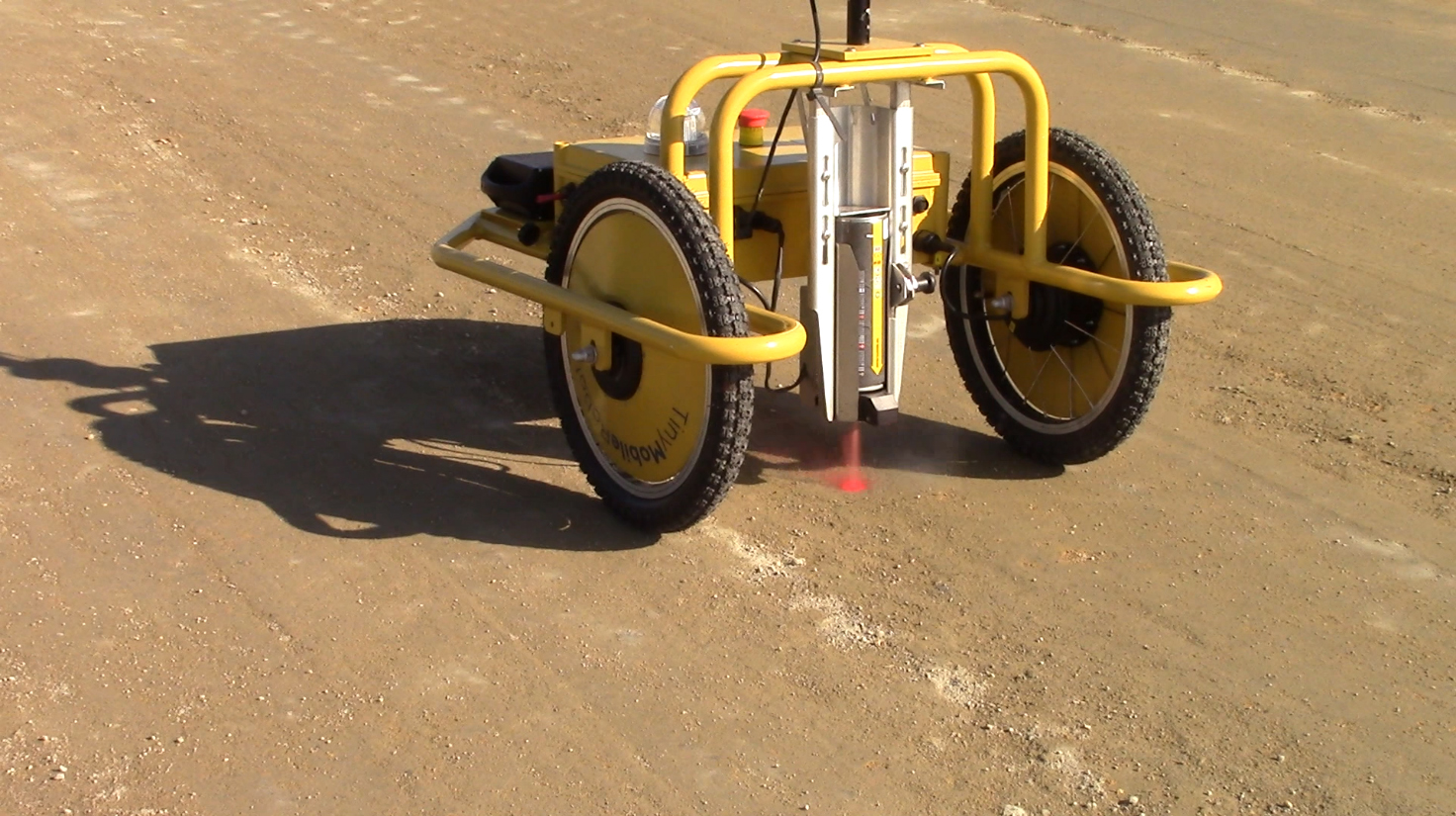
Small is beautiful, especially when it comes to robots, explains Jens Peder Kristensen, director of Danish company TinyMobileRobots
With the increased functionality of outdoor robots, the market for autonomous robots as a replacement for human work has widened. The human touch is still needed when dealing with terrain that is difficult to navigate or with a crowded construction site. But where extensive marking or height measurement is needed in flat areas, autonomous robots can operate with the same precision as a manual surveyor - but three times faster.
Indeed, while manual surveying requires a labourious search for the right coordinate, the robot simply employs an algorithm to optimise its movements. Since the robot locates coordinates at about three times the speed of a surveyor, it does not require many coordinates to locate before using the robot becomes profitable.
Additionally, unlike humans, robots can work for as long as the task requires, and won’t break for coffee! It might, however, need a change of battery every eight hours or so. During large tasks that can involve hundreds or perhaps even thousands of coordinates, it can tirelessly execute the task with many fewer mistakes than a surveyor.
In 2014, a scientist at the University of Southern Denmark collaborated with Larsen’s Land Surveying Service (Larsens Landmålerservice) to develop a prototype to assist in height measurements. The resulting fully functional prototype was not very robust; TinyMobileRobots then took over development. The first version was ready for users in 2015, followed by more users after some refinements last year.
I, Robot
In autumn of 2016, two versions of the robot were ready for sale. The version with a built-in GPS is intended for pre-marking duties. The other version, for land surveying companies, is designed to accept a customer-installed GPS receiver, such as those made by
The robot is controlled by a high-precision GPS - a network RTK corrected GNSS receiver - that outputs a position with an accuracy of 1-2cm. The user’s GPS continuously provides the robot with its updated position by use of an NMEA formatted signal.
When conducting as-constructed surveys, height has to be measured with far greater accuracy than is possible with a high-precision GPS. To enable this, a prism is mounted below the robot’s GPS antenna (see figure 2). The prism is used in collaboration with a total station to allow the user to measure height to within a few millimetres.
The robot navigates to horizontal positions by data from the GPS unit. But it comes to a full stop for a few seconds at each coordinate to allow for an accurate measurement with the total station. Depending on the equipment, the user can choose to manually activate the total station when the robot is at a full stop or the user can program the total station to automatically measure whenever it detects that the robot is at a full stop. In some cases, it is also possible to let the robot drive continuously while it steadily collects data with the total station.
Larsen’s Land Surveying Service has been using the robot to monitor newly laid asphalt on roads and ramps during the night in order to keep the project on its tight schedule. As well, Spotland Surveyors has used the robot to monitor the single layers of asphalt during bridge construction. This requires a large number of coordinates, since measurements in many cases must be conducted within a grid of 0.5m. The robot greatly reduces the time compared to manual measuring.
A built-in setting for parking lot pre-marking allows the robot to collect three coordinates in the field and indicate the angle and the number of rows and columns in the robot’s settings. The robot also has built-in support for the marking of lines and arcs. Once again, the user can collect two coordinates for a line or three coordinates for an arc and the robot will subsequently pre-mark these elements.
The robot is constructed of lightweight material and it weighs in at 18kg without the battery, which is likely to add 4kg. A remote control reconfigures the robot, controls it in manual mode and stop it immediately in case of emergency. The user programs the robot by storing coordinates on a USB stick for insertion into the robot which also supports all the world’s commonly used coordinate systems.
Importantly, customised equipment can be mounted onto the robot according to specifics of the task. The user can mount a GPS and prism for positioning and measurement on top of the robot. Also, a spray paint aerosol can actuator or a laser can be mounted underneath for tasks that involve pre-marking.
Since the robot compensates for the potential slope of the surface, it will always spray exactly at the given coordinate, even if the surface has a slope that prevents the GPS receiver from being positioned exactly above the spray paint can’s marking coordinate.
Marking/Premarking | Elaboration |
---|---|
Road Stripes | Premarking: If positions of road stripes are given by coordinates, marking can be done by an on-board high-precision GPS. |
Cutting Marks | To ensure concrete can handle temperature shifts, it must be cut in a specific pattern. Using coordinates, the robot pre-marks the cutting outline to ensure precise cutting. |
Abrasive Marks | If there are any mistakes in speed bumps or other structures, the robot can mark when the structure needs to be grinded. |
Parking Lots | A built-in parking lot function simplifies pre-marking. |
Spotland Surveyors has used the robot to pre-mark road stripes during expansion of the Køge Bugt motorway in Denmark. The client digitally provides the location of the road stripes and the robot pre-marks both the temporary road stripes that are necessary during temporary detours, as well as permanent road stripes for when the road is opened.
Spotland usually pre-marks with a distance of 5m which limits the number of coordinates that are marked. Using the robot, Spotland has simultaneously improved its efficiency and enhanced its employees’ safety, thanks to increased protection from machines and general traffic on the motorway.
Larsen’s Land Surveying Service has used the robot for a variety of marking tasks, including the pre-marking parking lots, airport runway stripes and cutting stripes. In late 2016, pre-marking cutting stripes was conducted during construction of a motorway between the Danish cities of Herning and Holstebro. Initially, cutting stripes were not supposed to be pre-marked, but the robot’s efficiency made the pre-marking feasible (see figure 1).
Height measurement
When conducting as-constructed surveys, height has to be measured with far greater accuracy than is possible with a high-precision GPS. To enable this, a prism is mounted below the robot’s GPS antenna (see figure 2). The prism is used in collaboration with a total station to allow the user to measure height to within a few millimetres.
The robot navigates to horizontal positions by data from the GPS unit. But it comes to a full stop for a few seconds at each coordinate to allow for an accurate measurement with the total station. Depending on the equipment, the user can choose to manually activate the total station when the robot is at a full stop or the user can program the total station to automatically measure whenever it detects that the robot is at a full stop. In some cases, it is also possible to let the robot drive continuously while it steadily collects data with the total station.
Measurement Task | Elaboration |
---|---|
Road | A road’s slope degree to encourage water runoff must be measured every few meters and there are usually three or four layers of asphalt to be considered. |
Ramp | Ramps often curves simultaneously when connecting to a road level; many measurements must be taken to ensure the right slope is maintained. |
Bridge | There are often six layers in bridge construction, all needing careful meausrement. |
Speed bump | The robot can quickly assess a speed bump profile. |
Larsen’s Land Surveying Service has been using the robot to monitor newly laid asphalt on roads and ramps during the night in order to keep the project on its tight schedule. As well, Spotland Surveyors has used the robot to monitor the single layers of asphalt during bridge construction. This requires a large number of coordinates, since measurements in many cases must be conducted within a grid of 0.5m. The robot greatly reduces the time compared to manual measuring.
A built-in setting for parking lot pre-marking allows the robot to collect three coordinates in the field and indicate the angle and the number of rows and columns in the robot’s settings. The robot also has built-in support for the marking of lines and arcs. Once again, the user can collect two coordinates for a line or three coordinates for an arc and the robot will subsequently pre-mark these elements.
Overall, the robot is very reliable and precise. Consequentially, in some cases, letting the robot enter areas that are potentially hazardous working environments keeps employees out of harm’s way.