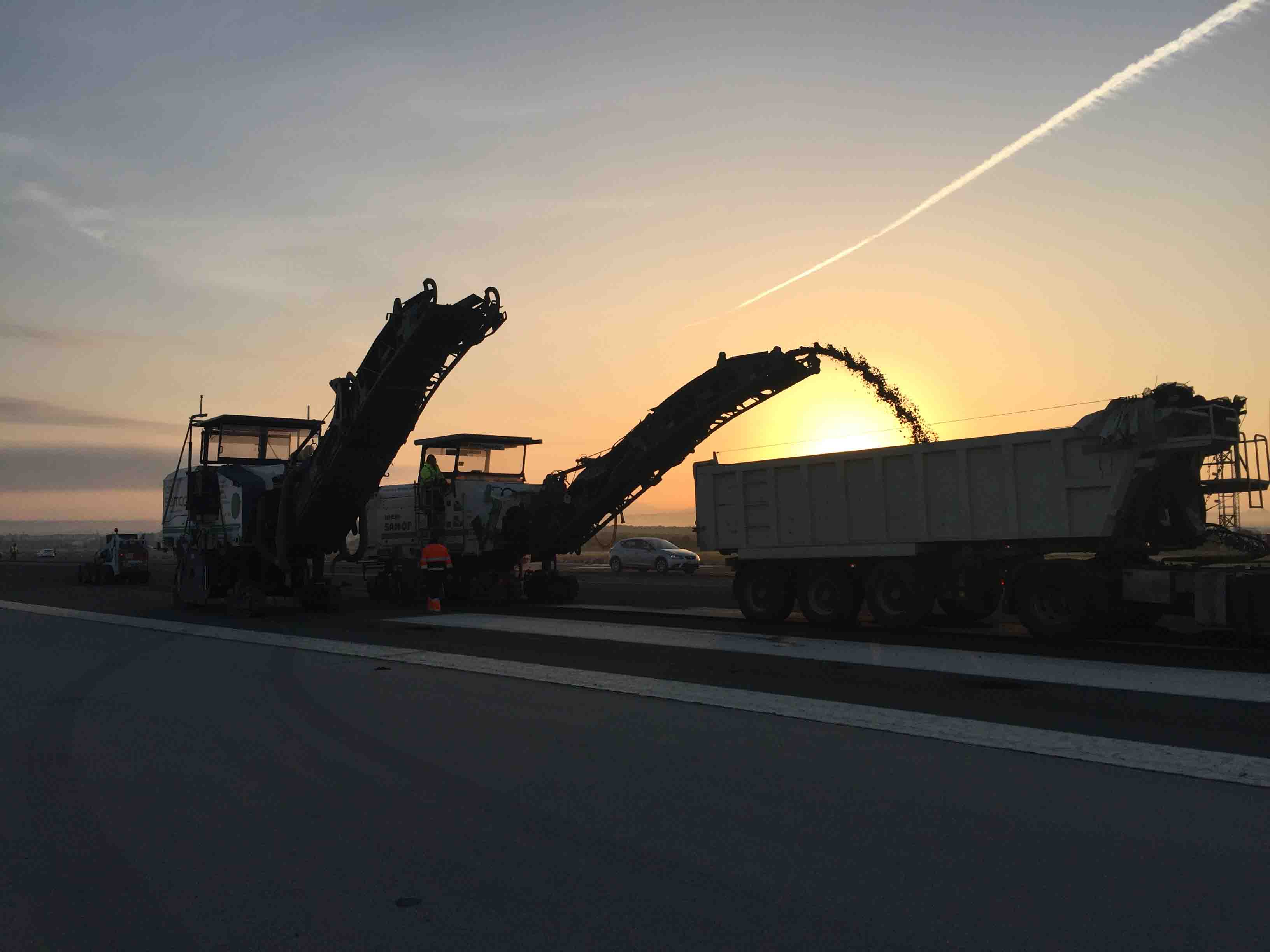
The Spanish island has long been a major tourist destination and its airport has been struggling to cope with demand, handling around 26 million passengers in 2016. Palma de Mallorca Airport is the third largest airport in Spain and during the peak summer holiday period, the massive influx of tourists makes it one of the busiest airports in Europe.
In November 2016, upgrade work for the airport’s southern runway commenced. The work has been carried out by a consortium called UTE Regeneración Pista Sur, which comprises the contractors MAB Obras Públicas and CONELSAN.
The consortium partners were given a specific task to carry out, correcting the slope of the runway and exchanging the horizontal and vertical runway signals. Because of the specialised nature of the milling job, this portion of the work was subcontracted to Iber Samop, which employed a PaveSmart 3D system from
The milling job was carried out by a
According to Iber Samop, this high rate of productivity could not be achieved without the use of up to date machine control equipment to guide the milling machines and deliver better quality results.
To meet the CS-ADR-DSN regulation covering the runways would have been difficult using conventional methods and systems. Iber Samop pointed out that with a profile milling job, the layer thickness can vary continuously. This can range from 10mm to 50mm just a few seconds later, according to the design. However, the firm said that the required evenness can be achieved by using the latest machine control technology to deliver an automated work process. The manual work process would require a surveyor in front of the machine at all times who would be busy measuring and marking the target milling thickness on the ground. But by using a machine control solution for milling, the human error in the conventional process can be eliminated and also allow for a safer working environment.
The work was carried out during a period of low air traffic volumes for the airport, so as to minimise delays for passengers. And with the runway now upgraded, Mallorca’s airport should be able to handle the 10% increase in passengers anticipated.