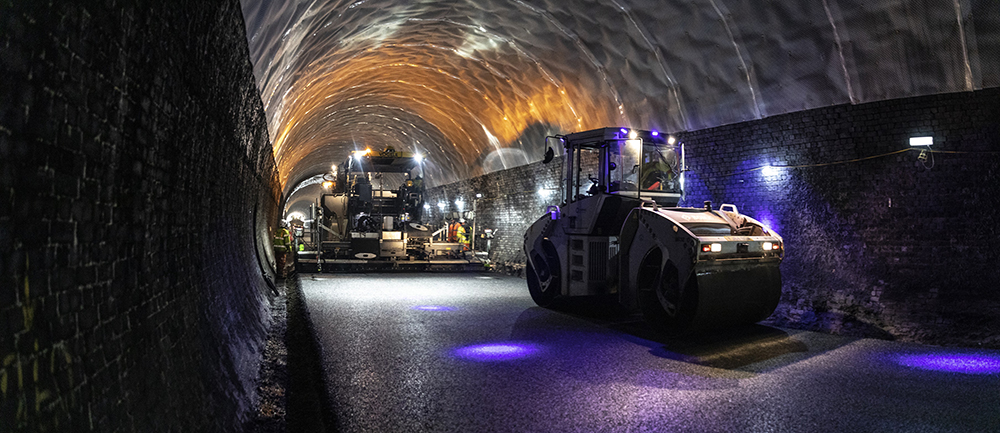
The firm has delivered a precise test track surface built to tight tolerances. The Catesby Tunnel test strip is a smooth, 2.7km stretch of flat track in Northamptonshire, UK. The former railway line and tunnel now offers suitable conditions for testing anything on wheels, ranging from supercars to bicycles.
As the track is underground it offers the capability for 24/7 testing in all weather conditions. The facility belongs to Aero Research Partners’ (ARP) Catesby Tunnel and opened in December 2021, allowing every feature of a vehicle to be tested, including aerodynamics, performance, aeroacoustics, and engine emissions.
Robert Lewis, director of Aero Research Partners, said: “We have worked closely with Stepnell, who led a professional team of great subcontractors. The team converted the tunnel from a wet hole in the ground to a pristine running surface that allows sophisticated vehicle testing.”
The tunnel removes variable conditions by offering a constant gradient of 1:176, allowing an extensive range of vehicle assessment studies to be carried out. It has a sealed working section to ensure that the environmental conditions are consistent. And it is a highly secure environment, ensuring vehicle development programmes can be conducted with confidentiality.
Tarmac laid a specially designed SMA asphalt surface, with specialist PSV 65, 10mm gritstone aggregate, that met the precise paving tolerances of less than one millimetre down to 0.3mm. The company was selected by ARP after previously successfully resurfacing the racetrack at Silverstone.
Rob Doody, managing director (Midlands region) for Tarmac, said: “The level of paving accuracy has delivered a surface with the exceptional consistency and uniformity. It enables automotive engineers to take any surface irregularity out of the equation.”
The tunnel environment meant that meticulous planning was needed. Tipper trucks could not be used so the asphalt material had to be transferred using feeders and dumpers. The asphalt supply had to be planned to ensure a continuous feed to the paver, while ventilation enabled safe working conditions to be maintained for the paving teams working in the tunnel.
To achieve the smooth finish to the test track required by ARP, Tarmac used specialist aggregate – with a Polished Stone Value (PSV) of 65 – from its Bayston Hill Quarry in Shropshire.
The quarry had earlier supplied the same stone used at Silverstone, Bahrain and Abu Dhabi Grand Prix circuits. A special mix design ensured the asphalt remained malleable while being transferred through the tunnel to the paver to ensure a quality finish.
Rob Doody added: “Achieving the specific tolerances required continuous paving along the full length of the tunnel, so we had to guarantee a continuous supply of asphalt to the paver from Tarmac plants at Mountsorrel, in Leicestershire, and the Elstow plant, near Bedford.
“In two shifts, the paving teams worked from 7am to 7pm, laying 1,340 tonnes of asphalt with a seamless changeover without stopping the paver.”