Innovative uses are being made of GPS technology, Mike Woof reports. US firms Creighton Manning Engineering and Delaney Construction have made a novel use of GPS technology in a project for the Route 85 Slingerlands bypass extension in the US.
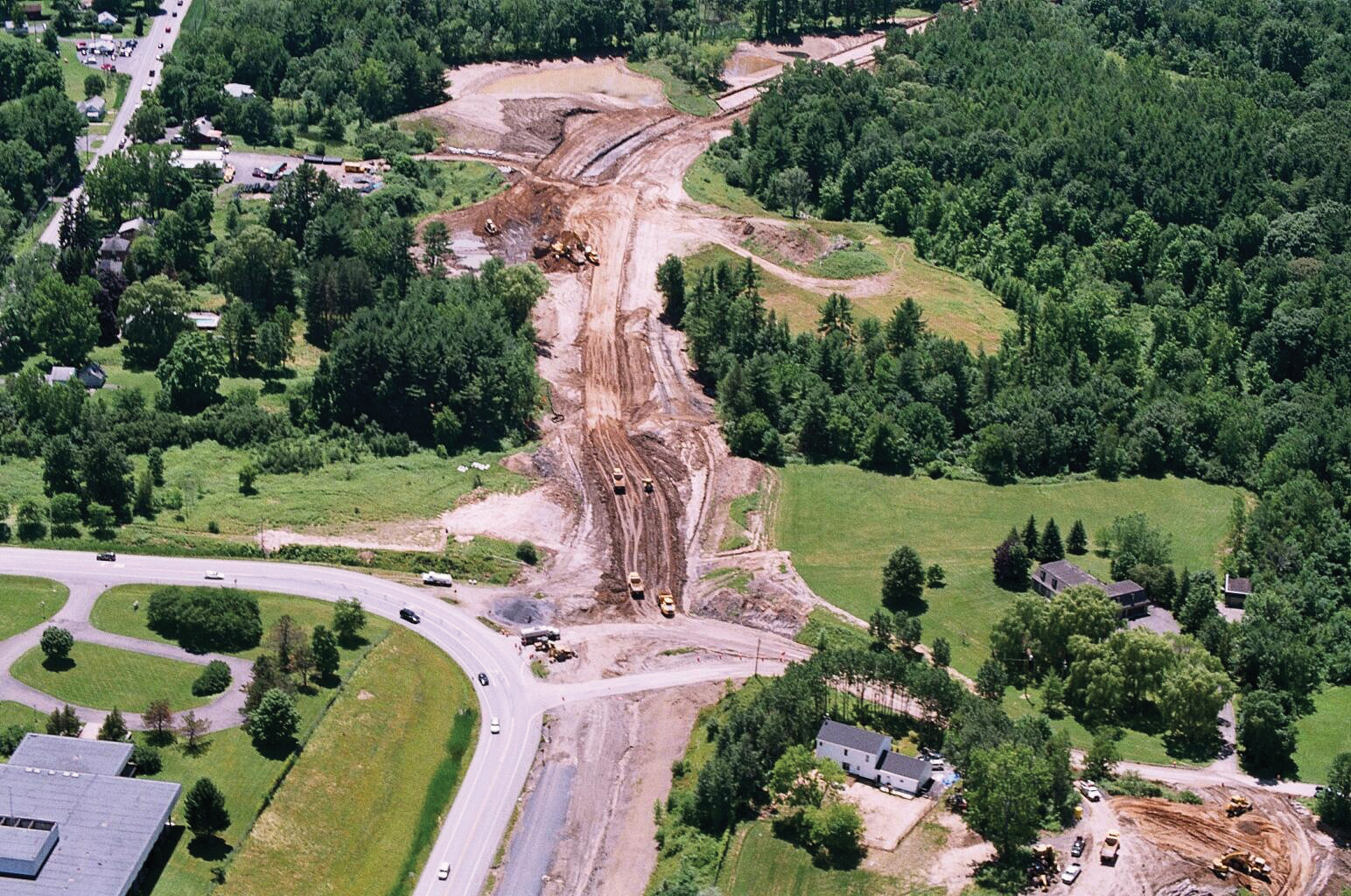
The stakeless method of surveying was particularly useful for contractor Delaney Construction, making notable cuts in the time required compared with conventional methods
Innovative uses are being made of GPS technology, Mike Woof reports
US firmsWith the need for the work apparent, the
Creighton Manning provided contractor Delaney Construction with the 3D model, which was downloaded directly into the GPS systems used on the machines. The two firms worked closely to ensure that this high technology approach worked, realising significant gains in efficiency once some initial bugs had been worked out.
Karl Detrick CADD manager and principal engineering technician at Creighton Manning played a pivotal role in the project. Detrick said that Creighton Manning used Bentley packages to develop 3D digital terrain models (DTMs) and estimating software to meet the project goals. The model had to be drawn up in 2D and 3D, but with a view to reducing the size of the construction plan, allowing the contractor to use GPS and automated grading equipment.
Use of the software required training and high level of expertise, so Creighton Manning worked closely with Bentley. The work was complex and involved a number of other factors too, such as wetlands mitigation.
The roundabout and storm water detention basins were not straight-forward to model according to Creighton Manning and virtually every kerb line needed a separate alignment. The firm set out proposed vertical and horizontal alignments, then used the roadway modeller tool for all the typical roadway area. For the roundabout tie-ins, indvidual aligments had to be used for all kerb edges and splitter islands. Because the earthmoving work was carried out on a stakeless basis and without conventional detailed plans drawn on paper, the horizontal control plan was used as a digital key, pointing the contractor to the correct inroads alignment.
The proposed horizontal and vertical geometry was provided in digital format to Delaney Construction as supplemental information. As part of the pilot project, Creighton Manning left out multiple tables with horizontal control data as this eliminated the risk of human error as well as the time required to generate them and it resulted in considerable time savings during design. Creighton Manning worked with NYSDOT to fine tune its data and Detrick said that this made for a tight estimate, with the contractor's own estimates proving to be very similar.
With all of the parties involved in the project sharing data, work-flows were improved and it proved critical to ensure the latest design information was passed between all the team members. There were numerous benefits and for Delaney Construction, the field-verified model was provided by the GPS tools. The model was used as designed and was stamped plans as the legal document for the work.
Combining the GPS system with a total station provides greater accuracy in the horizontal and vertical planes, a method that was used to improve performance. With this set-up there was no need for key sheets, grade stakes or a grade foreman and all the surveying work was carried out by single person. There was also no need for interim surveying and no lost time from waiting for an interim survey.
The site features sand and wet clays and most excavation was carried out using GPS-equipped dozers, while excavators were used to load trucks and Delaney Construction was able to shift 3,138m3 in each 12 hour shift. Monitoring progress was simpler and there was no need to count truck loads to provide a rough estimate, while the quantities of dirt being moved could be monitored from the data received back from the earthmoving machines, compared with the 3D model and computed using a tool on the design software. While a project of this size would normally require two inspectors to monitor progress, only one was needed and the set-up allowed easy checks of alignment and grade of any element. Other benefits included a reduction of tabular horizontal control information, improved quantity take-off, increased drainage automation, a cut in CAD design time and a reduction in errors from duplication of data.
It is of note that while the start of the construction work was delayed by seven months due to permit issues, the contractor was still able to meet the original schedule through the time-savings provided by the technology. For Creighton Manning, drawing up a detailed model added in 3D added around 20% to the time generally required for the deign of a conventional project but the firm says that much of this was down to the learning curve that resulted from using the software package to its full.
The technology boosted earthmoving productivity considerably and using the DTM and GPS-based survey and machine controls, Delaney Construction moved over 200,000m3 of earth in a relatively short time. At the same time as increasing productivity, the technology also delivered a better quality of work through improved accuracy, with no need for any reworking.
Following the successful use of this approach NYSDOT intends to allow contractors and designers to use 3D software models to run GPS machine control packages. This move is a significant step as it allows a 3D design to be used as a document of record for NYSDOT projects.
Detrick said that this innovative approach does requires a mid-high level of expertise to use the technology effectively, but that good training of an experienced team will provide an effective solution. Because of its innovation, the project was a winner in the Roads category of the Infrastructure Best Practices Symposium and Awards event run by construction software specialist Bentley Systems.